10 errores críticos en la fundición de bombas y válvulas
¡Bienvenido a mi blog!
¡Me encanta tenerte aquí! Antes de profundizar en el contenido, me encantaría que me acompañaras en mis redes sociales. Es donde comparto información adicional, conecto con nuestra increíble comunidad y te mantengo al tanto de las últimas noticias. Así es como puedes mantenerte conectado:
📘 Facebook: Shanghai Leierwo Industria Comercio Co., Ltd.
¡Ahora, emprendamos este viaje juntos! Espero que el contenido aquí te resulte no solo revelador, sino también inspirador y valioso. ¡Comencemos!
Tabla de contenido
Introducción
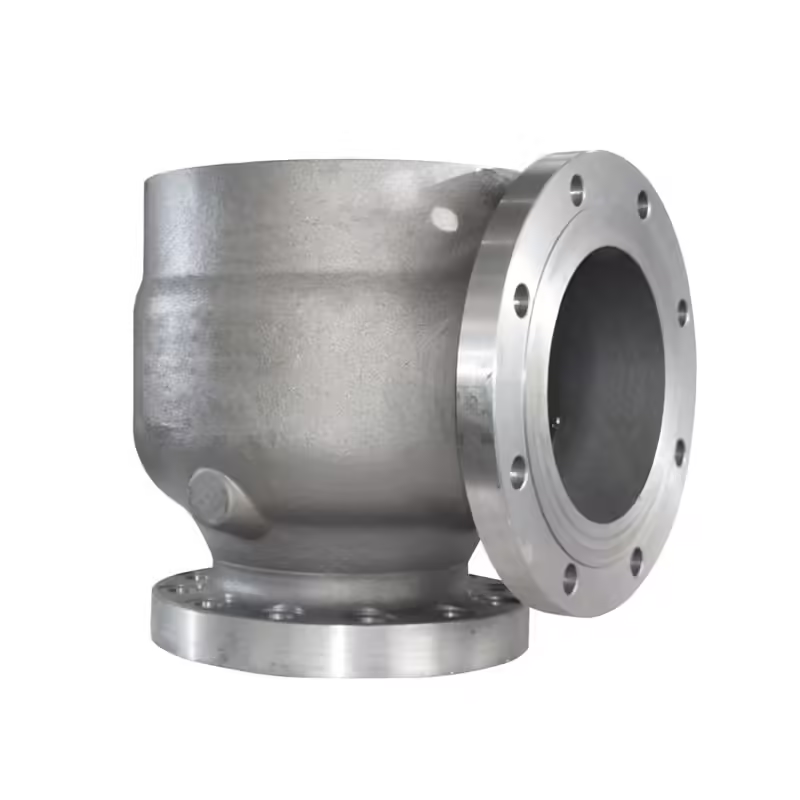
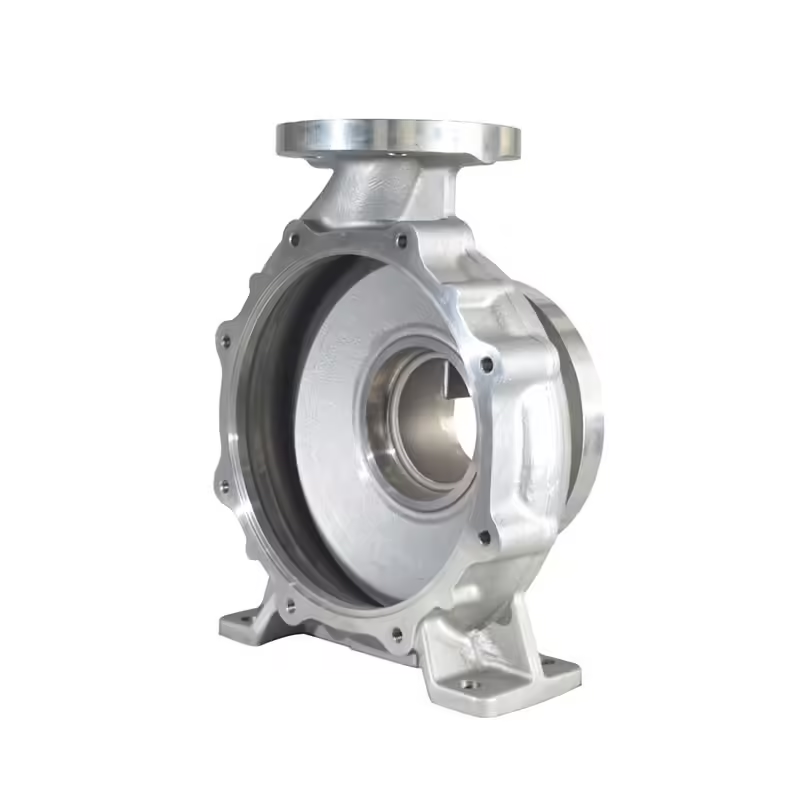
Pump and valve castings play a vital role in a wide range of industrial applications, from oil and gas to water treatment and chemical processing. They are designed to handle high pressures, corrosive substances, and extreme temperatures. However, despite their importance, there are numerous challenges and common mistakes manufacturers and buyers face when dealing with pump and valve castings. Understanding these mistakes can help avoid operational failures, safety risks, and financial losses.
