Why the Impeller Casting Process Excels in 2025
مرحباً بكم في مدونتي!
I’m thrilled to have you here! Before we dive into the content, I’d love for you to join me on my social media platforms. It’s where I share extra insights, connect with our amazing community, and keep you updated on the latest news. Here’s how you can stay connected:
📘 Facebook: Shanghai Leierwo Industry Trade Co., Ltd.
Now, let’s embark on this journey together! I hope you find the content here not only insightful but also inspiring and valuable. Let’s get started!
جدول المحتويات
مقدمة
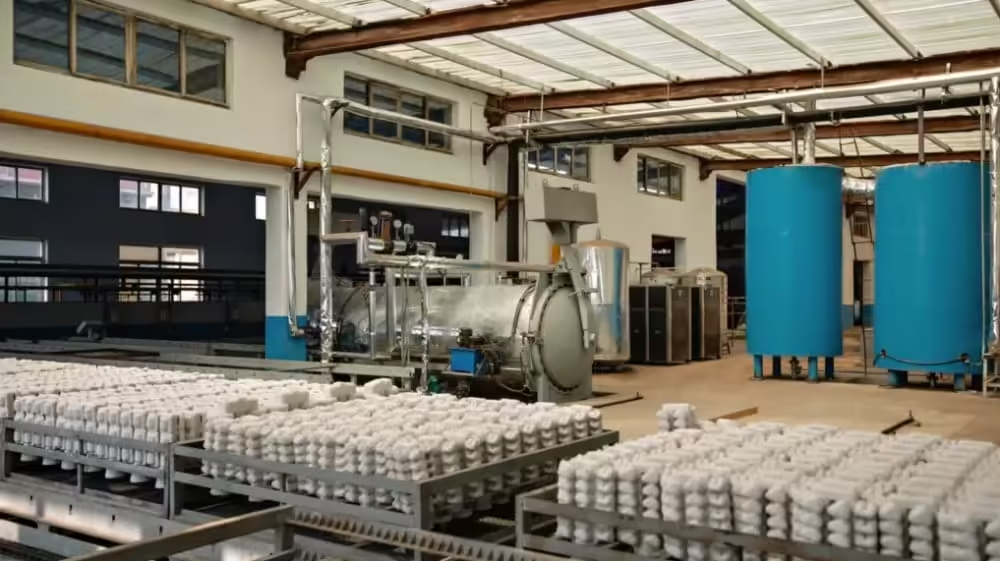
As industrial demands evolve and the need for more durable and efficient components increases, manufacturers are turning to refined production techniques. Among these, the impeller casting process has emerged as a superior method for creating precision-engineered components used in pumps, turbines, compressors, and other machinery. In 2025, this process continues to gain traction due to its ability to deliver high-performance parts with consistent quality.
The impeller, a rotating component of a pump or compressor, plays a crucial role in fluid dynamics. Its performance depends heavily on its geometry and structural integrity, making the production method especially significant. The casting process offers several advantages, including design flexibility, cost-effectiveness for complex shapes, and material versatility. With innovations in digital simulation, metallurgy, and automation, the impeller casting process is being adopted widely across sectors such as aerospace, automotive, energy, and industrial machinery.
How the Impeller Casting Process Works
Core Steps in the Impeller Casting Process
Impeller casting is a highly precise manufacturing process widely used in critical applications such as power generation, chemical processing, marine propulsion, and aerospace engineering. With the advancement of Industry 4.0 technologies in 2025, each step of the impeller casting process is now enhanced with automation, digital monitoring, and predictive analytics. The following are the detailed core steps involved:
1. Pattern creation
The process begins with the creation of a pattern, which is an exact replica of the impeller to be produced. Traditionally, materials like wax (used in investment casting) or foam (used in lost-foam casting) are employed to form this pattern. The pattern defines the geometry and surface finish of the final product.
In 2025, digital technologies such as 3D CAD modeling and rapid prototyping via 3D printing enable engineers to develop complex patterns with high dimensional accuracy. These advancements significantly reduce lead times and facilitate the manufacture of impellers with intricate internal structures, optimized for flow and efficiency.
2. Mold making
Once the pattern is completed, it is encased in a specialized mold material. For investment casting, the wax pattern is typically dipped multiple times in ceramic slurry to build a strong, heat-resistant shell. In sand casting, the pattern is pressed into fine-grain sand that has been chemically treated for strength.
The mold serves as the negative of the impeller, forming the exact shape into which the molten metal will be poured. In 2025, mold creation is supported by simulation software that predicts how the mold will respond to high temperatures and metal flow. This allows for proactive adjustments to prevent common casting defects such as porosity or misruns.
