El futuro de las piezas mecánicas en China: tendencias e innovaciones
¡Bienvenido a mi blog!
¡Me encanta tenerte aquí! Antes de profundizar en el contenido, me encantaría que me acompañaras en mis redes sociales. Es donde comparto información adicional, conecto con nuestra increíble comunidad y te mantengo al tanto de las últimas noticias. Así es como puedes mantenerte conectado:
📘 Facebook: Shanghai Leierwo Industria Comercio Co., Ltd.
¡Ahora, emprendamos este viaje juntos! Espero que el contenido aquí te resulte no solo revelador, sino también inspirador y valioso. ¡Comencemos!
Tabla de contenido
Introducción
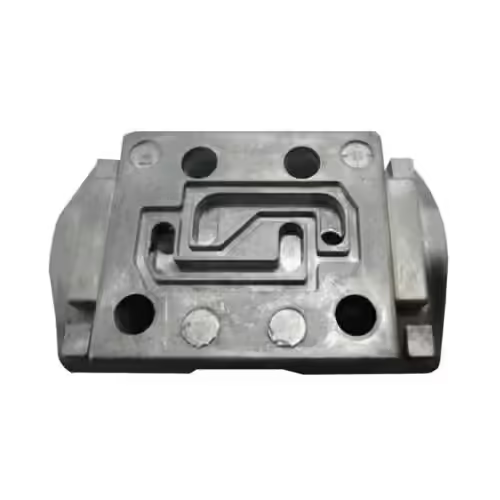
The Chinese automotive parts sector, including China mechanical parts for engines, chassis, and drivetrains, has long been a cornerstone of the global auto supply chain. In recent years this industry has been transforming rapidly – moving beyond low-cost mass production toward high-precision, high-tech manufacturing. Industry analysts note that China is now the world’s largest producer and exporter of auto parts, leveraging its vast factories and competitive costs. For buyers in the automotive sector, understanding this transformation in China mechanical parts production is crucial. We will explore how Chinese parts makers are innovating with new manufacturing technologies, advanced materials, and smart systems, and what this means for sourcing, quality, and supply chain strategy.
Despite a recent slowdown in vehicle sales, China’s mechanical parts output remains enormous. A 2024 market report finds that over the past five years China’s mechanical parts revenue still dwarfs that of any other country, reaching over $698 billion (USD) even after a modest decline. Chinese suppliers benefit from significant cost advantages and a mature logistics network, enabling them to offer a vast array of components – “everything from traditional China mechanical parts to high-tech electronic parts” – at competitive prices. In the next sections we’ll survey the key market trends and technological innovations reshaping China mechanical parts manufacturing, with a focus on the automotive industry.
Market Outlook for China Mechanical Parts
China’s automotive parts market has been under pressure from slowing domestic vehicle sales, but it remains a global China’s automotive parts market has been under pressure from slowing domestic vehicle sales, but it remains a global powerhouse. A 2024 industry report projects about a 2% annual decline in total auto parts revenue over 2018–2023, although 2023 alone saw a 6.7% rise as the market recovered. Even so, China mechanical parts output is unmatched in scale. According to one analysis, China exported roughly $75 billion of auto parts in 2023 – a 15% increase over 2022 – making it the world’s largest auto-parts exporter by a wide margin.
Major buyers of China mechanical parts include the United States, Germany, Japan and South Korea, with the US alone accounting for 25% of China’s auto parts exports.
Several factors have fueled this growth. China mechanical parts suppliers leverage high cost-efficiency and scale – large factories, affordable labor, and modern equipment drive down unit costs. Analysts note that China’s “high-cost efficiency” is a primary reason for its global leadership in auto parts. At the same time, many Chinese firms have moved up the value chain. They invest heavily in R&D to improve product quality and add advanced features (especially for electric and hybrid vehicles), narrowing the gap with established global brands. Over the past decade, the government’s Made in China 2025 initiative has also spurred this trend by prioritizing robotics, automation, and new-energy vehicles.
