Cómo la fundición en arena de resina transforma la fundición de metales
¡Bienvenido a mi blog!
¡Me encanta tenerte aquí! Antes de profundizar en el contenido, me encantaría que me acompañaras en mis redes sociales. Es donde comparto información adicional, conecto con nuestra increíble comunidad y te mantengo al tanto de las últimas noticias. Así es como puedes mantenerte conectado:
📘 Facebook: Shanghai Leierwo Industria Comercio Co., Ltd.
¡Ahora, emprendamos este viaje juntos! Espero que el contenido aquí te resulte no solo revelador, sino también inspirador y valioso. ¡Comencemos!
Tabla de contenido
Introducción
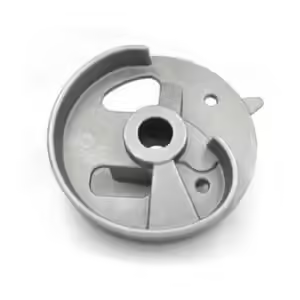
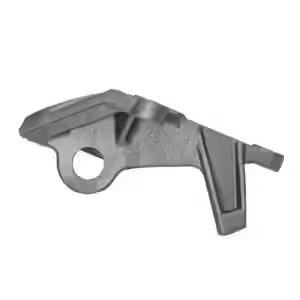
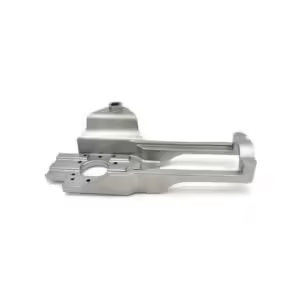
Resin sand casting is a highly efficient and versatile process in the metal casting industry, offering numerous advantages over traditional sand casting methods. In resin sand casting, a mixture of fine sand and a resin binder is used to create molds for metal components. This process allows for the production of complex and precise parts with minimal defects, making it ideal for industries such as automotive, aerospace, and heavy machinery. Unlike other casting methods, resin sand casting offers faster turnaround times, improved mold strength, and the ability to create intricate shapes with ease.
This article explores how resin sand casting is revolutionizing the metal casting process, its advantages, challenges, and why it is becoming the preferred choice for manufacturers.
The Advantages of Fundición en arena de resina
1. Improved Mold Strength and Durability
One of the most notable benefits of this casting technique lies in the exceptional strength and durability of the molds it produces. By incorporating high-quality resin binders into fine sand, the process significantly reinforces the mold structure, allowing it to endure the intense heat and pressure of molten metal pouring without breaking or deforming.
Compared to traditional green sand molds, this method offers far superior mechanical stability. The hardened molds maintain their shape even under harsh thermal and mechanical stress, resulting in castings with improved dimensional accuracy and smoother surface finishes. This is especially valuable in applications requiring strict tolerances, such as engine components, aerospace housings, and precision mechanical parts.
Furthermore, the increased structural integrity of the mold allows for the creation of thin walls and intricate geometries, which are typically more prone to failure in conventional sand casting. Industries demanding lightweight but durable components—like automotive, defense, or aviation—can benefit significantly from the precision and reliability of this approach.
2. Faster Turnaround Times
Unlike traditional sand casting, which often involves multiple steps including drying, this modern process accelerates production by utilizing faster-curing resin materials. The chemical hardening of the sand-resin mixture eliminates the need for prolonged baking or setting periods, which drastically reduces cycle times.
This shortened production time translates into higher efficiency for manufacturers, particularly those handling low to medium-volume production or custom prototyping. The ability to quickly switch between part designs or respond to urgent orders gives companies a competitive edge in industries where lead time is critical, such as heavy machinery, construction equipment, or industrial tooling.
Additionally, because the molds are more stable and precise, there’s less likelihood of errors or defects, which in turn reduces the need for rework or remanufacturing. The cumulative effect is not only faster delivery but also greater cost-efficiency throughout the production chain.
