Avoid These Cast Iron Impeller Quote Traps
¡Bienvenido a mi blog!
¡Me encanta tenerte aquí! Antes de profundizar en el contenido, me encantaría que me acompañaras en mis redes sociales. Es donde comparto información adicional, conecto con nuestra increíble comunidad y te mantengo al tanto de las últimas noticias. Así es como puedes mantenerte conectado:
📘 Facebook: Shanghai Leierwo Industria Comercio Co., Ltd.
¡Ahora, emprendamos este viaje juntos! Espero que el contenido aquí te resulte no solo revelador, sino también inspirador y valioso. ¡Comencemos!
Tabla de contenido
Introducción
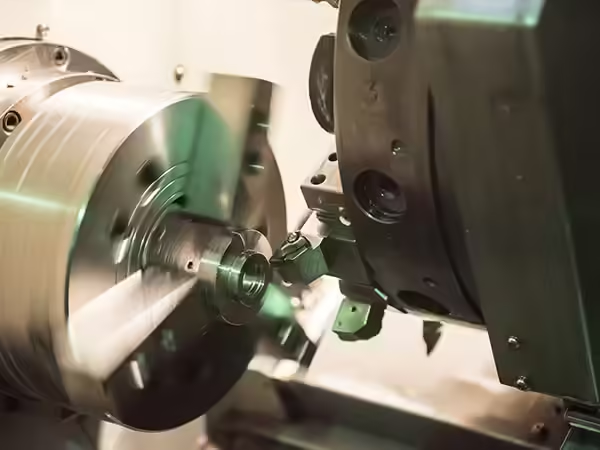
Getting the right cast iron impeller quotes seems like a straightforward task—but in reality, it’s full of nuances that many buyers overlook. Whether you’re replacing a pump impeller, preparing for a large manufacturing run, or sourcing components for industrial systems, understanding how quotes are structured—and where they might mislead—is critical to avoiding unnecessary costs and delays.
This article will walk you through the most common traps in the quote process, show you what details to ask for, and help you become a more confident and informed buyer. From material specs to shipping terms, from inspection standards to MOQ clauses, this guide equips you to assess cast iron impeller quotes like a professional.
Why cast iron impeller quotes Can Be Misleading
At first glance, quotes for cast iron impellers may appear comparable. You receive documents that list impeller descriptions, quantities, and estimated lead times. But what’s hidden beneath the surface is just as important as what’s written on the page. That’s because numerous variables affect the final cost, quality, and delivery experience of an impeller order.
Factors such as casting method, heat treatment, machining precision, and shipping responsibilities can all vary. If you’re not vigilant, you might accept a low quote that turns expensive later—or worse, receive parts that don’t match your system’s performance needs.
Key reasons why quotes vary widely include:
- Material ambiguity: Cast iron can come in many forms—gray, ductile, high-chromium alloyed. Some suppliers don’t clearly indicate which they’re quoting for.
- Casting quality: Investment casting offers better tolerances but costs more than sand casting. Many quotes fail to clarify which process is used.
- Coatings and finishing: An impeller might require anti-corrosive coatings, dynamic balancing, or precise trimming—all of which may or may not be included.
- Testing and certifications: Some vendors include full quality control testing and material certificates in the quote, while others charge extra for them—or omit them entirely.
- Incoterms confusion: Shipping costs and import duties depend on whether a quote is based on EXW, FOB, CIF, or DDP terms. Many buyers get caught off-guard by unexpected freight charges.
Understanding the full scope behind cast iron impeller quotes is essential to avoiding unpleasant surprises. The cheapest-looking quote may end up being the costliest in the long run.
Five Common Traps Found in cast iron impeller quotes
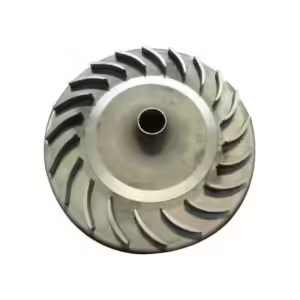
Here are the most frequent and costly traps hidden in impeller quotes—and how you can avoid them.
Vague or Incomplete Material Specifications
When a quote simply states “cast iron impeller” without naming the exact alloy or standard, it’s a red flag. Not all cast iron is the same. The mechanical strength, corrosion resistance, and heat tolerance differ drastically between gray iron and ductile iron. Receiving impellers made of the wrong material could lead to premature failure or incompatibility with your pump housing.
Request explicit material designations such as ASTM, ISO, or GB standards. If your application has specific chemical resistance requirements, ask for chemical composition reports or data sheets to verify.
Ambiguous Manufacturing Process and Surface Finish
Another common trap is the absence of details about how the impeller is manufactured. Sand casting, for instance, has looser tolerances than investment casting or lost foam methods. If the quote does not specify the process, you cannot predict the precision or reliability of the final product.
Similarly, quotes often leave out details about surface finish, trimming, polishing, or balancing—all critical for pump performance. High surface roughness or imbalance can affect efficiency, vibration, and wear.