In this blog, we will explore ten critical mistakes commonly seen in the world of pump and valve castings, analyze their consequences, and offer practical insights to help you make informed decisions. Whether you’re an engineer, procurement specialist, or business owner, this comprehensive guide is your roadmap to ensuring the reliability and performance of these essential components.
NO 1. Ignoring Material Compatibility in Pump and Valve Castings
One of the most critical and frequently overlooked mistakes in pump and valve castings is the selection of incompatible materials. Pump and valve castings operate in highly demanding environments where material properties must align precisely with the application’s requirements. Factors such as exposure to corrosive chemicals, high pressure, temperature extremes, and abrasive media demand careful material consideration.
Using the wrong material can lead to premature wear, corrosion, cracking, or even catastrophic failure. For instance, castings used in marine applications often require corrosion-resistant alloys such as duplex stainless steel or nickel-based alloys to withstand saltwater exposure. In contrast, castings used in the chemical processing industry might need super austenitic stainless steels or specialized alloys to resist aggressive acids and alkalis.
Failure to match material specifications not only shortens the lifespan of pump and valve castings but also increases maintenance frequency, downtime, and operational costs. In industries like oil and gas, chemical processing, or power generation, such failures can also pose significant safety risks. Therefore, understanding the operating environment and consulting material experts during the design and procurement phase is essential to avoid this costly mistake.
NO 2. Poor Design in Pump and Valve Castings
Design flaws are another common issue. Improperly designed pump and valve castings can cause turbulence, cavitation, and flow inefficiencies. Common design errors include insufficient wall thickness, poor geometry for fluid flow, and stress concentration points.
Effective casting design must take into account fluid dynamics, structural integrity, and ease of manufacturing. Collaborating with experienced engineers and foundries early in the process helps prevent these problems.
NO 3. Inadequate Quality Control Procedures
Even the best materials and designs can fail without strict quality control. Pump and valve castings require comprehensive testing protocols to ensure they meet rigorous industry standards and perform reliably in their intended applications. Quality control procedures encompass non-destructive testing (NDT), dimensional inspections, chemical composition verification, and mechanical property testing.
NDT techniques such as ultrasonic testing, radiography, magnetic particle inspection, and dye penetrant testing help identify surface and subsurface defects, including cracks, inclusions, or porosity. Dimensional inspections guarantee that castings conform to tight tolerances necessary for proper assembly and operation. Chemical analysis confirms that alloy compositions meet specifications critical for corrosion resistance and mechanical properties.
Companies that neglect or underinvest in these essential quality control steps risk producing pump and valve castings with hidden defects that may cause failure in service. Implementing a robust quality management system reduces scrap rates, lowers warranty claims, and improves customer satisfaction by delivering dependable products.
