Why Custom Mechanical Parts Outperform Standard Ones
Welcome to My Blog!
I’m thrilled to have you here! Before we dive into the content, I’d love for you to join me on my social media platforms. It’s where I share extra insights, connect with our amazing community, and keep you updated on the latest news. Here’s how you can stay connected:
📘 Facebook: Shanghai Leierwo Industry Trade Co., Ltd.
Now, let’s embark on this journey together! I hope you find the content here not only insightful but also inspiring and valuable. Let’s get started!
Table of Contents
Introduction
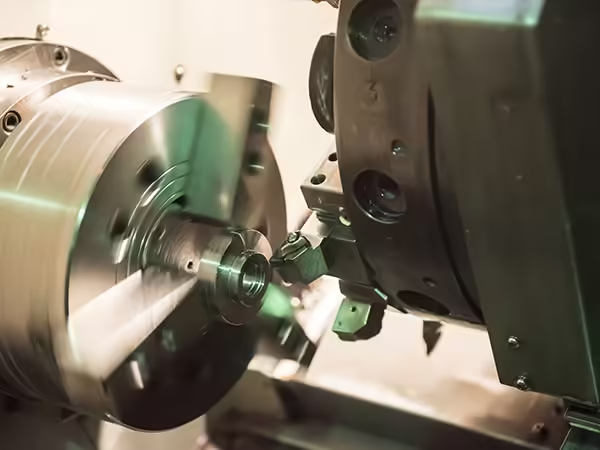
In today’s advanced manufacturing landscape, companies across sectors are shifting from standardized solutions to tailored alternatives. One major aspect of this evolution is the growing preference for custom mechanical parts over traditional off-the-shelf components. As machinery becomes more complex and market competition tightens, manufacturers are seeking components that offer not just basic functionality but also enhanced performance, durability, and compatibility.
Custom mechanical parts are engineered specifically for a given application. They take into account the unique mechanical, environmental, and operational demands of the machinery or system they will be integrated into. Unlike standard parts, which are designed to meet generic specifications, custom mechanical parts are optimized to provide superior alignment with project requirements.
This article explores the core advantages of custom mechanical parts, their role in improving system performance, and why many industries are transitioning toward customized engineering solutions.
Tailored Fit and Function: The Engineering Precision of Custom Mechanical Parts
One of the most defining advantages of custom mechanical parts is their ability to meet exact design specifications. Standard components may require additional adjustments or even compromise in performance due to size mismatches, tolerance issues, or limited material options. In contrast, custom components are manufactured to fit perfectly within an existing or newly designed assembly.
This precise fit enhances the mechanical performance of the entire system. It ensures that forces are distributed appropriately, moving parts operate smoothly, and wear and tear are minimized. Custom mechanical parts are often used in high-precision environments such as aerospace, medical devices, robotics, and automation systems.
Benefits of Tailored Engineering:
- Optimal size and geometry for specific applications
- Elimination of mechanical slack or misalignment
- Improved structural integrity and longevity
- Compatibility with proprietary systems or modules
Material Flexibility: Selecting the Right Composition for Your Application
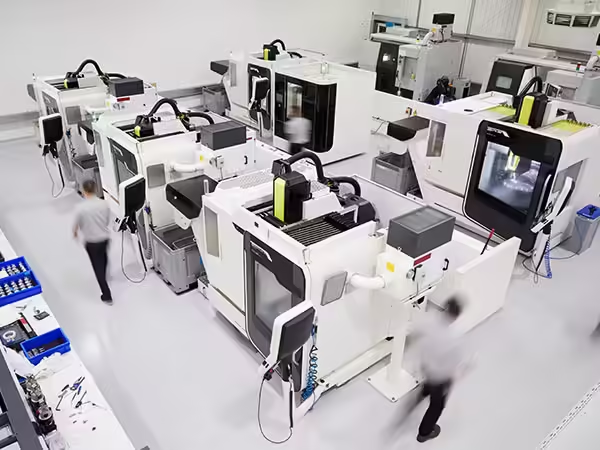
Material selection plays a crucial role in determining the performance of mechanical parts. Standard components are typically made from general-purpose materials such as mild steel, aluminum, or plastic. These materials may not offer the properties required for specific environmental or operational conditions.