For automotive buyers, this means China mechanical parts suppliers can now offer a wide range of components at competitive prices with improving performance. A recent industry breakdown emphasizes China’s strengths: cost advantage, an extensive supply network, and a broad product portfolio covering everything from traditional mechanical parts to high-tech electronic parts. It also highlights challenges: some China mechanical parts still have lower global brand recognition and IP protection can be a concern. Buyers should be aware of both sides. In practice, many global automakers rely on China mechanical parts manufacturers for engine parts, suspension components, and interiors, while also keeping a close eye on quality controls and certifications.
Technological Innovations in China Mechanical Parts
China mechanical parts manufacturers are rapidly adopting advanced technologies to improve efficiency, quality, and flexibility. This smart manufacturing trend is reshaping production lines across the country. As one industry observer puts it, China’s auto parts firms are moving toward “technological upgrading and intelligent manufacturing” by integrating industrial robots, IoT sensors, and big data systems into their plants. Below we explore some of the key innovations seen in the China mechanical parts industry:
Precision Machining and CNC
Computerized numerical control (CNC) machining is a cornerstone technology for high-quality China mechanical parts. It allows metal parts to be milled or lathed to micron-level tolerances. China mechanical parts manufacturers have invested heavily in modern CNC equipment and skilled technicians. In fact, analysts note that “China has established itself as a global leader in CNC machining, providing high-quality, precision-engineered components for the automotive sector.” From cylinder blocks to gear shafts and bearing housings, CNC factories in China churn out complex parts with accuracy rivaling that of Japan or Germany.
Automation further enhances precision machining. Many China mechanical parts plants use robotic loading of parts, automated tool changers, and AI-driven process control to maintain consistency. Industry reports highlight that integrating robotics and AI with CNC mills has enabled truly automated production cells. For example, advanced CNC systems in China mechanical parts workshops can switch tools and adjust cutting parameters on the fly based on sensor feedback, minimizing errors and scrap. This results in tighter part tolerances and higher throughput. According to recent analyses, Chinese CNC shops routinely achieve tolerances down to ±0.01 mm or better on engine parts.
Overall, the emphasis on high-precision machining means that many China mechanical parts are no longer “budget-grade” throwaways, but rather precisely engineered components. For buyers, this translates into a much broader range of reliable sourcing options. Large factories in China now routinely supply critical drivetrain components (crankshafts, camshafts, transmissions) and braking system castings with consistent quality.
Additive Manufacturing (3D Printing)
In recent years, additive manufacturing (AM) has emerged as a game-changer for prototyping and low-volume China mechanical parts. China is aggressively adopting 3D printing technologies in automotive production. For example, heavy-truck OEMs in China are using large-format 3D printers to produce prototype panels, custom interiors, and even end-use structural parts. A case in point: one Chinese truck maker reports that after installing industrial 3D printers, design iterations that used to take weeks now take “just a few days.” The company achieved a 50% reduction in both time and cost for prototyping China mechanical parts by shifting from CNC to 3D-printed prototypes.
Additive processes offer key advantages for automotive components: complex geometries, lighter weight (through lattice structures), and reduced material waste. In practice, China mechanical parts suppliers use metal 3D printing for intricate prototypes and specialized fixtures. The technology is expanding into actual production: large printed panels and brackets for custom vehicles are being integrated into final products. One executive notes that large-format prints “meet the need for high-quality functional end-use parts” and eliminate time-consuming assembly steps.
From a buyer’s perspective, this means faster development cycles and greater customization of China mechanical parts. Instead of waiting for a metal tool to be fabricated, engineers can iterate designs rapidly in digital form and print them. This agility is especially valuable for aftermarket parts, specialty vehicles, or tooling in Chinese factories. As one industry report summarizes: “Additive manufacturing is increasingly used for creating high-precision parts with complex geometries, especially for small production runs or prototypes.” In the Chinese context, combining low labor cost with 3D printing means even low-volume China mechanical parts can be affordable. Automotive buyers can leverage this by working with Chinese partners who offer rapid prototyping and on-demand part production.
