Top 8 Essential Pump Impeller Casting Tips
Welcome to My Blog!
I’m thrilled to have you here! Before we dive into the content, I’d love for you to join me on my social media platforms. It’s where I share extra insights, connect with our amazing community, and keep you updated on the latest news. Here’s how you can stay connected:
📘 Facebook: Shanghai Leierwo Industry Trade Co., Ltd.
Now, let’s embark on this journey together! I hope you find the content here not only insightful but also inspiring and valuable. Let’s get started!
Table of Contents
Introduction
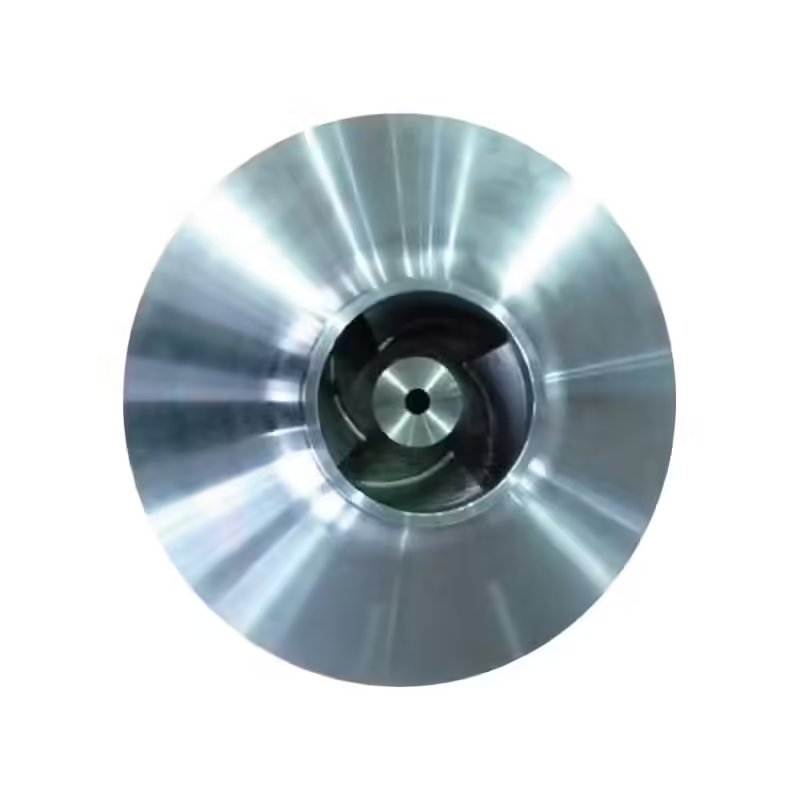
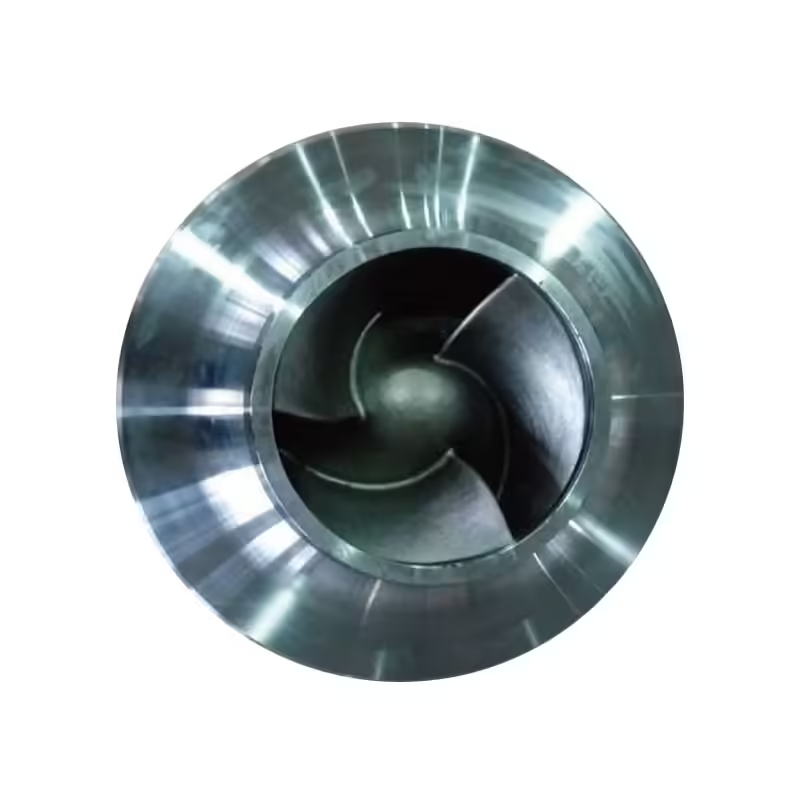
Pump impeller casting is a fundamental process in the manufacturing of efficient and reliable pumps used across various industries such as water treatment, chemical processing, oil and gas, and mining. The quality and precision of the pump impeller casting directly affect the pump’s hydraulic performance, wear resistance, and energy efficiency. Understanding the nuances of pump impeller casting can help manufacturers and engineers optimize production, minimize defects, and extend equipment life.