3. Ability to Produce Complex Shapes with High Precision
A major strength of this method is its ability to replicate intricate and detailed designs with remarkable accuracy. The high cohesion of the sand-resin blend allows it to conform tightly around patterns, capturing fine features and ensuring that even the most complex shapes are faithfully reproduced.
This characteristic reduces the amount of post-casting machining required. In many cases, parts can be used with minimal finishing, saving both time and labor. For example, when manufacturing components like turbine blades, pump housings, or gearboxes, this process helps reduce dimensional deviations and preserves critical design elements.
Moreover, the molds can support thinner walls and more refined profiles without collapsing—features that are often essential in high-performance parts. Engineers can optimize designs for weight, functionality, and thermal efficiency, which is increasingly important in sectors like electric vehicles, robotics, and energy systems.
El Fundición en arena de resina Process
1. Preparation of Sand and Resin Mixture
The first step involves blending high-quality silica sand with a liquid or powdered resin binder. This mixture forms the basis of the mold. Different resins—such as furan, phenolic, or urethane types—are selected depending on the thermal, chemical, and structural demands of the final casting. Additives may also be introduced to improve workability, curing speed, or surface quality.
Proper control of the sand-to-resin ratio and curing conditions is essential. A well-mixed composition ensures consistent mold hardness, uniform thermal behavior, and excellent surface finish.
2. Mold Making
Once the sand-resin compound is ready, it is packed into a mold box or flask, often around a pre-formed pattern. Vibratory compaction may be used to remove air pockets and ensure dense packing. The pattern defines the external shape of the part, while internal features—such as holes or hollow passages—are formed using separately prepared cores, which are also made from the same resin-treated sand.
The molds and cores harden either through ambient curing or accelerated thermal processes. Once cured, the pattern is removed, and the mold is assembled and prepared for pouring.
3. Metal Pouring and Cooling
Molten metal—such as iron, aluminum, or steel—is then poured into the mold cavity. Thanks to the robust structure of the cured mold, it can easily handle high-temperature metals without distorting or cracking. This ensures that the shape and detail of the casting are preserved during solidification.
The mold is allowed to cool naturally, and once the metal has solidified, the sand mold is broken away. This step is typically easier than with traditional ceramic molds, as the sand can be reclaimed or recycled after use.
4. Post-Casting Processes
After demolding, the raw casting undergoes a series of finishing operations. These may include shot blasting to remove any sand residue, machining to achieve tighter tolerances, and heat treatment to improve mechanical properties.
One of the key benefits of using this technique is that many parts require minimal machining, thanks to the high precision of the molding process. This is especially advantageous for complex components that would be expensive or time-consuming to machine from solid stock.
Challenges in Fundición en arena de resina
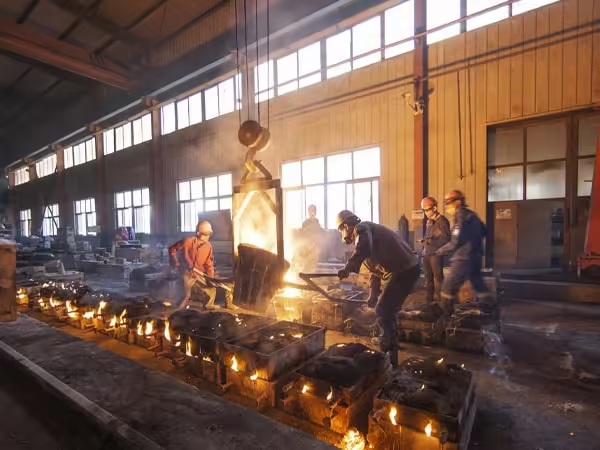
1. Cost Considerations
While the benefits are numerous, the process does come with certain cost implications. The resin binders and additives used are typically more expensive than water and clay used in green sand casting. Additionally, specialized mixing equipment, mold handling systems, and environmental controls may be required to manage the materials and emissions effectively.
