7 nachgewiesene Vorteile hochwertiger Ventilgussteile für die Kerntechnik
Willkommen auf meinem Blog!
Ich freue mich sehr, dass du hier bist! Bevor wir uns in die Inhalte vertiefen, würde ich mich freuen, wenn du mir auf meinen Social-Media-Plattformen folgst. Dort teile ich zusätzliche Einblicke, vernetze mich mit unserer großartigen Community und halte dich über die neuesten Nachrichten auf dem Laufenden. So bleibst du in Verbindung:
📘 Facebook: Shanghai Leierwo Industriehandel Co., Ltd.
Lassen Sie uns gemeinsam auf diese Reise gehen! Ich hoffe, Sie finden die Inhalte hier nicht nur aufschlussreich, sondern auch inspirierend und wertvoll. Los geht‘s!
Inhaltsverzeichnis
Einführung
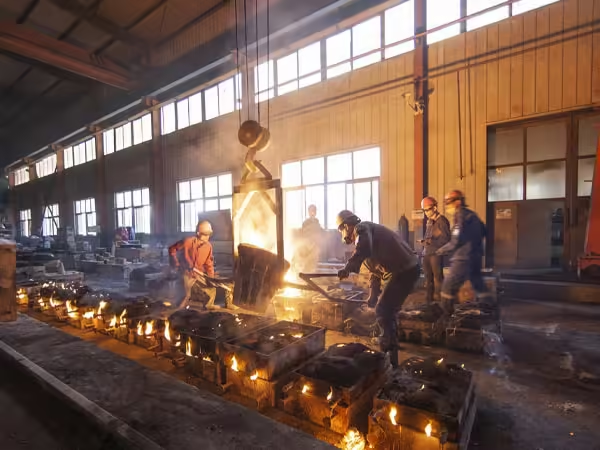
In the nuclear energy industry, precision, reliability, and safety are non-negotiable. One of the most critical components ensuring operational integrity within nuclear reactors and related systems is Gussteile für Kernventile. These specialized cast components are integral in controlling and managing the flow of gases, liquids, and radioactive materials in a nuclear facility. The quality of these castings directly influences system safety, operational efficiency, and compliance with regulatory standards. This article explores the seven proven benefits of high-quality nuclear valve castings and how they impact nuclear operations.
NO 1. Enhanced Operational Safety with Quality Nuclear Valve Castings
Safety is paramount in any nuclear facility. High-quality nuclear valve castings play a crucial role in maintaining secure containment of potentially hazardous materials. Their structural integrity ensures that valves function under extreme pressure and temperature conditions without failure. This reduces the risk of leaks, contamination, and system malfunctions, which could lead to severe safety incidents.
The production of Gussteile für Kernventile involves stringent quality control measures, including advanced non-destructive testing, to identify internal flaws. This meticulous approach ensures the final products meet the demanding requirements of nuclear environments, thus safeguarding both personnel and the environment.
Additionally, robust safety features integrated into high-grade castings—such as pressure-relief capabilities and fail-safe mechanisms—contribute to accident prevention. With each casting thoroughly examined, facilities can operate with greater confidence and reduced risk exposure.
NO 2. Improved Durability and Resistance to Corrosion
Nuclear environments often involve exposure to corrosive substances and high radiation levels. Quality Gussteile für Kernventile are manufactured using specialized alloys and heat treatment processes that enhance their resistance to corrosion and radiation-induced degradation.
Durable valve castings reduce maintenance frequency and extend the life of the equipment. They also perform reliably under long-term exposure to extreme conditions, which is essential for minimizing downtime and maintaining the continuous operation of nuclear power plants.
Moreover, the corrosion resistance of these components directly affects the purity and safety of nuclear processes. When valve castings maintain integrity, they help prevent the release of radioactive substances, ensuring environmental protection and compliance with international safety standards.
NO 3. Precision Engineering Ensures Performance Consistency
Consistency in performance is vital for the smooth operation of nuclear reactors. Nuclear valve castings that are manufactured to exacting standards provide uniform flow control, which is essential in critical systems like coolant loops and containment isolation.
Precision engineering ensures minimal variation between individual valve components, which leads to better system predictability and reduces the chances of performance discrepancies. This benefit becomes particularly important during system audits, stress testing, and when scaling operations.
Furthermore, precision-engineered castings streamline integration with automated control systems. This compatibility is essential for modern nuclear facilities that rely on digital monitoring and response protocols to ensure optimal performance and rapid diagnostics during abnormal events.
NO 4. Cost-Efficiency Over the Long Term
While high-quality Gussteile für Kernventile might involve a higher initial investment, they offer substantial cost savings over time. Their durability and resistance to wear mean fewer replacements and lower maintenance costs. Furthermore, their reliability contributes to fewer unplanned shutdowns, which can be financially catastrophic in nuclear operations.
Cost-efficiency is not only about direct savings but also includes avoiding regulatory penalties, litigation, or environmental cleanup associated with component failures. Reliable castings are a long-term investment in operational stability.
Additionally, reducing the frequency of component failure and replacement minimizes operational disruptions and logistics expenses. The long service life of superior valve castings translates into less waste, further supporting cost reduction and sustainability goals within nuclear energy systems.
NO 5. Compliance with Nuclear Industry Standards
Nuclear valve castings must meet rigorous industry standards, including ASME, ASTM, and ISO specifications. Quality manufacturers ensure that their products are fully compliant with these standards, which is critical for gaining regulatory approvals and operating licenses.
Compliance also demonstrates a commitment to safety and quality, helping nuclear operators build trust with regulators and stakeholders. Below is a table summarizing key standards and how quality valve castings meet or exceed them.