3. Melting and pouring
The selected alloy is melted in high-efficiency induction or arc furnaces. Temperature control is critical during this phase, as each metal has specific melting points and characteristics that must be preserved to maintain mechanical integrity.
Once the metal reaches the desired molten state, it is poured into the pre-heated mold cavity. Modern foundries now utilize robotic pouring systems and thermal cameras for real-time monitoring of temperature and pour rate. This level of automation minimizes human error, ensuring consistent casting quality and reducing material waste.
4. Cooling and solidification
After pouring, the molten metal begins to cool and solidify within the mold. The rate of cooling greatly affects the final grain structure and mechanical properties of the impeller. Controlled cooling is essential to avoid internal stresses, cracks, or warping.
Advanced casting setups in 2025 employ thermal sensors and cooling rate controllers, which dynamically adjust ambient conditions to maintain optimal solidification curves. This ensures that each casting achieves uniform hardness, strength, and dimensional stability, especially in complex, high-performance impeller designs.
5. Shakeout and cleaning
Once the casting has sufficiently cooled and solidified, the mold is broken apart to reveal the rough impeller. This process, known as shakeout, is followed by cleaning steps to remove residual mold material, oxides, and any excess metal from the gating system.
Modern facilities use automated sand removal systems, high-pressure water jets, and chemical cleaning solutions to ensure the impeller is free of contaminants. The cleaned impeller is then inspected for surface defects and prepared for finishing.
6. Finishing and inspection
The final stage involves machining, grinding, and polishing the impeller to meet precise tolerances and surface quality requirements. This may include drilling holes, refining vane edges, or balancing the component to reduce vibration in operation.
In 2025, CNC machining centers equipped with AI-based inspection systems ensure tight dimensional control. Non-destructive testing methods such as X-ray inspection, ultrasonic testing, and dye penetrant analysis are commonly used to detect any internal or surface flaws. These measures guarantee that the final impeller meets industry standards and performance specifications.
With these improvements, the entire casting process has become more efficient, repeatable, and capable of producing impellers with superior reliability and performance..
Key Materials Used in 2025
The choice of materials in the impeller casting process has expanded, allowing manufacturers to tailor components for specific environments:
- Stainless steel (for corrosion resistance)
- Inconel (for high-temperature applications)
- Bronze (for marine environments)
- Titanium alloys (for aerospace and medical applications)
Advancements in alloy development contribute to longer service life and improved mechanical performance.
Advantages of the Impeller Casting Process in 2025
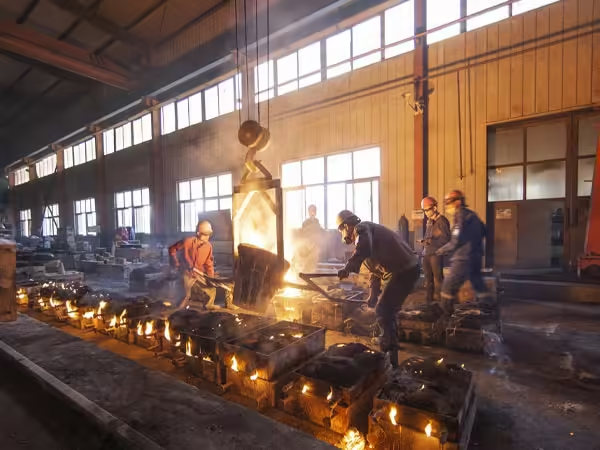
Enhanced Precision and Complexity
Modern casting techniques allow for intricate impeller geometries that were once impossible or cost-prohibitive. Improved simulation software predicts metal flow, shrinkage, and solidification, helping engineers optimize the design before production begins.
Cost-Effective for Mass Production
Casting is inherently suited for high-volume manufacturing. Once the mold is created, the same form can be used repeatedly, making it ideal for OEMs seeking consistent part quality at scale. Automation and additive manufacturing further reduce lead times and labor costs.
Improved Surface Finish and Mechanical Properties
With better mold materials and post-processing methods, cast impellers now offer superior surface finishes and tighter tolerances. Heat treatment and controlled cooling improve grain structure, enhancing the strength and fatigue resistance of the final product.
Sustainability and Material Efficiency
In 2025, sustainability is a priority across industries. The impeller casting process supports this trend by minimizing waste and allowing for the recycling of scrap metal. Closed-loop systems and energy-efficient furnaces further reduce the environmental footprint.