Robotics and Automation
Beyond CNC, China mechanical parts plants are widely embracing robotics. Spot-welding robots, multi-axis machining arms, and automated guided vehicles (AGVs) are now common on assembly floors. These robots perform repetitive tasks like welding car bodies or painting parts, freeing human workers for more skilled roles. The integration of robotics with the Internet of Things (IoT) and artificial intelligence is a hallmark of “Industry 4.0” China mechanical parts factories.
Specific examples include automated inspection machines that use cameras and sensors to verify part dimensions in real time, and predictive maintenance systems that schedule tool changes before breakdowns. According to industry sources, “Robotic arms and automation systems are used for tasks such as material handling, assembly, and inspection, reducing human error and increasing production efficiency.” The payoff is substantial: automation can boost output, improve consistency, and cut labor costs. One analysis notes that automated cells in China mechanical parts production allow for higher throughput and lower production costs, especially for complex or high-volume parts.
For automotive buyers, the robotics trend implies that China mechanical parts suppliers can offer fast, high-volume production with reliable quality. Plants with heavy automation are less vulnerable to labor shortages and can scale up quickly. Quality-wise, robots perform identical tasks the same way every time, reducing variability in China mechanical parts. Many Chinese Tier-1 suppliers now provide “lights-out” or fully-automated production lines for components like suspension struts and body panels. This maturity of automation in China’s mechanical parts sector is a key innovation trend that underscores the evolving sophistication of suppliers.
Digital Manufacturing and IoT
Alongside hardware, China’s parts industry is adopting digital technologies. Sensors and IoT platforms are being installed across factories to monitor every machine and batch. Data analytics and machine learning help optimize production schedules and predict equipment failures. A recent report highlights that “the integration of robotics, Internet of Things (IoT), and AI into precision manufacturing is transforming the sector”, enabling smarter factories. For example, in a Chinese engine plant, IoT sensors track cutting-tool wear; analytics then automatically schedule tool replacements to maintain tolerances. In logistics, some large parts mills use blockchain for supply-chain traceability, assuring buyers of material provenance.
This move toward digitalization means Chinese parts suppliers can offer improved transparency and responsiveness. Buyers can, for instance, request real-time production updates or quality reports from their Chinese vendors. The rise of “smart factories” is aligned with global trends, and China’s scale makes it a leading proving ground. As these systems mature, we expect to see even more customized production (small batches made economically) and better quality control, further raising the bar for China mechanical parts.
Advanced Materials and Lightweight Design
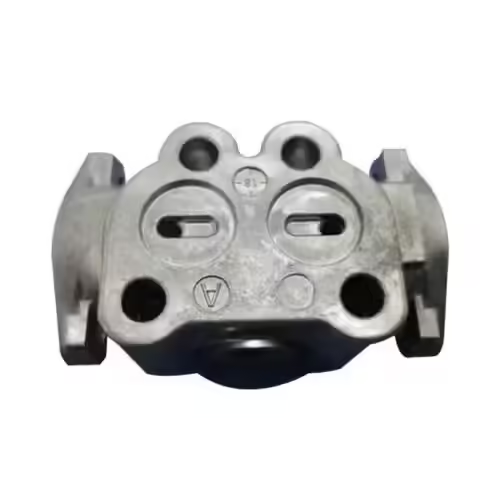
Meeting tightening fuel economy and emissions regulations is another driver of innovation. Automakers worldwide are pursuing lighter vehicles, and suppliers of China mechanical parts are responding with new materials and designs. In China, this trend is evident in the adoption of aluminum alloys, magnesium, and fiber-reinforced composites for components traditionally made of steel.
China’s government and industry often emphasize “light-weighting”. For example, a BASF industry report notes that Chinese regulators view weight reduction as a key way to improve fuel efficiency and meet carbon targets. In practice, china mechanical parts manufacturers are increasingly fabricating components like engine blocks, chassis beams, and knuckles out of aluminum or high-strength steel. Composite materials (carbon fiber reinforced polymer, CFRP) are gaining traction, especially for body panels and interior trim. A few China mechanical parts suppliers now offer carbon fiber leaf springs and subframe components for specialty vehicles.