NO 4. Neglecting Heat Treatment of Pump and Valve Castings
Heat treatment plays a critical role in determining the mechanical properties of metal castings. Without proper heat treatment, castings can be brittle, weak, or unable to perform under stress. Heat treatment processes such as annealing, quenching, and tempering optimize hardness, strength, and ductility.
Failure to apply the right heat treatment or doing it improperly can significantly reduce the effectiveness of the final product. Proper heat treatment must be tailored to the casting material and intended application.
NO 5. Failing to Consider Machinability
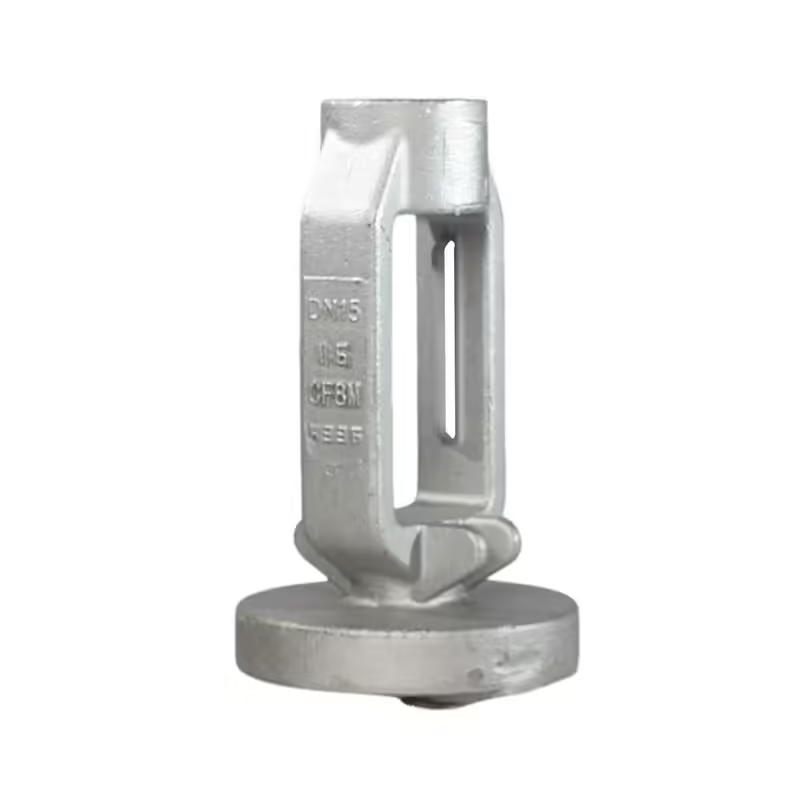
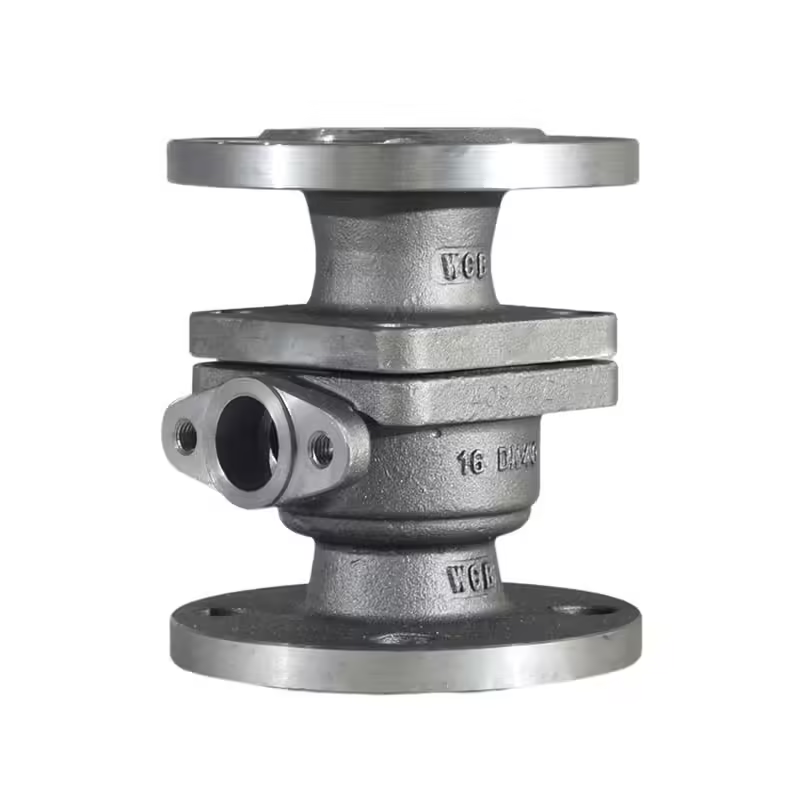
Machinability is often underestimated during the selection of pump and valve castings. Some materials or casting designs are difficult to machine, resulting in excessive tool wear, long machining times, and higher production costs. Poor machinability can delay project timelines and inflate budgets, affecting overall profitability.
