Common Pitfalls in Valve Body Castings You Must Avoid
Welcome to My Blog!
I’m thrilled to have you here! Before we dive into the content, I’d love for you to join me on my social media platforms. It’s where I share extra insights, connect with our amazing community, and keep you updated on the latest news. Here’s how you can stay connected:
📘 Facebook: Shanghai Leierwo Industry Trade Co., Ltd.
Now, let’s embark on this journey together! I hope you find the content here not only insightful but also inspiring and valuable. Let’s get started!
Table of Contents
Introduction
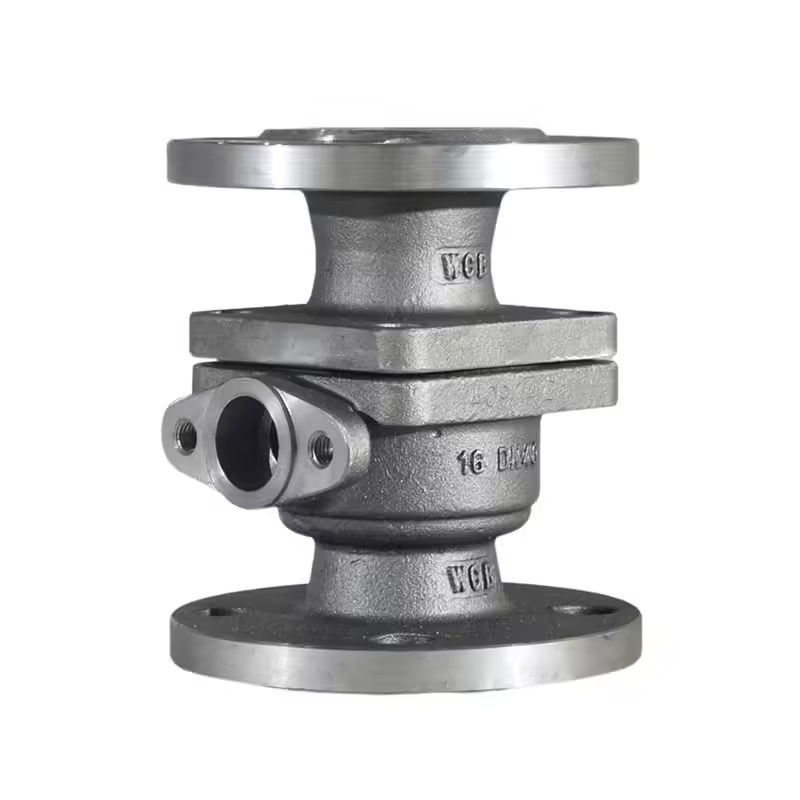
Valve body castings are critical components in many industrial applications, from automotive engines to hydraulic systems. They serve as the foundation for the smooth operation of valves, which regulate the flow of liquids or gases. However, like any manufacturing process, there are pitfalls that come with choosing poor-quality valve body castings. These hidden dangers can have long-term implications on equipment performance, safety, and maintenance costs. In this article, we will explore the hidden pitfalls of poor valve body castings, the risks they pose, and how to avoid these issues by choosing the right supplier.
The Importance of Quality in Valve Body Castings
When it comes to industrial components like valve bodies, ensuring top-tier quality is non-negotiable. A defective casting can trigger severe consequences such as leaks, system inefficiency, and premature wear. Understanding the key characteristics of high-quality castings is crucial for any operation relying on such components. Precision is a hallmark of well-made valve bodies, encompassing the correct material composition, a smooth surface finish, and consistent wall thickness. These factors are essential in ensuring that the component can withstand the environmental stresses and operational pressures it will face in service.
In contrast, low-quality components made from poorly executed castings often carry inherent risks. These include material defects, cracks, or inconsistencies in thickness, all of which can compromise the functioning of the entire system. Even minor imperfections, such as small cracks or surface irregularities, can result in costly repairs and unexpected downtime. Therefore, understanding the common pitfalls associated with subpar valve body manufacturing—and how to avoid them—is a crucial step in protecting the integrity and longevity of industrial equipment.