The benefit to buyers is twofold: lighter parts can help automakers meet efficiency targets, and advanced materials often allow new designs that integrate multiple functions (e.g., a bearing housing that doubles as a cooling manifold). China’s automotive materials sector is growing – one source predicts the precision manufacturing market (which includes materials processing and china mechanical parts) could reach over $600 billion by 2030, partly driven by these lightweight technologies. Buyers looking for cutting-edge mechanical parts should watch for china mechanical parts suppliers specializing in high-end materials. Many Chinese firms are now certified to OEM standards for aluminum castings and composite molding, meaning they can deliver parts that rival Western manufacturers in both weight and strength.
Electrification’s Impact on China Mechanical Parts
The rise of electric and hybrid vehicles (EVs/HEVs) is having a profound effect on piezas mecánicas de China demand. As China leads the world in EV production (tens of millions of units per year), suppliers are shifting their product mix. Traditional components like pistons, camshafts, and exhaust systems become less critical, while new parts emerge: e-motors, battery housings, power electronics enclosures, and regenerative braking modules.
China mechanical parts companies have actively retooled. Many are developing new-energy vehicle (NEV) components. For instance, china mechanical parts manufacturers are expanding production of battery management systems, electric drive motors and controllers – essentials for EVs. Domestic giants in battery tech and electric drives mean that Chinese supply chains are especially strong for these EV-specific parts. Even “mechanical” parts have evolved: electric powertrains use gearboxes and axles optimized for high torque, and they require lightweight supports and improved thermal management components.
Automotive buyers should note that china mechanical parts suppliers often combine mechanical expertise with electrical innovation. As one industry report highlights, “China surpasses all other countries by leading the production of electric vehicles with their essential components, such as batteries and electric drive systems”. The implication is that china mechanical parts in the EV era often integrate electronics – for example, a motor housing might include integrated cooling channels and sensor mounts. Buyers sourcing parts like electric motor rotors or chassis subframes for EVs can find competitive options in China, but should verify compatibility with their EV platforms.
It is also worth mentioning that the pace of EV adoption has been astonishing. New car sales in China now see EVs plus hybrids (NEVs) reach over 20% share, with targets to rise further. This creates enormous demand for new types of piezas mecánicas de China. Chinese suppliers’ deep experience with batteries (for consumer electronics) is a boon; they bring that scale and cost advantage to auto batteries. For conventional piezas mecánicas de China in BEVs, the focus is on durability under high-load electric motors (which can have much higher RPMs than an ICE). Chinese parts makers are developing hardened gears and bearings to meet these needs.
In summary, electrification is transforming what “mechanical parts” means. Buyers should partner with piezas mecánicas de China manufacturers who are investing in EV-ready components. Many traditional parts makers have launched new divisions or acquired tech startups to stay relevant. Overall, the trend favors suppliers that offer the right combination of mechanical precision and new-energy expertise.
Global Supply Chain and Trade Dynamics
China’s mechanical parts industry is deeply entwined with global automotive supply chains. Major OEMs source a significant portion of their parts from Chinese factories – not only for vehicles built in China but often for export models as well. For example, engines and transmissions assembled in China may go into cars sold worldwide. A recent study finds that companies like GM, VW, and Toyota “heavily depend on Chinese-made components” for their assemblies.
This global role has grown steadily. Chinese parts suppliers are pursuing overseas expansion: they have been acquiring foreign companies and forming joint ventures. Notable examples include Geely’s purchase of Volvo and Wanxiang’s acquisition of the former Saab (Fisker) assets, giving Chinese firms deeper technology and market access. These moves help Chinese parts makers improve their capabilities and credibility. Supply chain experts expect such M&A activity to continue, with Chinese capital flowing into overseas precision manufacturing assets.
For automotive buyers, this means the China mechanical parts supply chain is both vast and complex. On one hand, China’s location near raw material sources and its refined logistics network mean deliveries are often reliable and fast. On the other hand, buyers now consider geopolitical and logistical risks. Lessons from the COVID-19 disruptions have shown that overreliance on any one region (including China) can be risky. Many global firms are adopting a “China+1” strategy – keeping China as a production hub but also building capacity in Southeast Asia, India, or North America.