This article provides a comprehensive overview of eight essential tips that can enhance the quality and reliability of pump impeller casting. Whether you are a foundry operator, pump designer, or quality engineer, these insights will guide your decision-making and help avoid common pitfalls in pump impeller casting projects.
Tip 1: Select the Right for Your Application
Several casting techniques are available, and selecting the most appropriate one is crucial for achieving optimal impeller performance. The choice influences everything from dimensional accuracy to surface quality and production cost.
Common Casting Methods:
- Sand Casting: This method is highly adaptable and cost-effective, making it ideal for producing large components in low volumes. It’s well-suited for simpler designs where ultra-fine detailing isn’t a priority.
- Investment Casting: Known for its ability to produce intricate geometries with excellent surface finishes, this technique is ideal for applications requiring high precision and tight tolerances.
- Die Casting: If you’re looking to manufacture high volumes of smaller, detail-rich impellers, this method offers superior dimensional consistency and quick production cycles.
Your final decision should take into account variables like the complexity of the part, material type, dimensional requirements, and production scale. Each process offers a different balance of accuracy, finish, cost, and feasibility, all of which must align with your operational goals.
Tip 2: Optimize Impeller Design for Casting Feasibility
The design of the impeller plays a crucial role in casting quality. Complex designs can result in casting defects like shrinkage, porosity, or incomplete filling. Simplifying design features and ensuring uniform wall thickness can reduce these risks and enhance the pump impeller casting outcome.
Incorporate draft angles and generous radii to facilitate mold removal and minimize stress concentrations. Collaborate with design engineers to validate the manufacturability of the pump impeller casting design before tooling begins. Use simulation software to predict and prevent potential pump impeller casting issues.
Tip 3: Choose High-Quality Materials for Better Performance
The longevity and reliability of an impeller depend largely on the material from which it is made. Different working environments—whether corrosive, abrasive, or high-temperature—demand different material characteristics.
Common Material Choices:
- Stainless Steel: Offers excellent resistance to corrosion and is widely used in chemical or marine settings.
- Bronze: Known for good wear resistance and favorable casting properties; often used in seawater applications.
- Cast Iron: A more economical option for applications where high corrosion resistance isn’t required.
- Duplex Alloys: These materials provide a combination of strength and corrosion resistance, ideal for aggressive environments.
When selecting a material, consider key properties such as tensile strength, hardness, and thermal conductivity. It’s also important to ensure the alloy meets the chemical and mechanical standards required for your specific application.