Common Pitfalls of Poor Castings in Valve Bodies
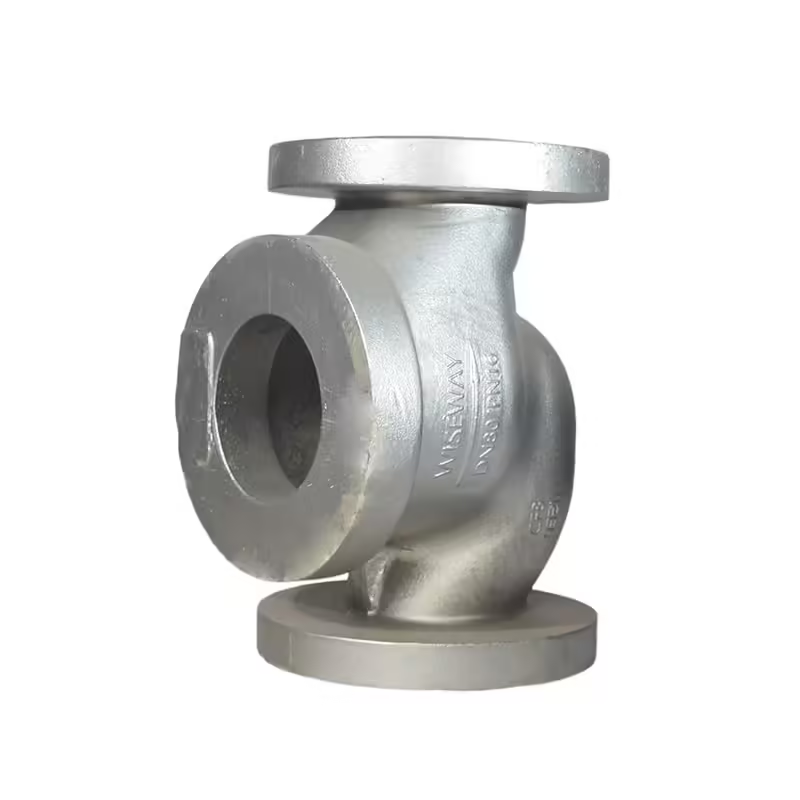
Material Inconsistencies
One of the most significant drawbacks of using poorly manufactured valve bodies is material inconsistency. If the material alloy isn’t closely controlled or if the casting process introduces impurities, the final product can be structurally compromised. For instance, valve bodies with excess carbon content may become brittle and prone to cracking under pressure. Variations in material quality can affect the overall durability and performance of the valve, increasing the risk of unexpected failures and malfunctions.
Improper Heat Treatment
Heat treatment plays a pivotal role in ensuring the strength and durability of the final product. When castings are subjected to incorrect temperatures or uneven heating, it can result in areas of uneven hardness, leading to weak points within the component. These weak points can ultimately lead to failure during normal operational conditions. Proper heat treatment ensures that the valve body reaches the desired mechanical properties, allowing it to perform reliably under harsh conditions.
Dimensional Inaccuracies
Dimensional precision is another key aspect that defines a high-quality valve body. Castings that suffer from issues like excessive shrinkage, warping, or distortion can lead to improper fits, causing sealing problems and potential leaks. Even small dimensional inaccuracies can impact the performance of the system, resulting in inefficient flow and increased chances of malfunction. Ensuring that valve bodies conform to precise dimensions is critical for achieving optimal sealing and functioning in complex systems.
Surface Defects
Surface quality is equally important. Defects such as porosity, cracks, or rough finishes can compromise the performance of valve bodies. Porosity refers to small voids or holes that form within the casting, which create weak spots that can eventually lead to leaks. Cracks on the surface further weaken the integrity of the valve, leading to reduced lifespan and poor operational performance. A rough surface finish can also impede the ability of the valve to properly seal, leading to fluid inefficiencies and eventual failure.
Lack of Rigorous Quality Control
One of the most serious issues associated with poor-quality valve bodies is the lack of effective quality control during production. When manufacturing processes aren’t thoroughly monitored or inspected, flaws that affect the mechanical and structural integrity of the valve may go undetected. These defects can cause operational issues and increase the risk of failure under normal working conditions. Leading manufacturers typically employ comprehensive testing methods, such as X-ray and ultrasonic inspections, along with visual checks, to ensure that every component adheres to the highest industry standards.