Custom mechanical parts allow engineers to choose from a wide range of materials including stainless steel, titanium, composites, and specialty alloys. This flexibility enables optimization for parameters such as thermal resistance, chemical stability, load-bearing capacity, and weight.
Comparison Table: Custom vs. Standard Mechanical Parts
Feature | Custom Mechanical Parts | Standard Parts |
---|---|---|
Design Compatibility | Fully optimized | May require compromise |
Material Options | Wide and customizable | Limited and generic |
Lead Time | Longer, with prototyping phase | Shorter, off-the-shelf |
Performance in Harsh Conditions | Superior with custom material | May degrade quickly |
Integration into Systems | Seamless and precise | May need additional adaptation |
Cost Efficiency (Long-Term) | High ROI over time | Lower upfront cost, higher wear |
Performance Optimization: Enhanced Efficiency and Reliability
Custom mechanical parts can dramatically improve the efficiency and reliability of machinery. Unlike off-the-shelf standard parts, which must be adapted to fit into existing designs, custom components are engineered specifically to fulfill a targeted function within a given system. This ensures maximum compatibility, performance, and operational smoothness.
When every component is designed with a specific function in mind, the result is smoother mechanical operations, less vibration, and fewer points of failure. By addressing potential weak spots during the design phase—such as stress concentrations, misalignments, or inefficient geometries—engineers can eliminate bottlenecks and significantly improve system throughput and energy efficiency.
For example, a custom gear designed for a high-speed application can include optimized tooth profiles, advanced heat-treated materials, and precision surface treatments to reduce friction, heat generation, and operating noise. This leads to several advantages, including:
- Longer maintenance intervals due to lower wear and tear
- Reduced need for lubrication
- Enhanced load distribution and shock absorption
- Decreased vibration and acoustic emissions
These enhancements translate directly into lower total cost of ownership, improved productivity, and fewer unplanned shutdowns.
In addition to performance gains, custom mechanical parts often incorporate features that facilitate easier assembly, disassembly, or alignment. Examples include integrated mounting points, quick-release mechanisms, or directional guides. This is particularly important in systems that require regular maintenance or part replacement, such as in aerospace, manufacturing robotics, or medical equipment.
Furthermore, because each part is purpose-built, tolerances can be finely controlled. This allows designers to eliminate gaps, reduce backlash, and achieve tighter seals—benefits that are often difficult or impossible to realize with generic components.
Innovation and Competitive Advantage Through Custom Mechanical Parts
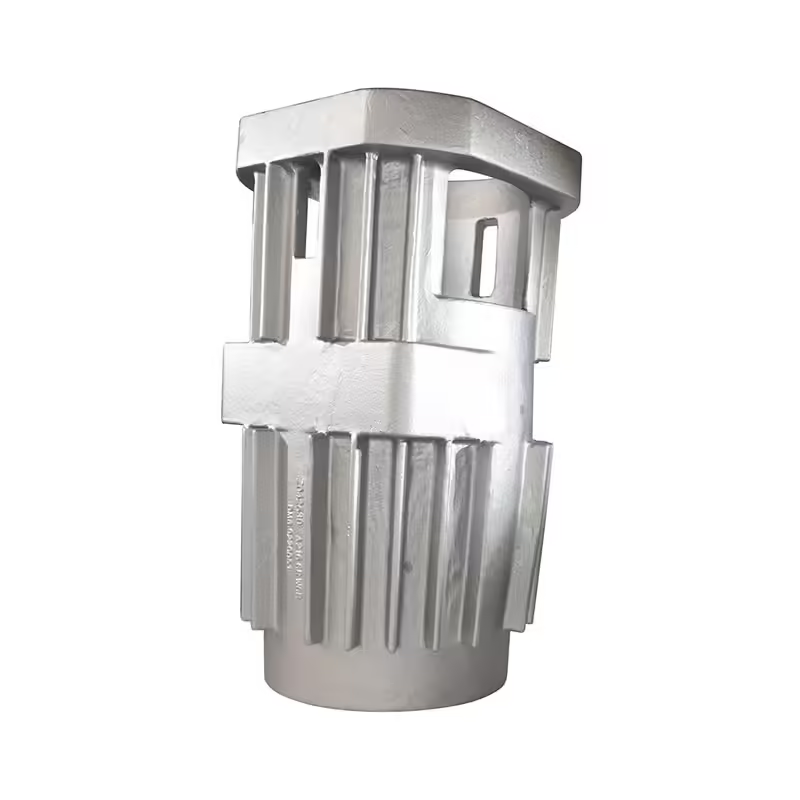
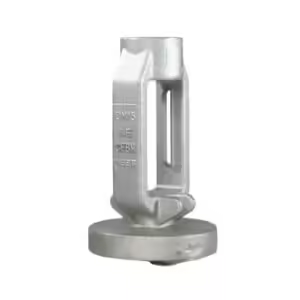
In industries where innovation is the primary driver of market differentiation, the ability to quickly develop and implement unique engineering solutions can be a major competitive advantage. Custom mechanical parts play a critical role in achieving this agility by unlocking new opportunities in design flexibility and product optimization.