Tip 4: Control Process Parameters to Minimize Defects
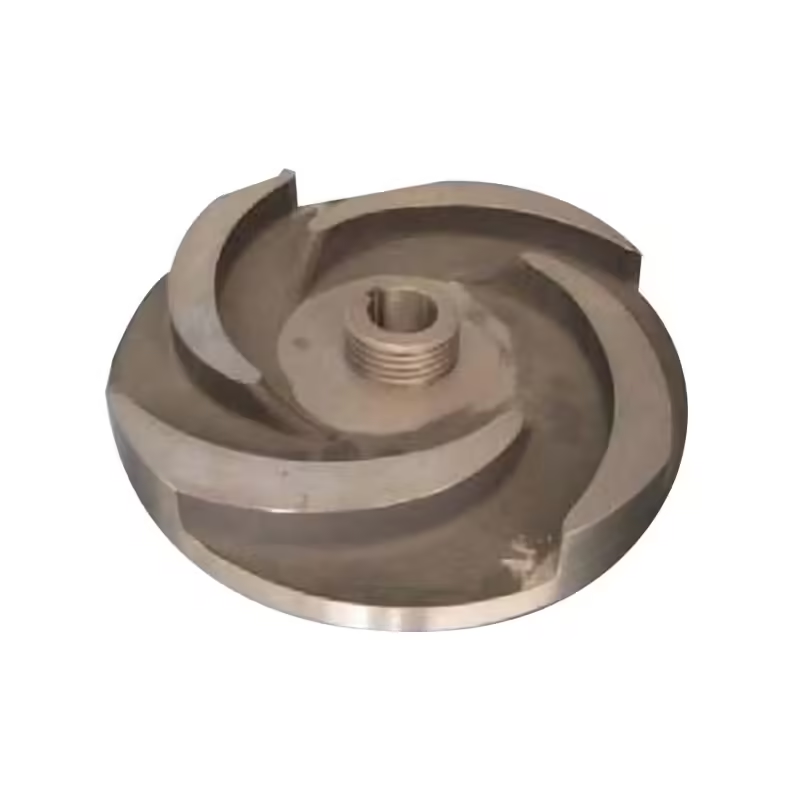
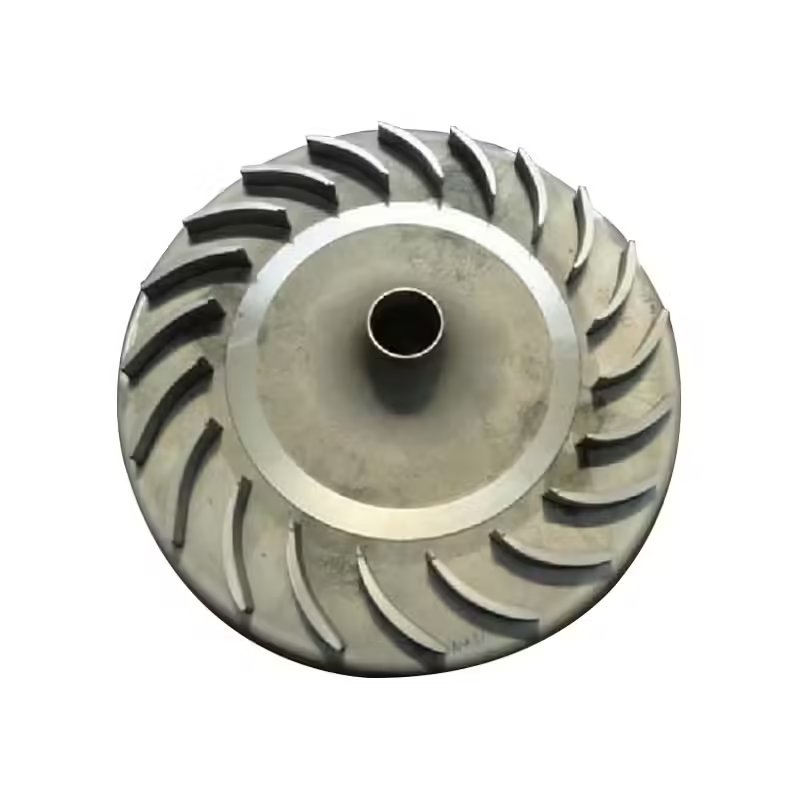
Achieving defect-free results requires tight control over key production parameters. Variations in pouring temperature, mold preheat levels, and cooling rates can lead to imperfections such as hot tears, internal voids, or dimensional inaccuracies.
Recommendations:
- Establish SOPs: Standard Operating Procedures help ensure consistent practices across batches.
- Monitor in Real-Time: Use sensors and automation to track vital metrics throughout the melt and pour process.
- Design Effective Gating Systems: Proper runner and riser placement ensures full mold filling and prevents air entrapment.
A controlled process doesn’t just yield better physical integrity—it also improves efficiency and reduces the likelihood of costly rework or scrap.
