5 Common Gate Valve Body Castings Issues and Solutions
¡Bienvenido a mi blog!
¡Me encanta tenerte aquí! Antes de profundizar en el contenido, me encantaría que me acompañaras en mis redes sociales. Es donde comparto información adicional, conecto con nuestra increíble comunidad y te mantengo al tanto de las últimas noticias. Así es como puedes mantenerte conectado:
📘 Facebook: Shanghai Leierwo Industria Comercio Co., Ltd.
¡Ahora, emprendamos este viaje juntos! Espero que el contenido aquí te resulte no solo revelador, sino también inspirador y valioso. ¡Comencemos!
Tabla de contenido
Introducción
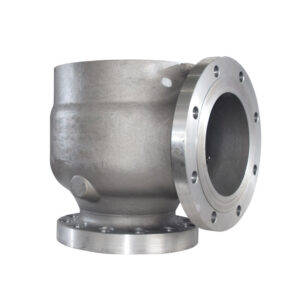
Gate valve body castings are essential components in various industries where controlling fluid and gas flow is crucial. These castings form the foundation of gate valves, which regulate the flow of liquids and gases in pipelines, tanks, and other industrial systems. While gate valves are designed to withstand tough operational conditions, problems with their body castings can significantly affect valve performance and reliability. These issues can result in costly repairs, safety hazards, and operational downtimes. In this blog post, we will address the five most common problems encountered with gate valve body castings and provide practical solutions to resolve these issues, helping to ensure the longevity and efficiency of the valves.
NO 1. Porosity in Gate Valve Body Castings
What is Porosity in Gate Valve Body Castings?
Porosity is one of the most prevalent defects found in gate valve body castings. It occurs when small pockets of air or gas become trapped inside the metal during the casting process. These trapped voids form pores within the metal, weakening the casting and reducing its structural integrity. Porosity can lead to several performance issues, including leaks, loss of pressure, and compromised sealing. When left undetected, it can cause more severe failures that may lead to valve malfunction.
Why Does Porosity Occur?
Porosity typically forms during the solidification of the molten metal when air or other gases become entrapped in the casting. The issue can be further exacerbated by factors such as improper molding, inadequate degassing of the metal, or excessive moisture in the mold material. Poor ventilation in the casting molds can also contribute to porosity.
Solution for Porosity in Gate Valve Body Castings
To prevent porosity, manufacturers must ensure that the mold materials are free from moisture and properly vented. Additionally, controlling the pouring temperature and utilizing degassing agents can help remove any trapped gases from the molten metal before it solidifies. Regular testing using non-destructive methods such as X-rays, ultrasonic testing, or dye penetration can help detect porosity and prevent defective gate valve body castings from reaching the production line.
NO 2. Cracking in Gate Valve Body Castings
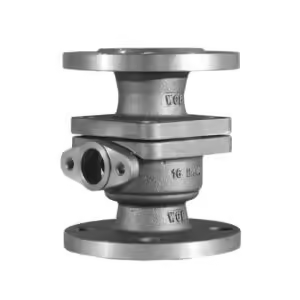
Why Do Cracks Form in Gate Valve Body Castings?
Cracking is another significant issue that affects gate valve body castings. Cracks can occur during cooling due to thermal stresses or improper cooling methods. When the casting cools too quickly, it can cause internal stresses that result in cracks or fractures in the metal. Cracks can also form when mechanical stresses or impacts exceed the material’s strength. These cracks can cause leakage, weaken the valve structure, and ultimately lead to valve failure if left unchecked.
Solution for Cracking in Gate Valve Body Castings
To reduce the risk of cracking, it is essential to use a controlled cooling process. This involves regulating the temperature of the molten metal and allowing the casting to cool slowly and uniformly. Additionally, using heat treatment techniques such as annealing can help relieve internal stresses that could lead to cracks. The use of high-quality alloy materials that are more resistant to cracking under stress is another solution to this problem. For castings that have already cracked, non-destructive testing methods can be used to assess the extent of the damage and determine whether repair or replacement is necessary.
NO 3. Inconsistent Wall Thickness in Gate Valve Body Castings
What is Inconsistent Wall Thickness?
Inconsistent wall thickness occurs when different areas of the gate valve body casting have varying levels of thickness. This can happen due to improper metal flow during the casting process or uneven cooling rates. When certain parts of the mold cool more rapidly than others, the metal contracts unevenly, creating areas with thin or weak walls. These thin areas are more susceptible to failure, especially under pressure, and can compromise the overall strength and durability of the gate valve.
Solution for Inconsistent Wall Thickness in Gate Valve Body Castings
To ensure consistent wall thickness, manufacturers must pay attention to the design and construction of the mold. The mold should be engineered to allow for an even distribution of molten metal. Optimizing the cooling process is also critical, as a slow and even cooling rate helps ensure that the casting solidifies uniformly. Additionally, employing simulation software during the design phase can help predict and address potential issues with wall thickness before the casting process begins. Regular inspections during and after the casting process can also help identify inconsistencies and prevent them from affecting the final product.
NO 4. Sand Inclusion in Gate Valve Body Castings
What is Sand Inclusion in Gate Valve Body Castings?
Sand inclusion is a common defect in gate valve body castings that occurs when sand particles from the mold material become trapped inside the casting. This can happen if the sand used in the mold is not properly prepared or if the mold is not cleaned thoroughly before casting. Sand inclusion can weaken the material and affect the surface finish of the gate valve body. In some cases, it can also affect the sealing ability of the valve, causing leaks and operational failures.