Companies that rely solely on standard components are often limited by dimensional constraints, material limitations, or outdated design architectures. In contrast, engineers using custom mechanical parts can:
- Prototype new mechanisms faster
- Integrate emerging technologies without reworking entire systems
- Optimize older equipment for better performance or compliance
- Respond more effectively to customer-specific requirements
For instance, in the electric vehicle (EV) industry, the ability to customize mechanical components such as motor housings, transmission gears, or cooling systems can result in dramatic gains. Manufacturers can minimize component size to save space, reduce structural weight for better fuel economy, and fine-tune system dynamics for improved range and safety.
Similarly, renewable energy applications, such as wind turbines and solar tracking systems, demand precision movement, corrosion resistance, and long-term reliability—requirements that standard parts often cannot meet. Custom mechanical parts address these challenges directly with specialized coatings, geometries, and modular integration.
Modern technologies like CNC machining, laser cutting, and additive manufacturing (3D printing) have lowered the barriers to producing high-quality custom parts. Small and medium-sized enterprises now have the tools to manufacture low-volume batches at a reasonable cost, enabling rapid design iteration and fast market feedback cycles.
This has profound implications for time-to-market. Companies no longer need to wait weeks or months for tooling and standard part sourcing. Instead, they can turn digital designs into physical components within days, enabling a continuous loop of innovation and refinement.
Ultimately, embracing custom mechanical parts isn’t just about improving machines—it’s about future-proofing your product line and staying ahead in an increasingly competitive global market.
Conclusion
While the initial cost of custom mechanical parts may be higher than standard alternatives, the long-term benefits make them a strategic investment. From increased equipment reliability and performance to enhanced adaptability and innovation potential, the advantages are substantial.
Companies that integrate custom mechanical parts into their products and production lines often see improvements in customer satisfaction, product lifecycle, and operational efficiency. As customization technologies evolve and become more affordable, the trend toward tailor-made components is likely to accelerate.
In the era of Industry 4.0, where data-driven design and automation are reshaping manufacturing, custom mechanical parts represent a crucial tool for achieving precision, differentiation, and sustainability.
FAQ
What are custom mechanical parts?
Custom mechanical parts are components specifically designed and manufactured to meet the unique requirements of a particular machine, device, or system. Unlike off-the-shelf standard parts that are mass-produced with generic dimensions and capabilities, custom mechanical parts are tailored to perform specific functions under specific conditions. This might include unusual shapes, precise tolerances, custom materials, or integration features that cannot be achieved with standard components.
These parts are often created through advanced techniques like computer-aided design (CAD), CNC machining, laser cutting, and 3D printing. Common examples include customized gears, brackets, shafts, couplings, housings, seals, and precision assemblies. Custom mechanical parts are critical in applications where performance, efficiency, and reliability cannot be compromised.
Are custom mechanical parts more expensive?
Generally, yes—custom mechanical parts involve higher initial costs compared to standard parts. These costs stem from several factors, including engineering design, material selection, tooling or fixture creation, and prototyping. However, it’s important to view this cost in the context of the part’s lifecycle.