Key considerations in this domain include:
- Trade Policies: Ongoing US-China trade tensions and tariffs can affect parts pricing and availability. Buyers must track changing regulations (e.g. Section 301 tariffs, new rules of origin) that impact Chinese parts imports.
- Quality Certifications: Global OEMs require ISO/TS certifications or IATF 16949 quality standards for tier-1 suppliers. Buyers should verify that any Chinese mechanical parts supplier meets these standards.
- Logistics and Lead Times: While Chinese manufacturers often promise fast delivery, shipping times and port congestion can cause delays. Diversifying ports and shipping lines is advisable.
- Currency Fluctuations: The Chinese yuan’s value can affect part costs. Buyers sometimes use forward contracts or price adjustments to mitigate this risk.
- Supplier Audits: Given brand and IP concerns, thorough supplier audits and warranty terms are important. Many buyers send technical teams to Chinese plants for inspections and capability assessments.
Despite these challenges, China’s role in the supply chain is set to remain huge. Analysts predict China will “boost its position as a leading exporter of automotive parts throughout the international marketplace”, thanks to continued investment in technology and manufacturing capacity. For buyers, the strategy is to take advantage of China’s strengths (cost and scale) while building risk mitigation into procurement plans.
Quality Assurance and Standards
As Chinese mechanical parts have matured, quality assurance has become a major focus. Historically, one criticism was that Chinese suppliers produced parts that met cost targets but not always the tight tolerances or durability expected by high-end OEMs. This is changing: many plants now operate under strict quality systems. According to industry reports, Chinese auto component manufacturers “put large resources into R&D” to improve both electric and traditional components. Over the last decade, the average precision of Chinese-made parts has steadily increased.
Buyers should still exercise caution. A recent trade survey found that some foreign partners remain reluctant to transfer their latest technologies to Chinese firms, reflecting ongoing concerns about intellectual property and quality control. However, Chinese suppliers have incentives to improve. To compete globally, they are obtaining international certifications and investing in lab testing. Many now produce parts that meet or exceed EU or US automotive standards. For example, Chinese foundries that make engine blocks are often IATF 16949 and ISO 9001 certified, and steel parts may carry CE or RoHS marks when needed.
Several tips for buyers:
- Check Certification: Ensure any Chinese supplier has the required quality certifications and track records with reputable OEMs. Trusted tiers will readily provide audit reports and performance metrics.
- Inspect Samples: Before mass production, get prototype parts and measure them against specifications. Chinese factories are accustomed to this and often have flexible production to refine prototypes.
- Watch IP: If your product design is proprietary, use confidentiality agreements. While IP laws in China are strengthening, it’s prudent to treat critical designs carefully.
- Seek Local Partnerships: In some cases, co-developing parts with a Chinese partner can help transfer knowledge and ensure quality. Several Western companies have set up technical centers in China to collaborate on new parts.
Overall, the quality of China mechanical parts is no longer uniformly low. Many suppliers now match global standards. As one expert observed: local Chinese suppliers are “good at mechanical parts” – meaning they can produce robust, reliable components – even if they historically needed help integrating electronics. The buyer’s role is to identify and work with the high-performing suppliers within China’s huge pool.