Tip 5: Implement Advanced Inspection Techniques
Quality control is indispensable in pump impeller casting. Non-destructive testing (NDT) methods such as X-ray inspection, ultrasonic testing, and dye penetrant testing can identify internal and surface defects without damaging the part.
Use dimensional inspection tools like coordinate measuring machines (CMM) to verify critical dimensions. Regular audits and inspections tailored to pump impeller casting help maintain consistent quality across batches.
Table: Comparison of Common Materials Used in Pump Impeller Casting
Material | Corrosion Resistance | Tensile Strength (MPa) | Temperature Tolerance | Typical Applications |
---|---|---|---|---|
Stainless Steel | Excellent | 500 – 750 | High | Chemical, marine, water pumps |
Bronze | Good | 200 – 500 | Medium | Marine, fire-fighting pumps |
Cast Iron | Moderate | 150 – 300 | Medium | HVAC, irrigation, general use |
Duplex Alloys | Excellent | 600 – 900 | High | Oil & gas, corrosive environments |
Tip 6: Focus on Energy Efficiency in Casting Design
Energy efficiency has become a top priority for industries relying on pumping systems, not only to reduce operational costs but also to meet sustainability goals. In the context of pump impeller casting, designing for energy efficiency begins at the earliest stages—long before the molten metal touches the mold.
One of the most effective strategies is optimizing the impeller’s hydraulic design. Factors such as blade number, blade curvature, vane angle, and channel width directly influence the flow characteristics and pressure head of the pump. A poorly designed impeller can create turbulence, flow separation, and recirculation zones, all of which reduce pump efficiency and increase energy consumption.
To mitigate these issues, engineers frequently employ computational fluid dynamics (CFD) simulations. CFD allows the evaluation of fluid behavior across different impeller designs, providing insights into how geometry affects efficiency. This enables design optimization before the pump impeller casting process even begins.
An energy-efficient impeller design will result in a casting that delivers smoother fluid motion, lower frictional losses, and improved mechanical stability. Over time, these benefits lead to measurable reductions in electricity usage and maintenance requirements. In systems that operate continuously, such as in wastewater treatment or industrial cooling circuits, the energy savings derived from an optimized pump impeller casting can be substantial.
Furthermore, integrating energy-efficient principles into casting design supports green manufacturing initiatives and aligns with growing regulatory pressure to reduce environmental impact.
Tip 7: Consider Post-Casting Machining and Finishing
After the casting is completed, secondary operations like machining, grinding, and surface finishing are crucial to meet dimensional and performance specifications. Impellers may require balancing to eliminate vibrations during operation.
Use CNC machines for precise machining, and apply coatings or treatments to enhance wear resistance and surface quality. The quality of the final product often depends on the effectiveness of post-casting processes.
Tip 8: Ensure Compliance with Industry Standards
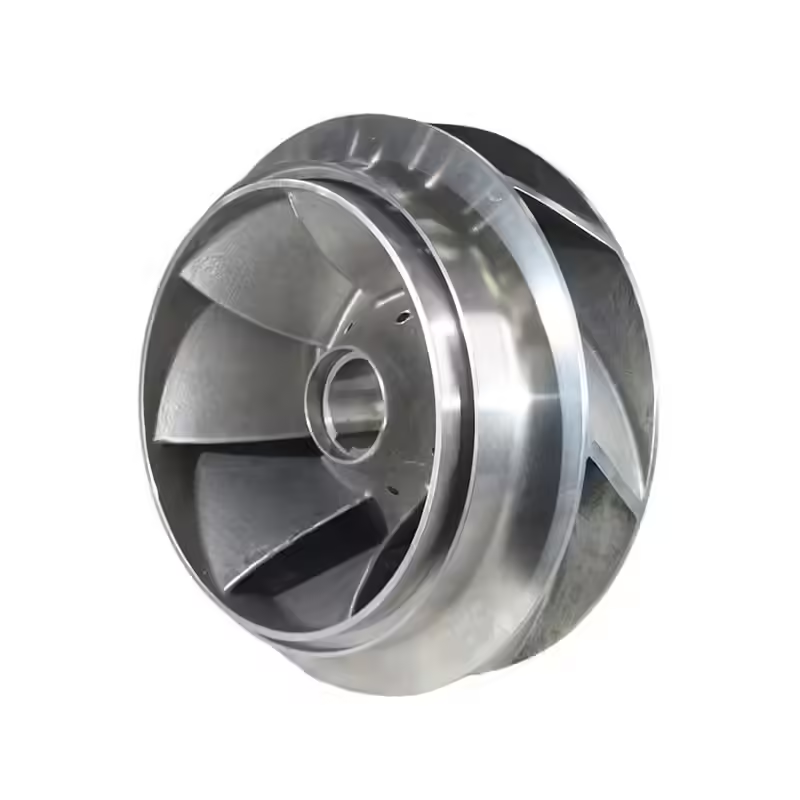
Adhering to international and industry-specific standards ensures reliability and customer confidence. Standards such as ASTM, ASME, and ISO define material grades, testing procedures, and dimensional tolerances.