When machinability is ignored, manufacturers may face challenges such as tool breakage, poor surface finish, dimensional inaccuracies, and increased labor costs. These issues are more common in castings made from hard alloys or those with complex shapes requiring extensive machining.
To avoid these problems, machinability should be evaluated early in the design and material selection process. Engineers should consider using materials with better machinability or simplifying casting geometry to minimize complex machining operations. Advanced machining techniques like CNC milling or EDM can also help but come at a cost. A balanced approach ensures pump and valve castings meet performance requirements without excessive manufacturing burdens.
Mid-Article Table: Common Pump and Valve Castings Mistakes and Their Impact
Mistake | Descripción | Potential Consequences |
---|---|---|
Wrong Material Selection | Using incompatible metals for the working environment | Corrosion, failure, safety risks |
Design Flaws | Inefficient fluid dynamics, poor geometry | Cavitation, flow inefficiencies, structural issues |
Lack of Quality Control | Inadequate testing and inspection | Surface defects, porosity, product failure |
Skipping Heat Treatment | Improper or no thermal processing | Weakness, brittleness, poor performance |
Overlooking Machinability | Choosing hard-to-machine materials | Cost overruns, production delays |
NO 6. Inconsistent Casting Processes
Variations in casting procedures from one batch to another can lead to inconsistent results. Temperature fluctuations, improper mold preparation, and varying cooling rates can all affect the final properties of the pump and valve castings.
Standardizing the casting process and maintaining strict process control is key. Reliable suppliers document their processes and provide consistent output that meets quality benchmarks.
NO 7. Relying on Unqualified Suppliers
A common pitfall in procuring pump and valve castings is prioritizing cost over quality by selecting unqualified or inexperienced suppliers. Castings require precise control of material properties, dimensional accuracy, and defect-free surfaces. Suppliers lacking expertise or modern equipment may fail to meet these exacting standards, resulting in costly rejections, delays, and operational failures.
Choosing suppliers solely based on the lowest bid often overlooks the critical factors of technical capability and quality assurance. Experienced foundries specializing in pump and valve castings understand the nuances of alloy selection, casting design, and finishing processes. They also maintain advanced testing facilities and employ skilled technicians to ensure product conformity.
Before partnering with any supplier, it is vital to conduct a thorough evaluation of their certifications such as ISO 9001 or API 6A, review their track record with similar projects, and verify their quality control procedures. Requesting references and sample reports of past work can provide valuable insights into their reliability.
Establishing long-term relationships with reputable suppliers not only guarantees superior castings but also facilitates collaboration on design improvements, troubleshooting, and innovation. The slight premium paid for qualified suppliers often results in overall cost savings through reduced scrap, rework, and downtime.
NO 8. Underestimating Lead Times
Pump and valve castings typically involve custom molds, complex geometries, and post-processing steps. Underestimating the time required for production can disrupt supply chains and delay projects.
Realistic scheduling that includes design, tooling, testing, and shipping is crucial for timely delivery. Buffer periods should be built into procurement plans to accommodate unexpected issues.
NO 9. Disregarding Testing Requirements
In critical applications, performance testing is non-negotiable. However, some companies skip or minimize testing to cut costs. This is especially risky in applications involving high pressure or hazardous materials.