Always ask vendors to describe their casting process, and whether impellers are dynamically balanced or statically balanced, as this significantly affects long-term performance.
Unrealistic or Undefined Lead Times
Quotes that say “fast delivery” or “as soon as possible” are a common trap. These vague phrases give buyers a false sense of urgency or optimism but lack real commitment. When the actual order is placed, production lead time may stretch far beyond your expectations.
Insist on clearly stated production and shipping schedules. Ask the supplier to define the lead time in terms of calendar days and specify whether it starts from the date of purchase order, payment, or drawing approval. Inquire about rush options, but also verify if they come with a premium.
Hidden Shipping and Handling Costs
Shipping heavy items like cast iron impellers comes with significant logistical complexity and cost. Some suppliers provide quotes that appear competitive but omit packaging, freight forwarding, customs duties, or insurance. You may only discover these omissions when the invoice arrives or when your shipment gets stuck at customs.
To avoid this trap, request quotes that clearly define Incoterms—especially whether it includes Delivery Duty Paid (DDP), Cost and Freight (CFR), or Free on Board (FOB). Be sure to ask about the packaging standards, palletization, and export documentation, all of which may add to the cost.
Unclear Quantity Requirements or Price Brackets
A quote that looks attractively low might be valid only for high-volume orders. Without specifying Minimum Order Quantity (MOQ) or price breaks for different tiers, you may assume the listed price applies to small orders—only to discover it doesn’t.
Clarify what order sizes the quote is based on. If you’re ordering small quantities for prototyping or maintenance, you’ll need vendors who accommodate low-volume runs. Conversely, if you’re purchasing in bulk, ensure the pricing reflects that and request discounts accordingly.
Comparing Common Elements in cast iron impeller quotes
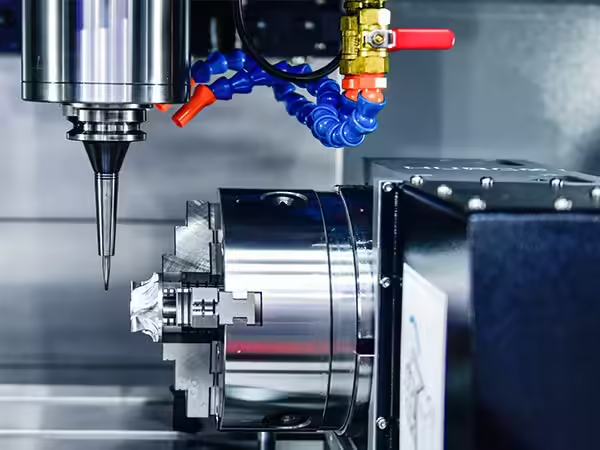
Here’s a summary table showing what to check in a quote and why it matters.
Element | What to Look For | Importance |
---|---|---|
Material Type | Specify gray iron, ductile iron, ASTM standard, etc. | Ensures mechanical and chemical compatibility |
Casting Method | Sand, investment, or lost foam casting | Affects dimensional accuracy and surface finish |
Surface Finish | Indicate polishing, dynamic balancing, coating options | Impacts performance and durability |
Plazo de entrega | Clearly defined in days from order or payment | Avoids project delays |
Incoterms | FOB, CIF, DDP, etc. | Determines who bears responsibility for logistics |
Packaging & Documentation | Palletized, vacuum sealed, with export docs | Reduces shipping damage and customs clearance delays |
MOQ & Price Tiers | Minimum quantity for quoted price | Prevents surprises in final invoice |
Certification | Material test reports, inspection data, balance certificates | Confirms quality, especially for regulated industries |
How to Request Better cast iron impeller quotes
Now that you’re aware of the pitfalls, here’s how to structure your RFQ (Request for Quotation) to avoid problems:
- Include Technical Specifications
Don’t just ask for an impeller—provide your pump model, performance data (flow rate, head, RPM), material preferences, trim diameter, shaft fitment, and any corrosion or pressure requirements. - Ask for Quality Documentation
Request material test certificates (MTCs), balance test results, and visual inspection reports. For high-performance or regulated applications, demand compliance with relevant standards. - Clarify Delivery Expectations
Define your delivery location and ask for total delivery lead time, including production and shipping. Specify if you’re requesting sea freight or air freight timelines. - Request Detailed Pricing
Insist on an itemized quote that separates base product cost, tooling charges (if any), optional features (e.g. coatings), packaging, documentation, and freight. - Discuss After-Sales Support
Find out about warranties, return policies, and whether the vendor provides technical support in case of failure or misfit.