Sustainability and Environmental Trends
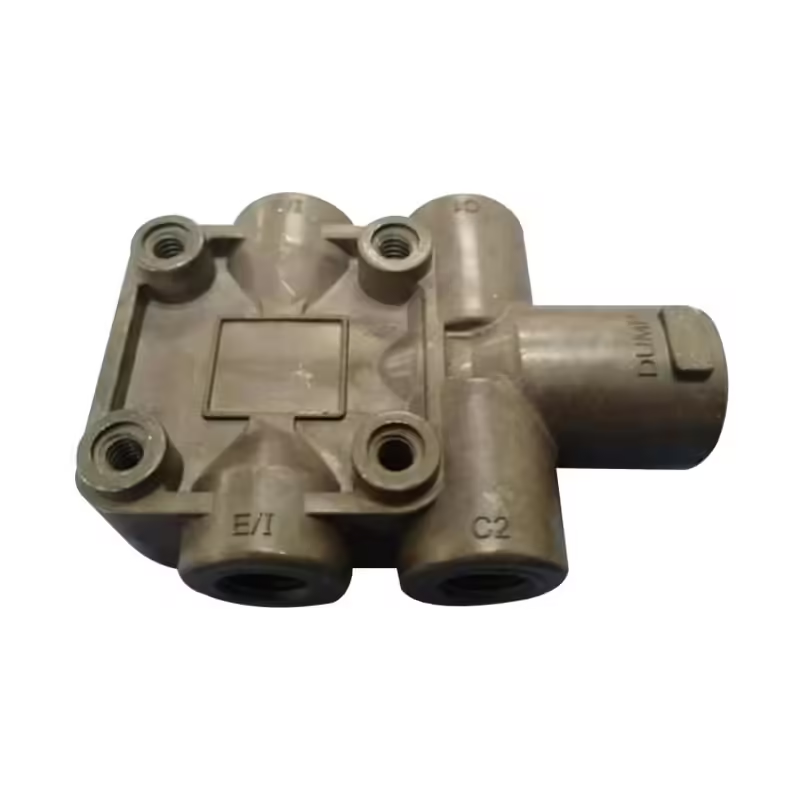
Environmental concerns and regulations are increasingly shaping China’s automotive parts sector. China has pledged to peak carbon emissions by 2030, and the auto industry is a major focus. The government’s automotive plans explicitly emphasize “energy conservation and emission reduction” as top priorities. In practice, this translates into several trends affecting mechanical parts:
- Lightweighting – As discussed earlier, developing lighter parts directly reduces vehicle fuel use or extends EV range. Chinese manufacturers are investing in advanced alloys and design techniques (like hollow structures) to shed weight. The market demand for lightweight components is growing rapidly.
- Clean Production – Many Chinese parts plants are upgrading to more efficient equipment. For example, automated spray booths reduce paint and solvent waste; modern furnaces burn cleaner with lower particulates. Firms are also adopting wastewater recycling and metal scrap recycling. Some suppliers report having reduced their per-part energy use by 10–20% through such measures.
- Renewable Energy Use – Large auto part factories in China have started installing solar panels or sourcing green energy to power their factories. This helps automakers meet the “green supply chain” criteria that many OEMs require today.
- Recyclability – With the surge in used EV batteries and parts expected, Chinese materials firms are developing recycling processes for metals and plastics from vehicles. Over time, auto parts may be manufactured with a higher percentage of recycled content.
These shifts have dual benefits. They help China meet international environmental commitments, and they align with customer preferences for sustainable sourcing. Buyers can look for Chinese parts suppliers that advertise their green credentials, such as carbon-neutral production certifications or compliance with global environmental standards (ISO 14000 series). In some cases, sourcing a more environmentally friendly part from China can become a value-add – for instance, claiming a lower lifecycle carbon footprint in the final vehicle assembly.points out that Chinese automakers know that “low carbonization is the inevitable trend for future vehicles” and that advanced materials are needed to meet stricter fuel-consumption limits.
The mechanical parts segment is directly impacted: by using new metals and designs, both engine efficiency and EV performance improve. As the automotive industry worldwide moves toward sustainability, China’s parts makers are adapting their innovation pipeline accordingly. We expect to see more products like green composites, energy-efficient manufacturing technologies, and full supply-chain transparency from China in coming years.
Challenges and Opportunities
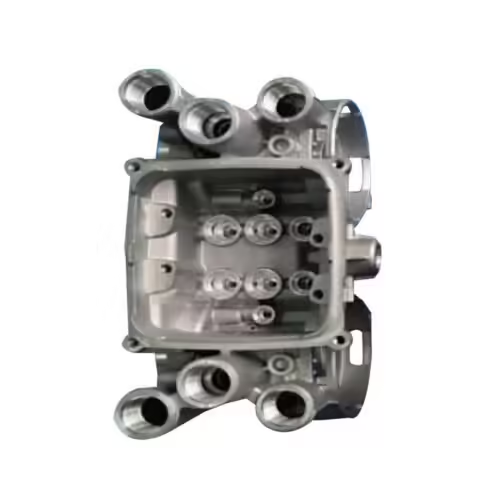
Despite the positive trends, the China mechanical parts sector faces challenges. Understanding these is key for buyers to navigate the market effectively.
