How to Spot High-Quality Precision Mechanical Parts Fast
Welcome to My Blog!
I’m thrilled to have you here! Before we dive into the content, I’d love for you to join me on my social media platforms. It’s where I share extra insights, connect with our amazing community, and keep you updated on the latest news. Here’s how you can stay connected:
📘 Facebook: Shanghai Leierwo Industry Trade Co., Ltd.
Now, let’s embark on this journey together! I hope you find the content here not only insightful but also inspiring and valuable. Let’s get started!
Table of Contents
Introduction
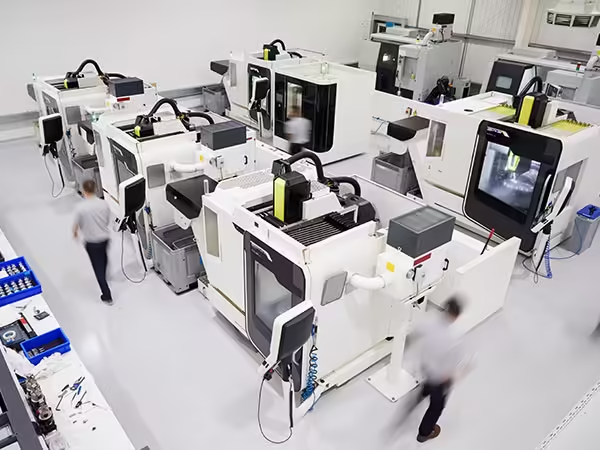
In today’s fast-paced manufacturing and engineering environments, the demand for quality precision mechanical parts is higher than ever. These components are critical in industries such as aerospace, automotive, robotics, medical devices, and industrial machinery. Their performance directly impacts the functionality, reliability, and safety of end products. Identifying quality precision mechanical parts quickly can significantly reduce production delays, maintenance costs, and operational risks.
This guide is designed to help engineers, buyers, and production managers efficiently evaluate mechanical components. From understanding materials to checking certifications, we will walk through the telltale signs of high-quality parts and how to avoid inferior ones.
Key Features of Quality Precision Mechanical Parts
To evaluate the integrity and performance of mechanical components, it’s essential to assess their defining attributes. Identifying these characteristics early helps in selecting parts that will perform reliably in demanding environments and under varying operational conditions. Here are the most common and crucial indicators of high-quality precision mechanical parts:
Material Composition and Certifications
The material used in quality precision mechanical parts determines their strength, resistance to corrosion, thermal stability, and wear life. Common materials include stainless steel, titanium, brass, and hardened alloys. Look for certification like ISO 9001, AS9100, or RoHS compliance to confirm quality standards.
Dimensional Tolerances
High-quality parts conform to tight dimensional tolerances as specified in engineering drawings. These tolerances ensure proper fit and function in assemblies. Use coordinate measuring machines (CMMs), calipers, and micrometers to verify accuracy.
Surface Finish and Coatings
Another significant indicator of quality is the surface finish. Quality precision mechanical parts exhibit uniform, smooth finishes that are free from burrs, scratches, tool marks, or other inconsistencies. The surface condition can affect everything from assembly fit to corrosion resistance and aesthetic appeal.
Additionally, many parts receive surface treatments to enhance their performance and life span. These treatments include anodizing (for aluminum parts), zinc or nickel plating (for corrosion resistance), heat treating (for hardness), and polishing or grinding (for precision mating surfaces). Proper surface treatment not only improves durability but also boosts functionality by minimizing friction or enhancing wear resistance.
Manufacturing Process
The quality of the manufacturing process has a direct correlation to the precision and consistency of the final product. State-of-the-art manufacturing techniques such as CNC (Computer Numerical Control) machining, laser cutting, electrical discharge machining (EDM), and injection molding are known for their ability to produce complex geometries with high repeatability.
Quality-focused manufacturers utilize automated in-process inspections and post-production testing to ensure every part meets strict quality criteria. The use of advanced CAD/CAM systems also allows for optimization of tool paths and better resource management, reducing errors and improving turnaround time. Moreover, the presence of robust process documentation and quality control checkpoints at each stage of manufacturing signifies a commitment to excellence.
Traceability and Documentation
Traceability is a critical quality control aspect in the modern manufacturing landscape. Each part should come with complete traceability records including batch numbers, inspection results, heat treatment logs, and raw material certificates. These records allow for root-cause analysis in case of failures, regulatory compliance, and easier recall procedures if necessary.