A Real-World Comparison: Smart Quote vs. Risky Quote
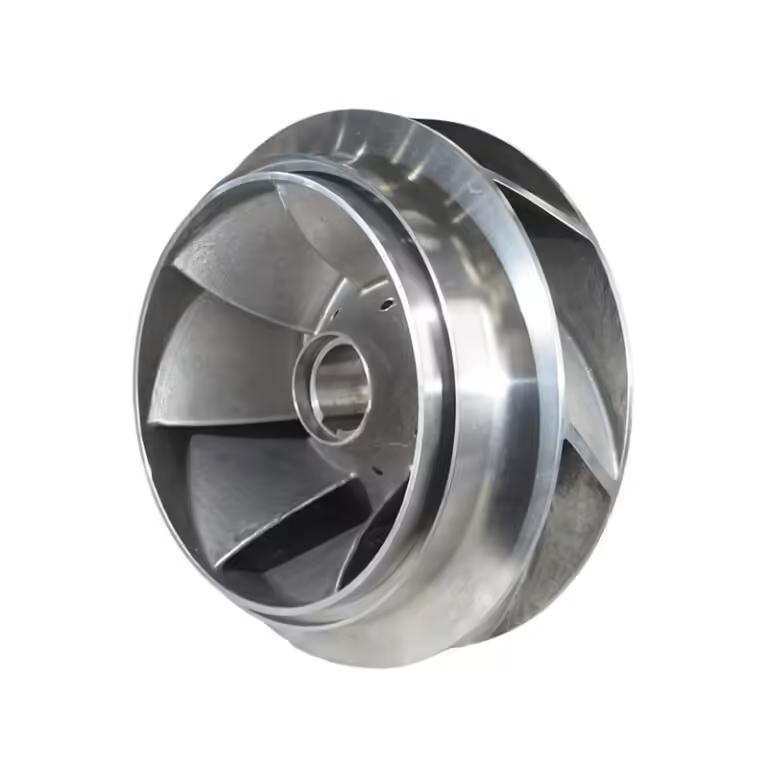
A buyer seeking impellers for a centrifugal pump received two quotes. One appeared 30% lower but lacked details—no mention of casting method, testing, or coating. The lead time was “estimated,” and the supplier did not clarify packaging.
The second quote included dynamic balancing, full certificates, firm delivery dates, and shipping with insurance. It even specified that the impellers were made via investment casting.
Though initially more expensive on paper, the second quote turned out to be faster and more reliable. The impellers arrived on time, performed as required, and passed third-party inspections. The first vendor never followed up after delays.
The lesson? A quote with more transparency is almost always the better deal in the long run.
Conclusión
Not all cast iron impeller quotes are created equal. While some vendors may offer enticing numbers, they may come with hidden costs, vague deliverables, or inadequate materials. By knowing what to ask and how to read between the lines, you can filter out misleading offers and find a trustworthy supplier who delivers the right component—on time, within scope, and to spec.
Focus on clarity, completeness, and comparison. In doing so, you’ll avoid unnecessary expenses, delays, and frustration—and ensure your pump systems continue to run smoothly with reliable impellers sourced under well-understood terms.
PREGUNTAS FRECUENTES
Q1: What standards should I expect for cast iron impellers?
You should request ASTM, ISO, or GB standards depending on your region. The material grade (e.g., ASTM A48, Class 30 or 40) and hardness levels are vital for compatibility.
Q2: Can I request a sample before placing a bulk order?
Yes. Most reliable suppliers allow for sample orders, especially when launching a new project. Use the sample to test dimensional fit, balance, and material integrity.
Q3: Should I worry about cavitation or erosion resistance?
Yes. Cast iron impellers are generally good for moderate-duty applications, but you should confirm if additional coatings or alloying are needed for highly erosive or cavitating environments.
Q4: Do I need balancing for small impellers?
Absolutely. Even small impellers rotating at high speeds can cause vibration if unbalanced. Always verify whether your quote includes dynamic or static balancing.
Q5: What is the best way to compare multiple quotes?
Use a checklist to verify if each quote includes the same scope—materials, processes, documentation, and delivery terms. Quotes should be evaluated side-by-side based on total value, not just unit price.
Categorías de productos
- Piezas de válvulas
- Piezas de la bomba de agua
- Piezas de la caja de cojinetes
- Piezas de fundición a presión
- Productos para bombas de acero inoxidable
- Productos para bombas de hierro fundido
- Piezas de válvulas para automóviles
- Recambios para automóviles
- Piezas de válvulas para uso civil
- Piezas de bomba de vacío KF
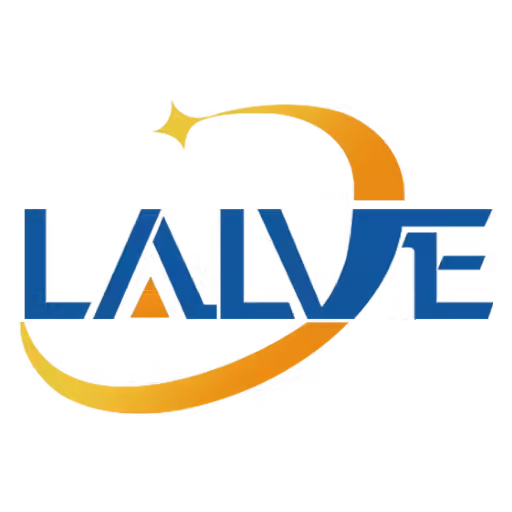