Table: Common Issues in Valve Body Castings and Their Effects
Issue | Effect on Performance | Potential Consequences |
---|---|---|
Material Inconsistencies | Weakened structure, premature failure | Cracking, corrosion, reduced lifespan |
Improper Heat Treatment | Uneven hardness, weak points | Valve failure, structural weakness |
Dimensional Inaccuracies | Poor fit, leakage, inefficiency | System malfunction, leakage |
Surface Defects | Reduced sealing capabilities | Leaks, inefficient fluid control |
Lack of Quality Control | Undetected defects, unreliable performance | Increased maintenance, system downtime |
How to Avoid the Pitfalls of Poor Valve Body Castings
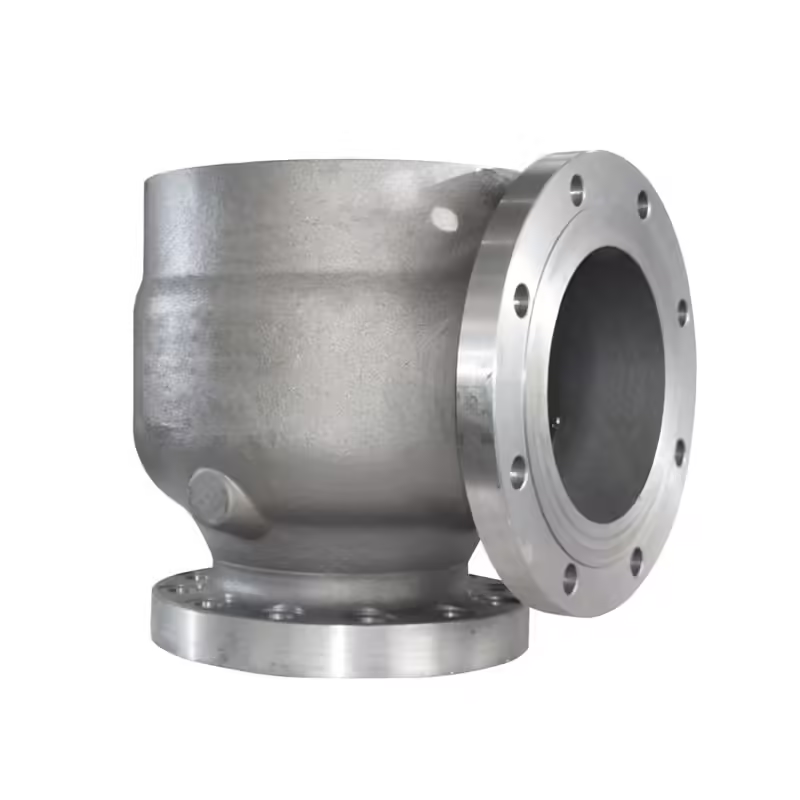
To avoid the risks associated with low-quality valve bodies, selecting a manufacturer who upholds rigorous quality control practices is essential. Here are some steps to help you choose the right supplier:
Verify Certifications and Standards
Choose manufacturers who are certified by international quality standards such as ISO 9001. Certification ensures that the manufacturer adheres to a reliable quality management system and consistently produces high-standard castings.
Request Material and Testing Certifications
A reputable manufacturer will provide documentation that verifies the material composition and mechanical properties of their products. Material certificates guarantee that the valve body meets the required specifications and is free from defects.
Demand Regular Inspections and Testing
Ensure that the manufacturer conducts thorough inspections throughout the production process. This includes dimensional checks, surface quality assessments, and advanced testing like ultrasonic or X-ray inspections to detect hidden defects that could compromise performance.
Consider Custom Solutions for Unique Requirements
For highly specialized applications, some suppliers offer custom valve bodies tailored to specific needs. Customization can help ensure that the product is fit for its intended use and meets unique operational requirements, providing additional confidence in its performance and durability.
Conclusion
The hidden pitfalls of poor valve body castings can significantly impact the performance, durability, and reliability of your equipment. By being aware of these risks and selecting a reputable supplier, you can ensure that your valve body castings are of the highest quality and meet your application’s requirements. Remember, quality control, material consistency, and thorough testing are key to avoiding costly repairs, downtime, and system failures.
FAQ
What is the best material for valve body castings?
The best material depends on the application, but commonly used materials include cast iron, steel, and stainless steel, all of which offer different advantages depending on the operating environment and pressure requirements.
How can I ensure my valve body castings meet quality standards?
Look for suppliers with ISO certifications, ensure they use modern quality control practices, and request material certificates to verify the specifications.
Why are surface defects in valve body castings so problematic?
Surface defects, such as cracks or porosity, can lead to leaks, which reduce the efficiency of fluid control and compromise system integrity.
Can I get customized valve body castings?
Yes, many manufacturers offer customized valve body castings to meet specific design, material, or performance needs.
What are the common applications for valve body castings?
Valve body castings are widely used in industries such as oil and gas, automotive, power generation, and water treatment for controlling the flow of liquids and gases.
Product Categories
- Valve Parts
- Water Pump Parts
- Bearing Box Parts
- Die Casting Parts
- Stainless Steel Pump Products
- Cast Iron Pump Products
- Valve Parts For Automobile Use
- Auto Parts
- Valve Parts For Civil Use
- Vacuum Pump Parts KF
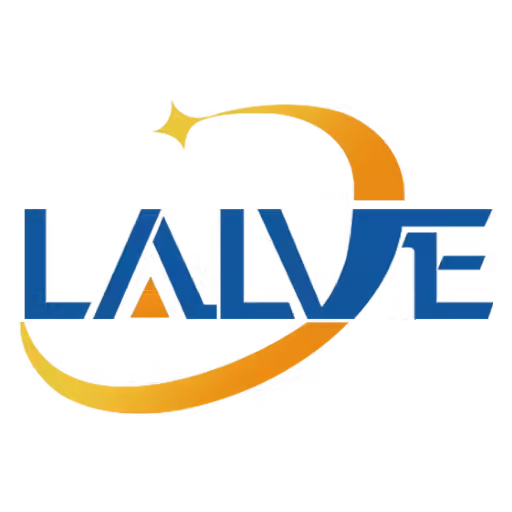