Testing such as hydrostatic pressure testing, X-ray inspection, and mechanical property verification should be standard. These help ensure that the pump and valve castings function as intended under actual service conditions.
NO 10. Not Planning for Lifecycle Costs
Many organizations focus exclusively on the initial purchase price when acquiring pump and valve castings, neglecting the broader perspective of lifecycle costs. This narrow view can be misleading, as low-cost castings often incur higher expenses over their operational lifetime due to increased maintenance, frequent replacements, and unscheduled downtime.
Lifecycle costs encompass the total cost of ownership, including procurement, installation, operation, maintenance, and disposal or recycling. Pump and valve castings of inferior quality or inappropriate materials may require more frequent repairs, corrosion treatments, or replacements.
Investing in premium materials and precise casting methods typically results in components with superior durability, corrosion resistance, and mechanical strength. Though the upfront cost is higher, these castings extend service intervals and reduce maintenance labor and material costs.
Lifecycle cost analysis allows organizations to compare options based on total value rather than price alone. This strategic approach enhances operational reliability, reduces downtime risks, and improves return on investment (ROI).
Effective lifecycle management also includes planning for spare parts availability, maintenance scheduling, and end-of-life recycling or disposal in compliance with environmental regulations. Considering these factors in the procurement stage ensures sustainable and cost-effective pump and valve casting solutions.
Conclusión
Pump and valve castings are mission-critical components in many industrial systems. However, common mistakes—ranging from poor material choices to lack of quality control—can significantly undermine performance and reliability. By understanding these pitfalls and implementing best practices, you can greatly improve the efficiency, safety, and cost-effectiveness of your operations.
Avoiding the ten critical mistakes discussed in this article can help ensure that your pump and valve castings deliver maximum value and minimal risk. Always work with trusted suppliers, invest in proper testing, and consider the full lifecycle cost to make smarter procurement and design decisions.
PREGUNTAS FRECUENTES
What are Fundiciones de bombas y válvulas used for?
Pump and valve castings are used to create the structural and flow-control components in fluid systems across various industries, including oil and gas, water treatment, chemical processing, and power generation.
Why is material selection important in Fundiciones de bombas y válvulas?
The correct material ensures compatibility with the operational environment, preventing issues like corrosion, wear, or mechanical failure.
How can I ensure the quality of Fundiciones de bombas y válvulas?
Implementing strict quality control procedures such as non-destructive testing, dimensional checks, and material analysis is crucial to verifying casting quality.
What is the biggest mistake in sourcing castings?
Choosing suppliers based on cost alone is a major error. Experience, capabilities, and quality assurance should be top criteria when selecting a casting partner.
How can I reduce lifecycle costs for Fundiciones de bombas y válvulas?
Focus on total cost of ownership rather than just initial price. Select high-quality materials, invest in proper processing, and work with reliable suppliers to maximize long-term value.
Categorías de productos
- Piezas de válvulas
- Piezas de la bomba de agua
- Piezas de la caja de cojinetes
- Piezas de fundición a presión
- Productos para bombas de acero inoxidable
- Productos para bombas de hierro fundido
- Piezas de válvulas para automóviles
- Recambios para automóviles
- Piezas de válvulas para uso civil
- Piezas de bomba de vacío KF
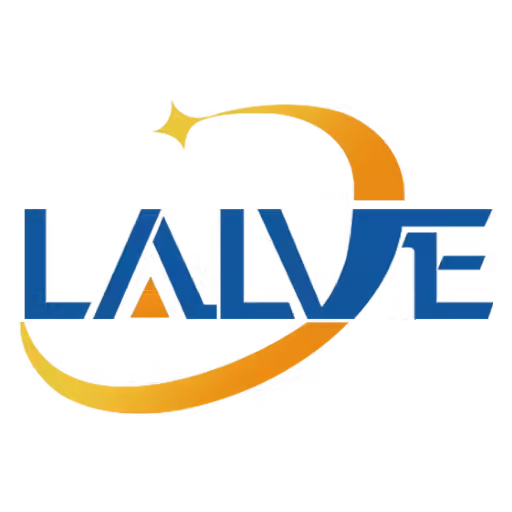