Solution for Sand Inclusion in Gate Valve Body Castings
To prevent sand inclusion, manufacturers must ensure that the mold is prepared using high-quality sand materials that are free of contaminants. The mold should be properly cleaned to remove any residual sand particles before the casting process begins. Additionally, optimizing the casting process, such as controlling the pouring speed and temperature, can reduce the likelihood of sand inclusion. Post-casting processes, such as sandblasting or shot peening, can also be used to remove any trapped sand particles from the surface of the gate valve body.
NO 5. Dimensional Inaccuracies in Gate Valve Body Castings
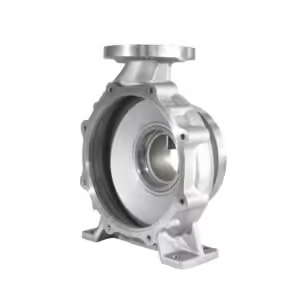
Why Do Dimensional Inaccuracies Occur?
Dimensional inaccuracies in gate valve body castings are often the result of flaws in the mold design, improper material flow, or poor casting techniques. These inaccuracies can lead to poor-fitting components, misalignment, and operational issues when the valve is assembled. Inaccurate dimensions can also result in sealing problems and cause the valve to fail under pressure. For gate valves to function correctly, precise dimensional tolerances must be maintained throughout the casting process.
Solution for Dimensional Inaccuracies in Gate Valve Body Castings
To minimize dimensional inaccuracies, manufacturers should use advanced measuring techniques such as 3D modeling and laser scanning to design precise molds. The casting process should be closely monitored to ensure that the molten metal is distributed evenly, and the mold is filled properly. Using high-quality materials and optimizing the cooling and solidification process can also help reduce dimensional issues. After the casting has solidified, dimensional inspection tools such as coordinate measuring machines (CMM) and micrometers can be used to check the accuracy of the final product.
Table: Common Gate Valve Body Casting Issues and Their Solutions
Issue | Cause | Solution |
---|---|---|
Porosity | Trapped air or gases during casting | Maintain proper casting techniques, use degassing agents, and inspect regularly |
Cracking | Thermal stresses, rapid cooling, mechanical impacts | Use controlled cooling processes and heat treatment, inspect for cracks |
Inconsistent Wall Thickness | Uneven cooling or mold design flaws | Use well-designed molds, optimize cooling systems, and check for consistency |
Sand Inclusion | Poor mold preparation or improper casting process | Ensure proper mold preparation, use high-quality materials, and clean molds |
Dimensional Inaccuracies | Mold defects, poor material distribution | Employ advanced measurement techniques, optimize mold design, and inspect regularly |
Conclusión
Gate valve body castings are fundamental components in various industrial applications. However, like any critical part, they are susceptible to several issues during the manufacturing process. By understanding the common problems, such as porosity, cracking, inconsistent wall thickness, sand inclusion, and dimensional inaccuracies, manufacturers can take the necessary steps to prevent these issues. Using advanced techniques, conducting regular inspections, and implementing optimal processes can help ensure that gate valve body castings are of the highest quality, providing reliable performance and extending the lifespan of gate valves.
PREGUNTAS FRECUENTES
What is the most common issue in gate valve body castings?
The most common issue is porosity, where air pockets become trapped inside the casting, weakening the material.
How can I detect cracks in gate valve body castings?
Non-destructive testing methods such as ultrasonic or X-ray testing are effective for detecting cracks without damaging the casting.
Can inconsistent wall thickness affect the performance of gate valves?
Yes, uneven wall thickness can lead to structural weaknesses and poor performance, especially under pressure.
How can sand inclusion be prevented in gate valve body castings?
Proper mold preparation, high-quality mold materials, and regular cleaning of molds help prevent sand inclusion.
Why is dimensional accuracy important for gate valve body castings?
Dimensional accuracy ensures that the gate valve components fit together correctly, preventing misalignment and ensuring proper sealing.
Categorías de productos
- Piezas de válvulas
- Piezas de la bomba de agua
- Piezas de la caja de cojinetes
- Piezas de fundición a presión
- Productos para bombas de acero inoxidable
- Productos para bombas de hierro fundido
- Piezas de válvulas para automóviles
- Recambios para automóviles
- Piezas de válvulas para uso civil
- Piezas de bomba de vacío KF
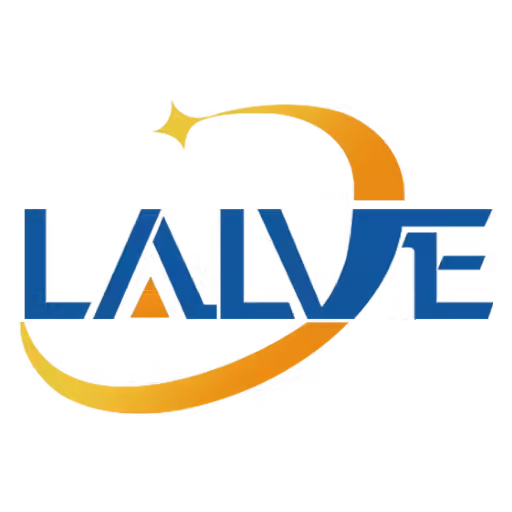