Difference Between Duplex and Super Duplex Steel:5 Key Facts
Willkommen auf meinem Blog!
Ich freue mich sehr, dass du hier bist! Bevor wir uns in die Inhalte vertiefen, würde ich mich freuen, wenn du mir auf meinen Social-Media-Plattformen folgst. Dort teile ich zusätzliche Einblicke, vernetze mich mit unserer großartigen Community und halte dich über die neuesten Nachrichten auf dem Laufenden. So bleibst du in Verbindung:
📘 Facebook: Shanghai Leierwo Industriehandel Co., Ltd.
Lassen Sie uns gemeinsam auf diese Reise gehen! Ich hoffe, Sie finden die Inhalte hier nicht nur aufschlussreich, sondern auch inspirierend und wertvoll. Los geht‘s!
Inhaltsverzeichnis
Einführung
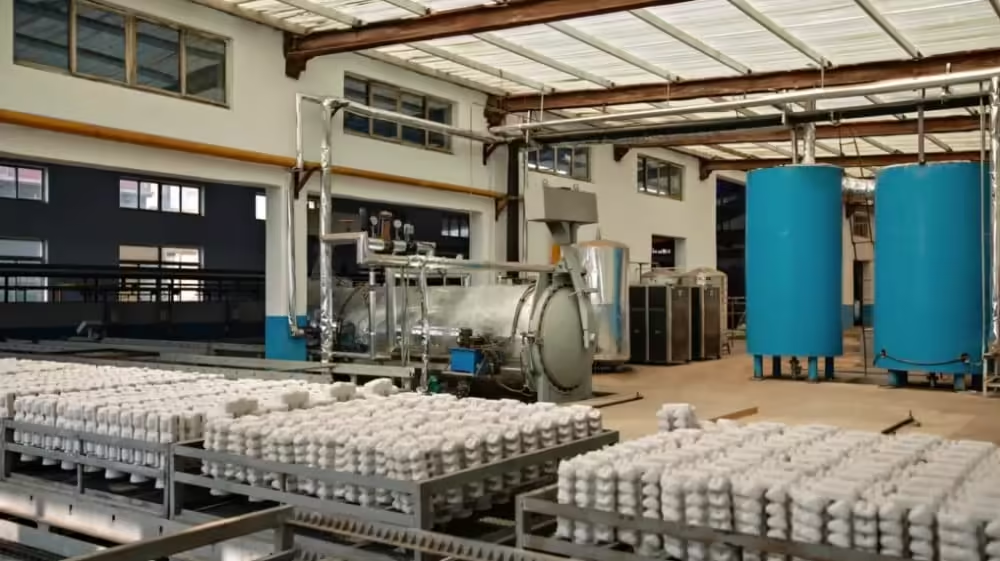
In today’s industrial landscape, material selection is critical to the success of engineering and structural applications. When it comes to choosing the right stainless steel for environments with high stress, corrosion, and temperature demands, duplex and super duplex steels are top contenders.
Understanding the difference between duplex and super duplex steel is not merely a technical detail—it influences performance, longevity, and cost-effectiveness in industries like chemical processing, oil and gas, desalination, and marine engineering. While both categories fall under the duplex family, which blends the strength of ferritic and austenitic stainless steel, their chemical compositions, corrosion resistance, and mechanical properties vary significantly.
This article dives deep into the five key differences between duplex and super duplex steel to help engineers, buyers, and technical professionals make informed decisions. You’ll also find a comparative table in the middle of the post for quick reference, followed by FAQs to clarify the most common questions.
1. Composition Differences Between Duplex and Super Duplex Steel
A fundamental way to understand the difference between duplex and super duplex steel is by examining their chemical makeup. While both belong to the duplex family—meaning they share a dual-phase microstructure of roughly equal parts austenite and ferrite—the specific proportions of critical alloying elements are what set them apart.
The composition directly influences the steel’s resistance to corrosion, mechanical strength, and suitability for different industrial applications. In most cases, super duplex steel is considered an enhanced version of duplex due to its higher alloy content, making it more resilient in severe service environments.
Key Alloying Components:
- Chromium Content: Duplex steel typically contains 21–23% chromium, whereas super duplex ranges from 24–26%. This added chromium increases the material’s resistance to pitting and crevice corrosion.
- Molybdenum Content: Duplex grades usually feature 2–3% molybdenum, but super duplex includes up to 4%. Molybdenum is especially effective in enhancing resistance to localized corrosion in chloride-rich environments.
- Nickel Content: The nickel percentage in duplex steel often falls between 4–6%, while in super duplex it can reach 6–8%. Higher nickel improves ductility and overall impact toughness, particularly at lower temperatures.
- Nitrogen and Other Additives: Super duplex steel may also contain elevated nitrogen levels and small amounts of copper, both of which contribute to greater tensile strength and corrosion resistance.