Challenges:
- Intellectual Property (IP) and Branding: Chinese parts suppliers have improved, but many still struggle with brand recognition overseas and full IP compliance. Buyers often perceive quality variation, especially from lesser-known firms. According to a sourcing analysis, Chinese companies need stronger IP protections and brand building to gain trust. This means buyers should verify patent and design protections when collaborating.
- Electronic Integration Gaps: As noted in industry reports, local Chinese suppliers excel at mechanical components but are sometimes behind on electronics and mechatronics integration. With modern cars requiring fully integrated modules, this gap can pose challenges. Buyers of systems (not just bare parts) may need to ensure the Chinese supplier can integrate sensors and controls, or else consider international partners.
- Regulatory Uncertainty: Trade policies and environmental regulations change. For example, stricter vehicle emission rules may phase out some legacy part types, requiring new designs. Tariffs and geopolitical issues could also disrupt supply or raise prices. Buyers need to stay informed about Chinese market policies (like local content requirements or export duties) and adjust sourcing strategies.
- Labor and Cost Pressures: China’s labor costs have been rising, and raw material prices can be volatile. In some cases, Chinese suppliers may no longer be the absolute cheapest source for commodity parts (as cheaper labor emerges in Southeast Asia). Buyers should continuously benchmark costs and be prepared to negotiate or shift production if more cost-effective alternatives exist.
Opportunities:
- Scale and Variety: The biggest opportunity remains China’s sheer scale. For large-volume needs, Chinese suppliers can ramp up production faster than almost any other country. They also offer an enormous variety of part types – from stamped metal brackets to precision hydraulics – often under one roof. Buyers can consolidate supply chains by sourcing multiple parts from a few Chinese partners.
- Electric Mobility Leadership: As mentioned, China dominates EV production. This means its parts suppliers are likely ahead on EV-specific components. Buyers looking to develop electric cars or trucks can tap into this expertise and cost advantage. Chinese firms already account for a major share of global EV battery and motor output.
- Aftermarket Growth: China’s massive vehicle parc (billions of cars) creates a huge domestic aftermarket. Chinese suppliers are geared toward producing spare parts (mechanical and electronic) at low cost. Global buyers in the replacement parts market can benefit by sourcing from China, especially for high-volume items like filters, bearings, or chassis components where brand equality is less critical.
- Innovation Adoption: Many Chinese parts makers are quick to try new processes, sometimes faster than older Western firms. For example, the rapid adoption of 3D printing or digital twins in Chinese factories means innovative solutions can emerge there. Buyers who want cutting-edge prototypes or custom solutions may find more agile development from Chinese manufacturers.
By carefully vetting suppliers and staying aware of these dynamics, automotive buyers can turn China’s mechanical parts industry to their advantage. The future promises strong innovation-driven growth for China’s auto parts sector – something global buyers cannot afford to ignore.
Conclusión
China’s mechanical parts industry is at a crossroads: blending its traditional cost and capacity advantages with a new emphasis on technology and sustainability. For automotive sector buyers, this means access to an unprecedented range of components. From ultra-precision CNC machined engine blocks to lightweight composite structural parts, Chinese suppliers are expanding their capabilities. The embrace of automation, robotics, and digital tools is making production faster and more consistent. Meanwhile, the electric vehicle revolution is spawning whole new categories of “mechanical” components made in China, backed by the country’s massive EV market.
At the same time, buyers should remain diligent. Quality assurance, intellectual property, and supply chain risks require active management. Partnering with top-tier Chinese manufacturers – those with proven quality systems and export experience – is key. Analysts agree that the future of China’s auto parts industry is bright: continued investment in R&D, smart manufacturing, and green processes will keep Chinese firms competitive internationally. In practical terms, this means that automotive component buyers should view China not just as a source of cheap parts, but as a hub of innovation. By understanding the trends outlined above, buyers can make informed sourcing decisions and gain an edge in a rapidly evolving market.