Compliance Table for Nuclear Valve Castings
Standard | Description | How Quality Castings Comply |
---|---|---|
ASME Section III | Rules for construction of nuclear facility components | Use of certified materials and testing methods |
ASTM A351 | Standard for castings for pressure-containing parts | Use of corrosion-resistant alloys |
ISO 9001 | Quality management system requirements | Documented procedures and traceability |
NQA-1 | Nuclear quality assurance requirements | Full QA/QC program implementation |
PED | Pressure Equipment Directive (EU compliance) | CE marking and material traceability |
NO 6. Customization Capabilities for Specialized Applications
Nuclear valve castings are highly specialized components that must meet the distinct needs of each nuclear facility. Unlike generic valve castings, these are often tailored to the specific reactor design, system layout, and operational requirements. Quality casting manufacturers provide comprehensive customization services to ensure every valve casting perfectly fits its intended application.
Customization options include:
- Design Modifications: Alterations in valve body geometry to improve flow efficiency or fit within confined spaces.
- Material Selection: Use of specialized alloys or coatings tailored to resist specific corrosive environments or radiation exposure.
- Integrated Features: Embedding sensors or ports for real-time monitoring of pressure, temperature, or valve position.
- Surface Treatments: Application of advanced coatings or heat treatments to enhance durability and corrosion resistance beyond standard specifications.
These capabilities allow nuclear operators to address unique challenges, such as accommodating new reactor technologies, adapting to regulatory changes, or upgrading existing systems without complete overhauls. Customized nuclear valve castings facilitate optimal performance, safety, and longevity, aligning with the constantly evolving landscape of nuclear technology.
Moreover, having a trusted partner that can rapidly produce bespoke castings reduces lead times and improves project timelines, a critical factor in large-scale nuclear installations or upgrades.
NO 7. Supporting Sustainability and Waste Reduction
Sustainability is becoming a fundamental goal within the nuclear energy sector, and quality nuclear valve castings contribute significantly to this effort. By enhancing component longevity and reliability, these castings reduce the need for frequent replacements, which directly cuts down on material waste and environmental impact.
Key sustainability benefits include:
- Extended Equipment Lifespan: Durable castings withstand harsh operating conditions, minimizing the frequency of part failure and replacement.
- Reduced Radioactive Waste: Lower failure rates mean fewer maintenance interventions and less handling of potentially contaminated parts.
- Environmentally Conscious Manufacturing: Leading casting producers increasingly adopt eco-friendly practices such as recycling metal scrap, optimizing energy consumption in furnaces, and reducing emissions during the casting process.
Furthermore, by supporting stable and efficient nuclear operations, quality valve castings indirectly promote cleaner energy production. Reliable components reduce unplanned outages, which in turn lowers reliance on backup fossil fuel generators, thus decreasing greenhouse gas emissions.
As global energy policies emphasize sustainability and carbon reduction, investing in premium nuclear valve castings aligns with broader environmental goals. It demonstrates a commitment not only to operational excellence but also to responsible stewardship of natural resources and public safety.
Abschluss
Investing in high-quality Gussteile für Kernventile is more than a technical decision—it’s a strategic one. These components influence nearly every aspect of nuclear plant operation, from safety and compliance to efficiency and sustainability. The seven benefits highlighted above underscore the value that precision-engineered, rigorously tested castings bring to the nuclear industry. As demand for clean energy continues to rise, the role of reliable nuclear infrastructure, including valve systems, becomes increasingly important.
Choosing the right casting supplier and emphasizing quality at every production stage will yield long-term dividends in performance, safety, and regulatory success.
Häufig gestellte Fragen
What materials are used in Gussteile für Kernventile?
Typically, stainless steels, duplex steels, and special high-alloy materials are used to ensure corrosion resistance and strength.
How are nuclear valve castings tested for quality?
Non-destructive testing methods such as radiography, ultrasonic testing, and dye penetrant inspection are commonly employed.
Why is customization important in valve casting?
Each nuclear facility has unique operational requirements. Custom castings ensure the valve meets exact flow, pressure, and space constraints.
Can poor quality castings lead to safety incidents?
Yes. Defective castings can lead to valve failure, leaks, or even system shutdowns, which compromise plant safety.
Are quality Gussteile für Kernventile more expensive?
They may have a higher upfront cost, but the long-term savings in maintenance, downtime, and risk management make them more economical overall.
Produktkategorien
- Ventilteile
- Wasserpumpenteile
- Lagergehäuseteile
- Druckgussteile
- Pumpenprodukte aus Edelstahl
- Pumpenprodukte aus Gusseisen
- Ventilteile für den Automobilgebrauch
- Autoteile
- Ventilteile für den zivilen Gebrauch
- Vakuumpumpenteile KF
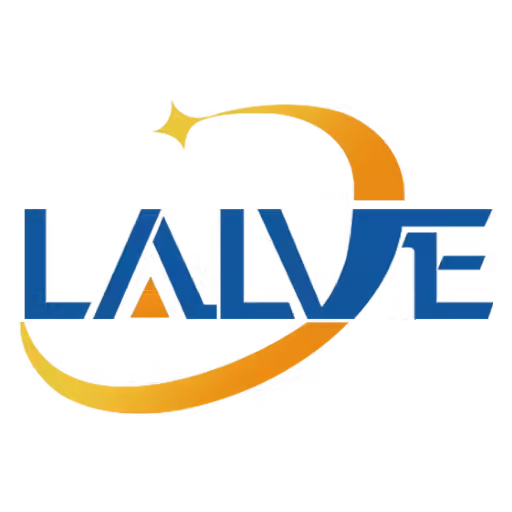