Precision Mechanical Parts:5 Must-Know Tips
Selamat Datang ke Blog Saya!
Saya teruja untuk mempunyai anda di sini! Sebelum kita menyelami kandungan, saya ingin anda menyertai saya di platform media sosial saya. Di situlah saya berkongsi cerapan tambahan, berhubung dengan komuniti kami yang hebat dan memaklumkan anda tentang berita terkini. Begini cara anda boleh terus berhubung:
📘 Facebook: Shanghai Leierwo Industry Trade Co., Ltd.
Sekarang, mari kita mulakan perjalanan ini bersama-sama! Saya harap anda mendapati kandungan di sini bukan sahaja bernas tetapi juga memberi inspirasi dan berharga. Mari mulakan!
Jadual Kandungan
pengenalan
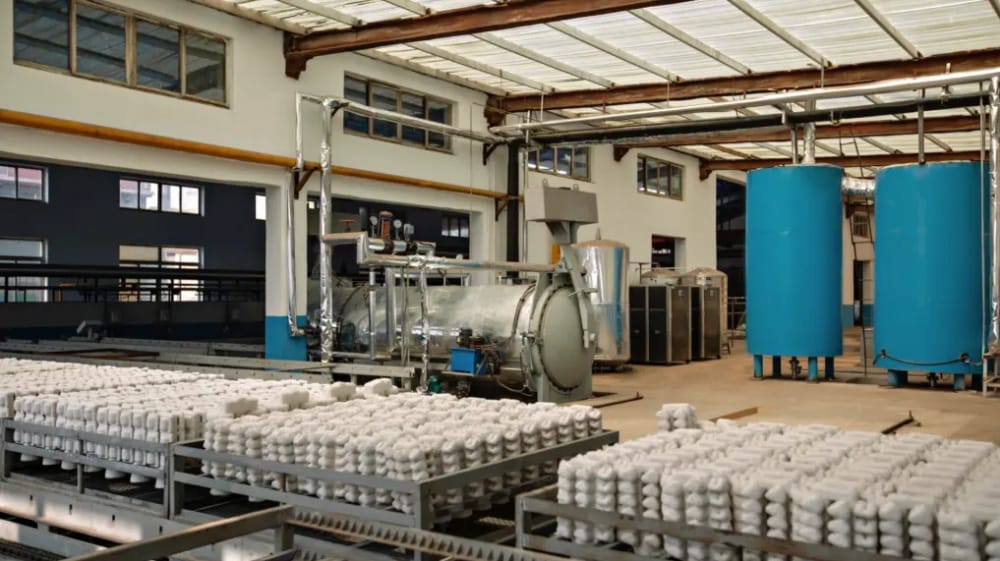
Precision mechanical parts are essential components in various industries, including aerospace, automotive, electronics, medical devices, and robotics. These parts are engineered with tight tolerances and high-quality materials to ensure accurate performance and consistent reliability. Without precision mechanical parts, many advanced systems would simply not function as expected.
In today’s globalized manufacturing environment, attention to detail and consistent quality in mechanical components are not just advantages—they’re necessities. This article explores five must-know tips that can help businesses, engineers, and procurement teams ensure optimal performance and longevity of their precision mechanical parts.
Whether you’re sourcing components for a new machine or troubleshooting an existing system, understanding the fundamentals of these parts can help reduce errors, improve efficiency, and lower maintenance costs.
Tip 1: Select the Right Material for Precision Mechanical Parts
The first and arguably most crucial aspect of working with precision mechanical parts is choosing the correct material. The material impacts performance, wear resistance, thermal stability, and machinability.
Common Materials Used in Precision Mechanical Parts
- Stainless steel
- aluminium
- Brass
- Titanium
- Engineering plastics (e.g., PEEK, Delrin)
Each material has unique properties that make it suitable for specific applications. For example, stainless steel offers excellent corrosion resistance and strength, making it ideal for medical or marine environments. On the other hand, aluminum is lightweight and cost-effective, perfect for aerospace and electronics.