However, these higher upfront costs are often justified by reduced labor, less rework, and better part quality. For industries that demand performance and consistency, the investment is well worth the return.
2. Environmental Impact
Some of the resins used in this process can emit volatile organic compounds (VOCs) during mixing or curing. These emissions pose potential health and environmental hazards if not properly controlled. Therefore, adequate ventilation, emissions filtering systems, and personal protective equipment (PPE) are essential in facilities using this method.
In response to increasing environmental regulations and industry demand for greener solutions, manufacturers are exploring low-emission resins, reclaimable sand systems, and bio-based binders. These innovations aim to reduce the ecological footprint of the process while maintaining performance standards.
Applications of Fundición en arena de resina
Resin sand casting has found applications in various industries, including automotive, aerospace, defense, and heavy machinery. Its ability to produce high-precision parts with complex geometries makes it particularly useful in applications where durability and performance are critical. Below is a table showcasing some common applications of resin sand casting and the benefits it offers:
Industry | Aplicación | Benefits of Resin Sand Casting |
---|---|---|
Automotive | Engine blocks, transmission parts | High precision, fast production cycle |
Aerospace | Turbine blades, engine components | Complex shapes, lightweight structures |
Defense | Gun parts, military hardware | High strength, durability |
Heavy Machinery | Gearboxes, hydraulic components | Improved mold strength, minimal defects |
Conclusión
Resin sand casting is revolutionizing the metal casting process by offering enhanced precision, faster production cycles, and the ability to produce complex shapes with high strength. As industries demand more complex and precise components, resin sand casting has proven to be a reliable and efficient method that meets these needs. Although there are challenges such as cost and environmental impact, the benefits of resin sand casting often outweigh these concerns, making it a preferred choice for many manufacturers.
PREGUNTAS FRECUENTES
What is the primary advantage of resin sand casting over traditional sand casting?
The primary advantage of resin sand casting is the superior strength and precision of the molds, which allows for the production of more intricate and detailed parts with fewer defects.
Is resin sand casting suitable for large-scale production?
Yes, resin sand casting is suitable for both small and large-scale production, offering quick turnaround times and high-quality results.
Can resin sand casting be used for aluminum casting?
Yes, resin sand casting is commonly used for aluminum casting, especially when high precision and complex geometries are required.
What industries benefit the most from resin sand casting?
Industries such as automotive, aerospace, defense, and heavy machinery benefit greatly from the precision and durability offered by resin sand casting.
Are there any environmental concerns with resin sand casting?
Yes, there are environmental concerns regarding the disposal of resin materials. However, efforts are being made to find more eco-friendly alternatives and improve recycling practices.
Categorías de productos
- Piezas de válvulas
- Piezas de la bomba de agua
- Piezas de la caja de cojinetes
- Piezas de fundición a presión
- Productos para bombas de acero inoxidable
- Productos para bombas de hierro fundido
- Piezas de válvulas para automóviles
- Recambios para automóviles
- Piezas de válvulas para uso civil
- Piezas de bomba de vacío KF
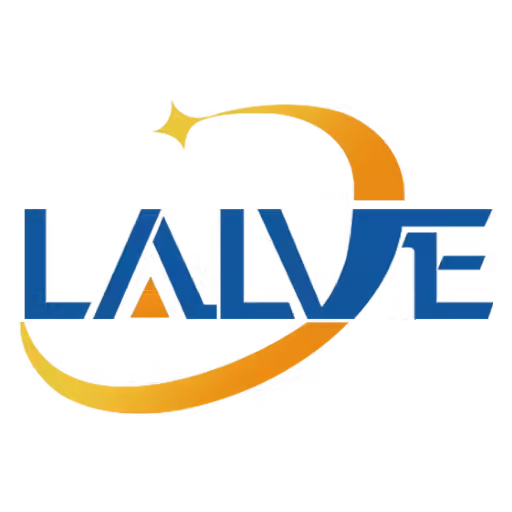