Custom parts are purpose-built, which often translates into better fit, fewer failures, improved performance, and extended service life. This significantly reduces maintenance frequency, unplanned downtime, and part replacement costs over time. In many industrial applications, the total cost of ownership (TCO) is lower when using custom mechanical parts, despite the higher upfront investment.
Furthermore, digital manufacturing advancements have brought down the cost of producing low- to medium-volume custom parts, making them more economically viable than ever before.
How long does it take to produce custom mechanical parts?
The production timeline for custom mechanical parts depends on several factors, such as:
- Part complexity (geometry, tolerances, features)
- Material availability and machinability
- Quantity required (prototyping vs. batch production)
- Manufacturing method (CNC, 3D printing, injection molding, etc.)
- Design and approval processes
For a simple custom part, the design and manufacturing process may take only a few days to a week. More complex assemblies may require several weeks, especially if multiple prototypes are needed for testing and revision.
However, with the help of rapid prototyping methods—such as 3D printing or quick-turn CNC services—many manufacturers can significantly shorten the lead time. Iterative development becomes faster, which is especially beneficial for startups, R&D departments, and time-sensitive production lines.
What industries benefit most from using custom mechanical parts?
Custom mechanical parts are used across a wide array of industries, particularly in sectors where precision, reliability, or innovative design is essential. Some of the key industries include:
- Aerospace: Custom brackets, housings, fasteners, and actuators designed for weight savings and high-stress conditions.
- Automotive: Bespoke drivetrain components, cooling system fittings, and suspension parts for performance optimization.
- Medical Devices: Precision-engineered implants, surgical tools, and diagnostic equipment requiring biocompatibility and sterility.
- Robotics and Automation: Custom linkages, motion systems, and frames built to exact operational specifications.
- Renewable Energy: Specialized components in wind turbines, solar tracking systems, and hydroelectric generators requiring corrosion resistance and long-term durability.
- Defense and Military: High-strength, lightweight parts built to withstand extreme environments and operational demands.
In all these fields, standard parts rarely offer the perfect solution. Custom mechanical parts provide the exact specifications and functionality needed for safety, innovation, and optimal performance.
Can small businesses afford custom mechanical parts?
Yes, increasingly so. Thanks to digital fabrication technologies like 3D printing, waterjet cutting, and affordable CNC machining, the barrier to entry for producing custom mechanical parts has significantly lowered. Even small businesses or individual inventors can now develop high-quality prototypes and short production runs without relying on large-scale manufacturers.
In fact, small businesses often benefit the most from custom mechanical parts because they allow unique product development, branding, and performance advantages that standard parts can’t deliver. By leveraging cloud-based CAD platforms, online manufacturing services, and flexible supply chains, startups and small manufacturers can bring custom innovations to market faster and more affordably than ever before.
Moreover, many manufacturing providers now offer design assistance, prototyping packages, and no-minimum-order services tailored specifically to the needs of small enterprises.
Product Categories
- Valve Parts
- Water Pump Parts
- Bearing Box Parts
- Die Casting Parts
- Stainless Steel Pump Products
- Cast Iron Pump Products
- Valve Parts For Automobile Use
- Auto Parts
- Valve Parts For Civil Use
- Vacuum Pump Parts KF
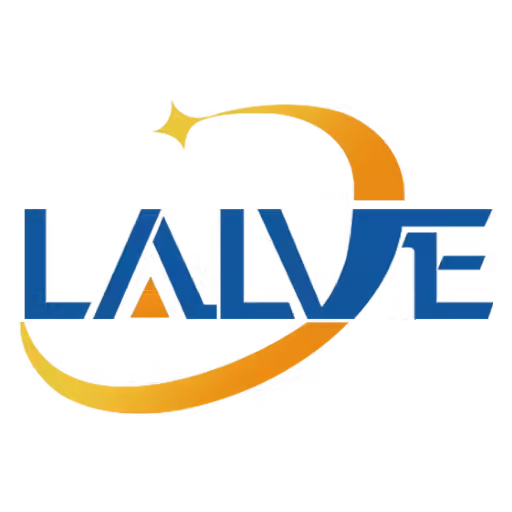