When selecting materials, consider the following:
- Load requirements
- Environmental conditions (humidity, temperature, exposure to chemicals)
- Expected wear and tear
- Required precision and tolerance
Consult with materials engineers or your supplier to ensure you are not just choosing a material that “works” but one that performs optimally over time.
Tip 2: Tolerances and Accuracy Matter More Than You Think
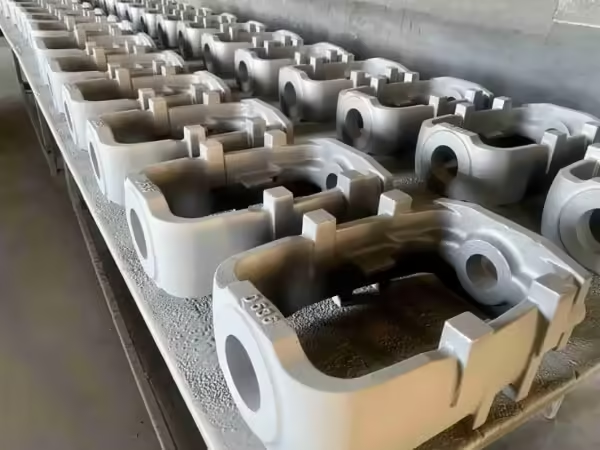
Precision mechanical parts are defined by their ability to fit within strict tolerance ranges. A part with a tolerance deviation as small as a few microns can lead to assembly errors, performance issues, or even system failures.
Understanding Tolerances in Precision Mechanical Parts
Tolerances refer to the allowable variation in a part’s dimensions. There are two key concepts:
- Dimensional tolerance: Acceptable variation in length, diameter, or thickness
- Geometric tolerance: Acceptable variation in shape, orientation, or position
Maintaining tight tolerances ensures that parts will fit and function as intended without requiring additional adjustments during assembly.
Precision is particularly important in high-speed or high-load systems where minor misalignments can lead to vibration, inefficiency, or premature wear.
Tip 3: Surface Finish Plays a Critical Role
The surface finish of a part affects not just its appearance but its performance. A poorly finished part may cause friction, noise, or accelerated wear when interacting with other components.
Why Surface Finish Matters in Precision Mechanical Parts
- Reduces friction and improves lubrication
- Enhances corrosion resistance
- Improves fatigue strength
- Ensures better sealing performance
Different applications require different surface finish specifications. For example:
Surface Finish Type | Typical Roughness (Ra) | Applications |
---|---|---|
Machined | 1.6–6.3 µm | General engineering |
Ground | 0.4–1.6 µm | Bearings, seals |
Lapped | 0.05–0.4 µm | Optical, semiconductor |
Polished | <0.05 µm | Medical devices, aerospace |
Collaborate with your manufacturing partner to specify the correct finish based on your application’s needs. Neglecting surface finish can lead to major issues down the line.
Tip 4: Consistency in Manufacturing Process Is Key
Even the most well-designed part can fail if it is not manufactured consistently. Consistency involves replicating exact dimensions, tolerances, and finishes across large production runs without deviation.
Key Factors in Maintaining Consistency
- Use of CNC machines and automated inspection systems
- Routine calibration of manufacturing equipment
- Consistent sourcing of raw materials
- Statistical Process Control (SPC)
Working with a manufacturer that specializes in precision mechanical parts production is critical. Ask about their quality assurance processes, certifications (like ISO 9001), and track record for meeting tight tolerances.
Consistency ensures that every unit in a production batch performs identically, reducing downtime, warranty claims, and system failures.
Tip 5: Inspection and Quality Control Should Never Be Skipped
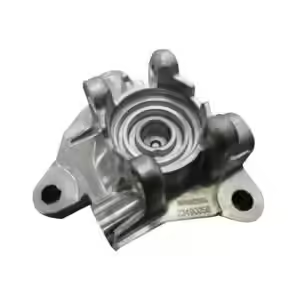
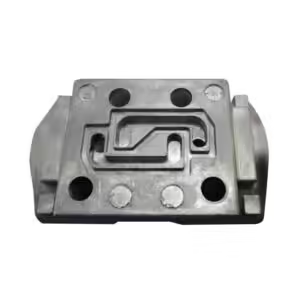
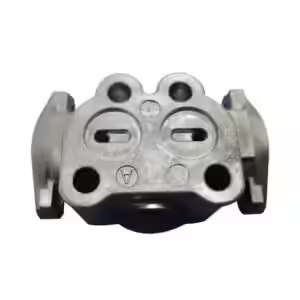
Inspection is often the final step before precision mechanical parts are shipped or installed. However, it’s not just a formality—it’s a vital part of ensuring reliability.