Comprehensive documentation not only supports internal quality audits but also builds trust between suppliers and clients. When every component can be tracked from raw material sourcing to final shipment, it demonstrates transparency and accountability, which are cornerstones of long-term business relationships.
In summary, the presence of proper materials, tight dimensional tolerances, flawless surface finishes, reliable production methods, and full documentation are hallmarks of quality precision mechanical parts. When all of these features align, manufacturers can achieve higher efficiency, longer product life, and fewer system failures.
Table: Comparison of High vs. Low-Quality Precision Mechanical Parts
Feature | High-Quality Parts | Low-Quality Parts |
---|---|---|
Material | Certified metals/alloys with known properties | Uncertified, inconsistent materials |
Tolerance Accuracy | Within tight specifications (micron-level) | Loose, inconsistent tolerances |
Surface Finish | Smooth, polished, free of defects | Rough, with burrs or visible machining marks |
Production Method | CNC, EDM, precision casting | Manual or outdated machining |
Quality Certifications | ISO, AS, RoHS, etc. | Usually absent |
Traceability Documentation | Complete and verifiable | Often missing or incomplete |
Durability and Performance | Long service life, high reliability | Prone to failure, reduced operational life |
Visual and Functional Inspection Techniques
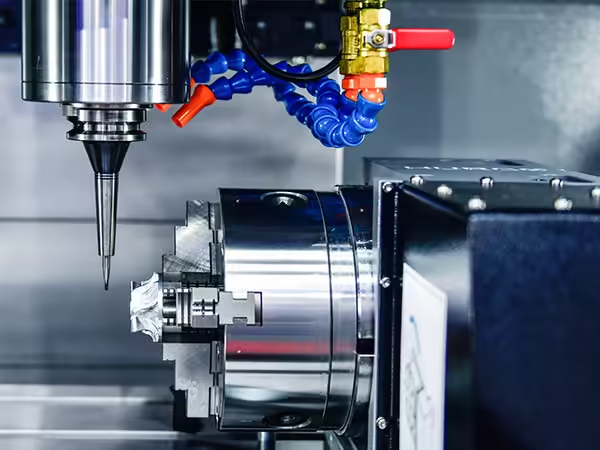
Before purchasing or installing components, it’s essential to conduct thorough visual and functional inspections to ensure that each part meets performance and quality expectations. These checks are often the first line of defense against defects and inconsistencies.
Visual Check
Examine the parts under good lighting conditions, preferably using magnification if necessary. Look for surface irregularities such as cracks, pits, burrs, scratches, and tool marks. A uniform surface finish and clearly etched or engraved markings (e.g., part number, batch code) indicate careful production.
Compare the physical part with the engineering blueprint or CAD drawing, ensuring that all features—holes, threads, grooves, and fillets—are present and correctly sized. High-quality components should exhibit no signs of surface contamination, rust, or discoloration.
Dimensional Verification
Confirm that all critical dimensions match the specifications by using precision measurement instruments like micrometers, digital calipers, height gauges, and CMMs. Cross-reference these results with inspection reports from the supplier, if available, to validate quality claims.
Where available, examine the statistical process control (SPC) data for the batch to assess variation levels and consistency in manufacturing. Consistent part dimensions reflect a stable production process and reduce assembly complications.
Function Testing
For components that serve a specific mechanical function—such as rotating, sealing, or load-bearing parts—functional testing can provide further validation. These tests may include:
- Test-fitting into actual or simulated assemblies to verify fitment.
- Load or pressure simulations to check for deformation or leakage.
- Rotation or movement tests to ensure alignment and clearance.
Functional tests help identify potential issues that visual and dimensional inspections may miss, particularly in dynamic systems.
Vendor Evaluation
Beyond the parts themselves, evaluating the vendor’s reliability is crucial. A high-quality component is often the result of a robust quality management system upheld by the supplier.
Choose suppliers with a proven track record in delivering consistent and high-quality precision mechanical parts. Review their customer testimonials, online reviews, and industry certifications. Suppliers with strong documentation, responsive customer support, and flexible customization capabilities often prove more valuable in the long term.
Site visits, sample evaluations, and third-party audits can further reinforce vendor credibility. A reliable vendor not only ensures product quality but also helps mitigate supply chain disruptions.
In summary, conducting a structured visual and functional inspection—combined with careful vendor selection—ensures that only quality precision mechanical parts make it into your system. This proactive approach minimizes risks, reduces costs, and supports long-term operational excellence.