Compliance not only facilitates market acceptance but also reduces the risk of product failures. Implement a robust documentation system to track compliance from raw material procurement to final inspection.
Conclusion
Pump impeller casting is more than just a manufacturing process—it is a critical step that determines the efficiency, reliability, and lifespan of the pump. By following these eight essential tips, manufacturers can produce higher-quality castings, reduce operational costs, and improve customer satisfaction.
From selecting the right casting method to enforcing stringent quality checks, every stage plays a pivotal role in the final outcome. Staying informed and integrating modern technologies into traditional casting practices is key to maintaining competitiveness and excellence in the field.
FAQ
What is pump impeller casting?
Pump impeller casting is the manufacturing process where molten metal is poured into a mold to form the shape of a pump impeller. This method is widely used in industries like water treatment, chemical processing, and mining due to its ability to create complex geometries with precise dimensions. The quality of pump impeller casting significantly influences pump efficiency, reliability, and durability.
Why is the quality of pump impeller casting so important?
The performance of a pump largely depends on the accuracy and integrity of its impeller. Poor pump impeller casting can result in defects like porosity, misalignment, or imbalance, which may lead to reduced hydraulic efficiency, increased energy consumption, and even premature failure. Ensuring high-quality casting is critical to the longevity and effectiveness of the entire pump system.
How does pump impeller casting influence energy efficiency?
An efficiently cast impeller with optimized geometry reduces hydraulic losses and improves flow performance. Using tools like CFD (Computational Fluid Dynamics) during design helps fine-tune blade angles and streamline contours. Energy-efficient pump impeller casting contributes to lower operating costs and sustainable performance.
8. How can I ensure my pump impeller casting meets international standards?
Adherence to standards such as ASTM, ASME, and ISO ensures consistency in materials, tolerances, and testing methods. Following these guidelines builds trust with customers and allows for greater market accessibility. It’s also advisable to implement a comprehensive documentation and traceability system for every stage of the pump impeller casting process.
Product Categories
- Valve Parts
- Water Pump Parts
- Bearing Box Parts
- Die Casting Parts
- Stainless Steel Pump Products
- Cast Iron Pump Products
- Valve Parts For Automobile Use
- Auto Parts
- Valve Parts For Civil Use
- Vacuum Pump Parts KF
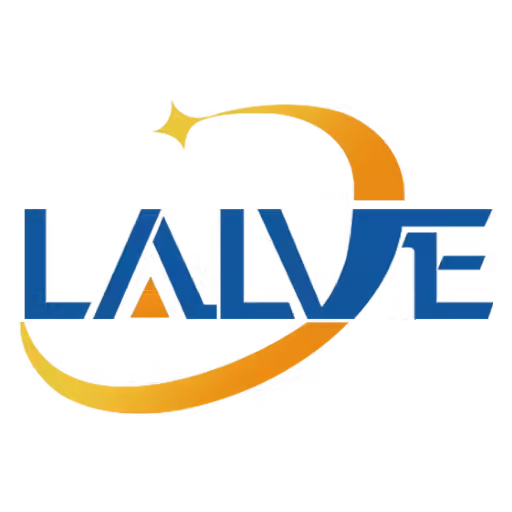