PREGUNTAS FRECUENTES
How are Chinese mechanical parts manufacturers improving quality and innovation?
Chinese suppliers have dramatically upgraded their capabilities in recent years. Major factories now implement automated CNC machining, robotics, and IoT monitoring to tighten tolerances. Many firms focus on R&D for electric vehicle components and advanced materials. The result is that today’s Chinese-made mechanical parts can match international standards in precision and durability. Buyers also benefit from rapid prototyping via 3D printing, which Chinese companies use to slash design cycles.
Why should automotive buyers consider sourcing mechanical parts from China?
The primary appeal is cost and range. China produces components at very low labor cost, which translates into competitive pricing for high-volume parts. Additionally, Chinese suppliers offer a wide portfolio of parts under one roof – everything from engines and transmissions to chassis and bearings. For specialized or emerging technologies (like EV drivetrains), China’s scale means they often have the capabilities already in place. Global brands can leverage Chinese manufacturing strength, provided they manage quality and compliance carefully.
What challenges should we watch out for when buying from China?
Key issues include quality consistency, intellectual property protection, and supply-chain risk. Although many Chinese factories meet rigorous quality standards, buyers must verify certifications (ISO/TS, IATF) and perform audits. IP concerns persist, so use non-disclosure agreements and consider splitting design across suppliers if needed. Also account for trade factors: tariffs or shipping delays can impact timing. It’s wise to maintain alternative sources (“China+1”) and build inventory buffers for critical parts.
How will the shift to electric vehicles affect the demand for Chinese mechanical parts?
Electrification changes the parts mix but not the importance of China as a supplier. While fewer piston-driven engines are needed, Chinese firms are leaders in EV-related components like battery packs, electric motors, and power electronics housings. They are also adapting existing mechanical parts (e.g. lighter aluminum transmissions) for EV use. In fact, with EVs now over 20% of Chinese car sales, buyers will find robust Chinese supply for all the new mechanical parts EVs require. Conversely, for declining ICE-specific parts, China still offers cost-effective inventory production as global manufacturers scale down combustion engine programs.
What impact does China’s national policy have on mechanical parts production?
China’s industrial policy – notably Made in China 2025 – pushes domestic manufacturers to adopt advanced tech and upgrade product quality. In practice, this has accelerated the use of robotics, automation, and new materials in parts plants. The government also promotes EV and NEV development aggressively, which indirectly boosts parts suppliers to focus on EV drivetrains. For importers, this means Chinese mechanical parts are increasingly made with modern processes, potentially reducing quality risk. However, it also means China may pursue self-sufficiency in certain core technologies, so buyers should monitor policy shifts that could affect technology transfer or component availability.
Categorías de productos
- Piezas de válvulas
- Piezas de la bomba de agua
- Piezas de la caja de cojinetes
- Piezas de fundición a presión
- Productos para bombas de acero inoxidable
- Productos para bombas de hierro fundido
- Piezas de válvulas para automóviles
- Recambios para automóviles
- Piezas de válvulas para uso civil
- Piezas de bomba de vacío KF
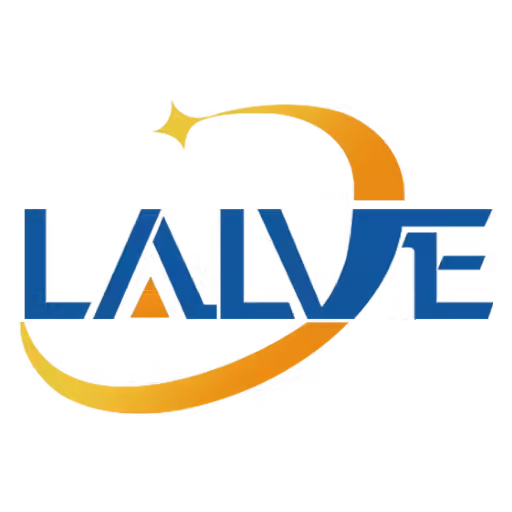