Best Practices to Ensure Consistent Quality
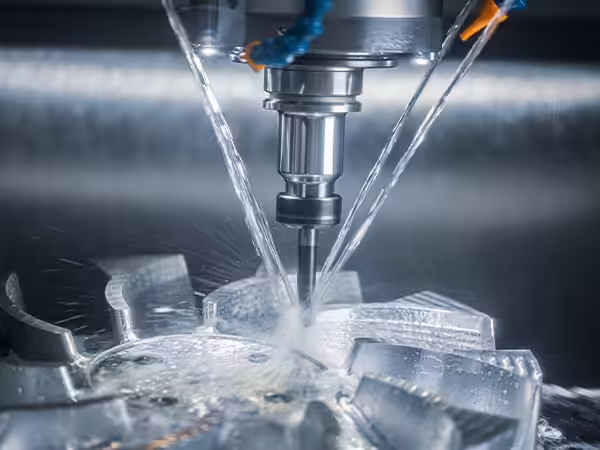
Partner with Certified Suppliers
Working with vendors who specialize in quality precision mechanical parts and hold certifications like ISO 9001 ensures a baseline of quality assurance. Certified companies often follow strict quality control and continuous improvement protocols that contribute to more consistent product performance.
Request Sample Parts
Before placing large orders, request sample components of quality precision mechanical parts to evaluate their workmanship, tolerance conformity, and documentation. Samples help in validating product consistency before making large-scale procurement decisions.
Audit Quality Processes
If possible, audit your supplier’s production facility. Look for clean, organized workspaces, modern machinery, and skilled technicians capable of consistently producing quality precision mechanical parts. These audits give insight into the overall quality culture of the vendor.
Use Quality Assurance Contracts
Establish written agreements that specify required tolerances, acceptable material standards, and inspection processes for all quality precision mechanical parts. This documentation protects both buyer and seller by clarifying quality expectations and creating a standard for accountability.
Conclusion
The cost of choosing subpar components goes beyond monetary losses. It affects reputation, customer satisfaction, safety, and system performance. By learning how to quickly identify quality precision mechanical parts, companies can streamline production, reduce waste, and build reliable products.
Paying attention to details like material grade, dimensional accuracy, manufacturing method, and supplier reliability makes a significant difference. Use this guide as a checklist to verify components before procurement or installation.
FAQ
What industries use quality precision mechanical parts?
Industries such as aerospace, automotive, medical devices, industrial automation, and electronics rely heavily on high-quality mechanical parts for critical systems.
How do I verify the tolerance of a mechanical part?
Use measurement tools like micrometers, calipers, and CMMs. Tolerance information is usually provided on the engineering drawing or technical datasheet.
Can visual inspection determine part quality?
Yes, visual inspection can help spot surface defects, poor finishes, or material inconsistencies. However, it should be supplemented with measurement and function testing.
Why are certifications important for mechanical parts?
Certifications ensure that the parts meet standardized requirements for safety, performance, and environmental compliance. They also improve traceability.
What’s the risk of using low-quality mechanical parts?
Poor-quality parts can fail under load, cause assembly errors, and lead to costly downtime or safety hazards.
Product Categories
- Valve Parts
- Water Pump Parts
- Bearing Box Parts
- Die Casting Parts
- Stainless Steel Pump Products
- Cast Iron Pump Products
- Valve Parts For Automobile Use
- Auto Parts
- Valve Parts For Civil Use
- Vacuum Pump Parts KF
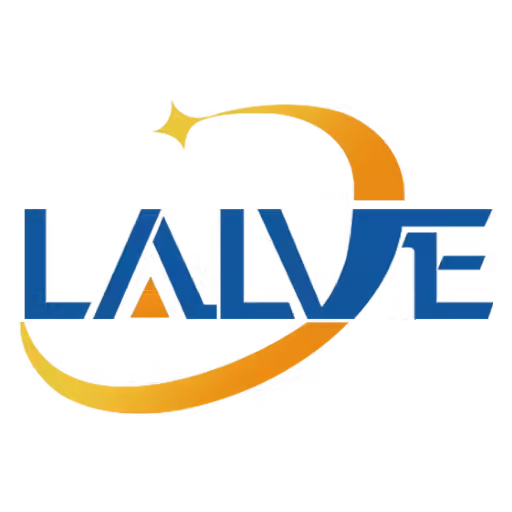