Inspection Techniques for Precision Mechanical Parts
- Mesin Pengukur Selaras (CMMs)
- Optical comparators
- Laser scanners
- Surface profilometers
- Go/No-Go gauges
Make sure your supplier has a documented inspection process and can provide measurement reports or certificates of conformance. Advanced industries such as aerospace and medical often require 100% inspection for all critical dimensions.
Even the best design and material choices are meaningless if the final product doesn’t meet specifications. Consistent, well-documented inspection practices ensure that your parts are ready for deployment with full confidence.
Kesimpulan
Precision mechanical parts are at the heart of many modern systems. From their material composition to final inspection, every step in their journey matters. Applying the five tips covered in this blog can help you avoid common mistakes, increase system reliability, and reduce long-term operational costs.
Whether you’re dealing with a few critical components or managing an entire supply chain, understanding these principles helps you make smarter decisions. Choosing the right material, maintaining tight tolerances, specifying surface finishes, ensuring process consistency, and verifying quality all contribute to achieving optimal performance.
By implementing these strategies, you’ll gain greater confidence in your products and processes while maintaining a competitive edge in your market.
Soalan Lazim
What industries commonly use precision mechanical parts?
Precision mechanical parts are widely used in aerospace, automotive, medical equipment, semiconductor manufacturing, robotics, and consumer electronics. Each industry demands specific tolerances, materials, and certifications to meet their high-performance and safety standards.
What is the typical lead time for custom precision mechanical parts?
Lead time varies by complexity and quantity. Simple parts usually take 1–2 weeks, moderately complex ones 3–6 weeks, and high-precision parts may require 6–10 weeks. Providing clear specifications early helps avoid delays.
How do I ensure my parts meet required tolerances?
Work with suppliers who use tools like CMMs and offer inspection reports. Clearly define GD&T in your drawings and confirm that quality control systems are in place before production begins.
Are 3D printed precision mechanical parts viable?
Yes, for prototyping or low-load applications, high-resolution 3D printing technologies like SLA or DMLS can produce usable precision mechanical parts. However, for mission-critical components, CNC machining or traditional methods are usually preferred.
How important is documentation for precision mechanical parts?
Extremely important. For regulated industries or complex assemblies, documentation ensures traceability, compliance, and repeatability. Request certificates of material, inspection, and even process validation when necessary.
Kategori Produk
- Bahagian Injap
- Bahagian Pam Air
- Bahagian Kotak Galas
- Bahagian Die Casting
- Produk Pam Keluli Tahan Karat
- Produk Pam Besi Tuang
- Bahagian Injap Untuk Kegunaan Kereta
- Bahagian Kenderaan
- Bahagian Injap Untuk Kegunaan Awam
- Bahagian Pam Vakum KF
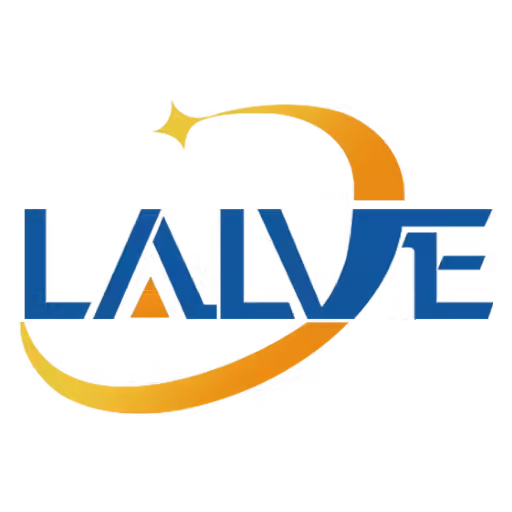