Understanding the difference between duplex and super duplex steel from a compositional perspective is essential for engineers selecting materials for chemical processing, marine structures, or oil and gas installations. The enhanced alloy content in super duplex allows for longer service life in harsh conditions, making it a preferred choice where failure is not an option.
2. Corrosion Resistance: A Defining Difference Between Duplex and Super Duplex Steel
One of the most critical performance distinctions in the difference between duplex and super duplex steel lies in their ability to resist corrosion. Both materials are designed to withstand harsh environments, but super duplex steel provides superior protection in particularly aggressive or high-salinity conditions.
This added resilience is directly tied to its enhanced composition, allowing super duplex steel to thrive in industries where corrosion is a constant concern, such as offshore oil drilling, desalination, and high-pressure chemical processing.
Resistance Characteristics:
- Pitting Resistance Equivalent Number (PREN): PREN is a calculated value based on the levels of chromium, molybdenum, and nitrogen in the steel. Duplex steels generally have a PREN between 30 and 38, while super duplex steels boast values over 40. A higher PREN indicates better resistance to pitting, particularly in seawater or chloride-heavy environments.
- Stress Corrosion Cracking (SCC): Super duplex steel offers enhanced resistance to stress corrosion cracking—a form of sudden failure caused by the combination of tensile stress and a corrosive environment. This property is especially valuable in subsea pipelines and pressure vessels.
- Localized and Uniform Corrosion: Thanks to higher levels of protective alloying elements, super duplex performs more reliably against both localized attacks like pitting and broader surface degradation over time.
For engineers and project managers evaluating the difference between duplex and super duplex steel, corrosion resistance is often the deciding factor. In fact, material failure due to inadequate corrosion protection can lead to costly repairs, safety hazards, and environmental violations. Super duplex steel, with its increased resistance, offers peace of mind and long-term reliability in such scenarios.
3. Mechanical Strength and Toughness Comparison
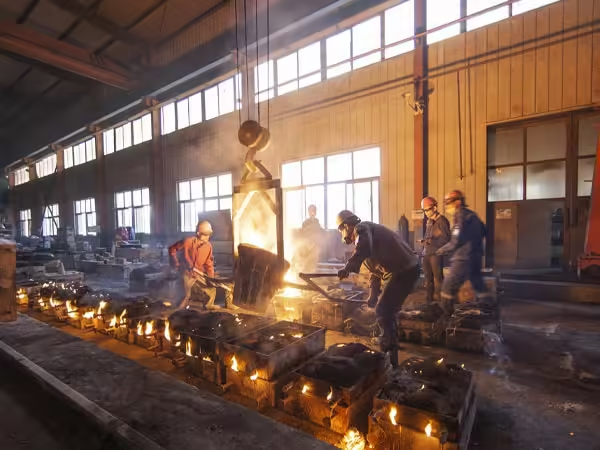
Another key area where the difference between duplex and super duplex steel becomes evident is in mechanical performance. Both materials surpass standard austenitic stainless steels when it comes to strength and fatigue resistance, but super duplex offers even greater benefits due to its refined microstructure and enhanced composition.
Mechanical Property Comparison:
- Yield Strength: Duplex steel offers a yield strength around 450 MPa, whereas super duplex can exceed 550 MPa.
- Tensile Strength: Super duplex also tends to outperform duplex steel in tensile strength, providing higher load-bearing capacity.
- Impact Toughness: At low temperatures, super duplex maintains better ductility and impact strength due to its refined microstructure and nickel content.
This increased strength means that components can be manufactured with thinner walls while maintaining performance, resulting in weight and cost savings in structural designs.
4. Applications: Where the Difference Between Duplex and Super Duplex Steel Matters
Choosing between duplex and super duplex steel often comes down to the specific application. The added strength and corrosion resistance of super duplex make it suitable for more aggressive environments, whereas duplex steel suffices in moderately corrosive or mechanical conditions.
Typical Use Cases:
Application Area | Duplex Steel | Super Duplex Steel |
---|---|---|
Offshore Platforms | Piping, supports (non-critical zones) | Critical load-bearing structures, risers |
Chemical Processing | Storage tanks, process lines | High-pressure vessels, pumps |
Marine Engineering | Hull plating, structural supports | Propeller shafts, submerged components |
Desalination Plants | Brackish water treatment systems | Seawater intake and outfall structures |
Pulp and Paper Industry | Digesters, tanks | Chloride-exposed processing units |
Heat Exchangers and Condensers | Moderate-duty exchangers | High-efficiency, corrosion-prone units |
In applications involving seawater, chlorides, or acidic compounds, using super duplex is often not just a recommendation—it’s a necessity.
5. Cost and Weldability: Practical Considerations
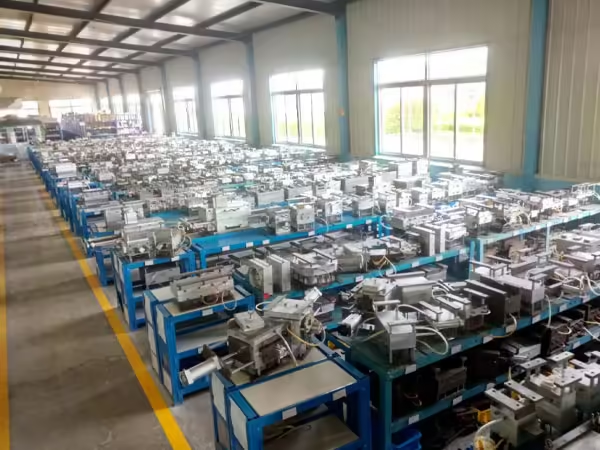
While performance often dictates material choice, cost and fabrication requirements can’t be overlooked when assessing the difference between duplex and super duplex steel. Selecting the right material involves more than technical specifications—it also requires a close look at economic and operational feasibility.
Cost Considerations:
- Material Cost: One of the most noticeable factors in the difference between duplex and super duplex steel is price. Super duplex steel is typically 20–30% more expensive due to its higher alloy composition and specialized production processes.
- Welding Requirements: Another important difference between duplex and super duplex steel lies in weldability. Super duplex steel demands strict control over temperature and cooling rates during welding to prevent phase imbalance and cracking. Duplex steel, by contrast, is more tolerant, reducing the need for advanced procedures and lowering fabrication costs.
- Availability: In terms of availability, duplex steel is easier to source in a variety of standard sizes and grades. The difference between duplex and super duplex steel in this regard can affect procurement lead times and material logistics for time-sensitive projects.
For engineers and project managers working with tight budgets or moderate corrosive exposure, duplex steel offers a cost-effective solution. However, in environments where failure is not an option, the difference between duplex and super duplex steel justifies the higher initial investment in super duplex, thanks to its reduced lifetime maintenance costs and superior durability.
Abschluss
Understanding the difference between duplex and super duplex steel is fundamental for selecting the right material in environments where mechanical performance and corrosion resistance are mission-critical. While both types offer excellent properties compared to standard stainless steels, the superior strength, corrosion resistance, and performance under pressure make super duplex the material of choice in more extreme applications.
Still, duplex steel holds a strong position where cost efficiency and moderate performance are acceptable. Engineers and procurement specialists should weigh these five key differences—composition, corrosion resistance, mechanical strength, applications, and cost—before making a final selection.
In the long term, making the correct material decision based on these differences can significantly improve system reliability, reduce maintenance costs, and ensure compliance with industry standards.
Häufig gestellte Fragen
What is the main difference between duplex and super duplex steel?
The primary difference is the alloy content. Super duplex contains more chromium, molybdenum, and nickel, offering superior strength and corrosion resistance compared to standard duplex steel.
Can duplex and super duplex steel be used interchangeably?
In some cases, yes—but not in highly corrosive or high-stress environments where super duplex is essential. Interchanging them without proper assessment can lead to material failure.
Is super duplex always the better option?
Not necessarily. While it provides better performance, it is more expensive and harder to weld. For less demanding environments, duplex may be more cost-effective.
How do I know if I need super duplex for my project?
If your application involves high chloride levels, seawater exposure, or intense mechanical stress, super duplex is the safer and more reliable option.
Is there a noticeable difference in service life?
Yes. In harsh environments, super duplex steel can offer a significantly longer service life due to its superior resistance to pitting, crevice corrosion, and mechanical fatigue.
Produktkategorien
- Ventilteile
- Wasserpumpenteile
- Lagergehäuseteile
- Druckgussteile
- Pumpenprodukte aus Edelstahl
- Pumpenprodukte aus Gusseisen
- Ventilteile für den Automobilgebrauch
- Autoteile
- Ventilteile für den zivilen Gebrauch
- Vakuumpumpenteile KF
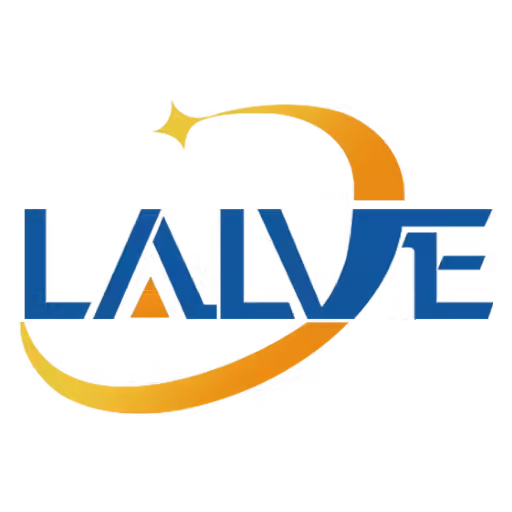