Comparative Table: Impeller Casting Process vs. Other Manufacturing Methods
ميزة | Impeller Casting Process | تصنيع الآلات باستخدام الحاسب الآلي | Forging |
---|---|---|---|
Complexity of Design | عالي | Medium | قليل |
Material Waste | قليل | عالي | Medium |
Setup Cost for Mass Production | قليل | عالي | Medium |
Surface Finish Quality | عالي | عالي | Medium |
Suitability for High Volume | ممتاز | Poor | جيد |
Time Efficiency | عالي | قليل | Medium |
Customization Flexibility | ممتاز | Medium | Poor |
Key Industries Using the Impeller Casting Process
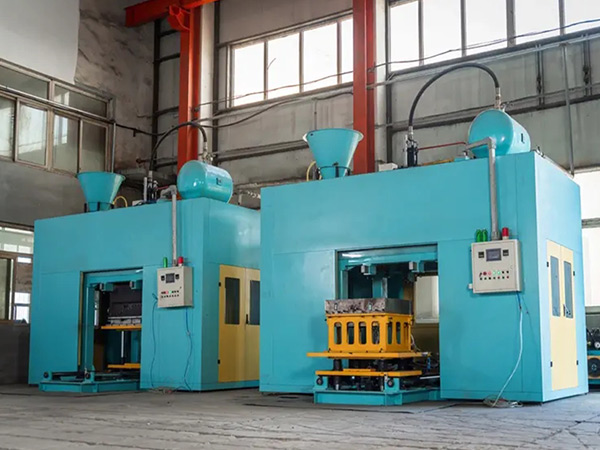
Aerospace
The aerospace sector demands parts that can withstand extreme stress and temperature changes. Cast impellers meet these requirements while allowing for complex aerodynamic profiles.
Energy and Power Generation
Impellers in turbines and compressors are central to energy production. The casting process provides the required durability and geometry while accommodating different energy outputs and operating environments.
Water Treatment and HVAC
Pump impellers used in HVAC systems, desalination plants, and water recycling facilities rely on casting for corrosion-resistant components capable of long-term service.
Automotive and Heavy Machinery
Engines and cooling systems in vehicles and industrial machines benefit from the uniformity and strength provided by cast impellers.
Future Outlook: Innovations in the Impeller Casting Process
As 2025 progresses, several trends are shaping the future of this manufacturing technique:
- Additive Casting Hybrids: Combining 3D printing with casting molds for faster prototyping.
- Smart Monitoring Systems: Sensors integrated into molds to capture temperature and flow data in real-time.
- Eco-Friendly Alloys: New material formulations that reduce emissions and improve recyclability.
- Digital Twins: Virtual models that mirror the actual casting process to optimize outcomes before physical production.
These innovations continue to reinforce the importance and relevance of the impeller casting process across industries.
خاتمة
ال impeller casting process is not just surviving in 2025—it is thriving. With its ability to handle complex designs, reduce waste, enhance durability, and support sustainability goals, it stands out as a premier choice for modern manufacturing. Its adoption across aerospace, automotive, and energy sectors highlights its adaptability and long-term value.
In a world where efficiency, precision, and sustainability matter more than ever, this process is at the heart of innovation. As industries evolve, the impeller casting process continues to deliver consistent performance, making it a cornerstone of component manufacturing.
الأسئلة الشائعة
What makes the impeller casting process better than machining?
Casting is more efficient for complex designs and high-volume production. It reduces material waste and offers more design flexibility than machining.
Are cast impellers durable?
Yes, especially when made from advanced alloys. They undergo heat treatment and rigorous testing to ensure durability in extreme conditions.
Is the process suitable for small-scale production?
While it’s ideal for large batches, modern techniques like rapid mold-making allow it to be cost-effective for smaller runs too.
What industries benefit most from this method?
Aerospace, energy, HVAC, automotive, and water treatment sectors all utilize this process for its precision and reliability.
How has technology improved this process in 2025?
Technological advances like real-time monitoring, digital simulations, and hybrid manufacturing methods have enhanced quality, reduced costs, and shortened production times.
فئات المنتجات
- أجزاء الصمامات
- أجزاء مضخة المياه
- أجزاء صندوق المحمل
- أجزاء الصب بالقالب
- منتجات مضخات الفولاذ المقاوم للصدأ
- منتجات مضخات الحديد الزهر
- قطع غيار الصمامات لاستخدام السيارات
- قطع غيار السيارات
- أجزاء الصمامات للاستخدام المدني
- قطع غيار مضخة التفريغ KF
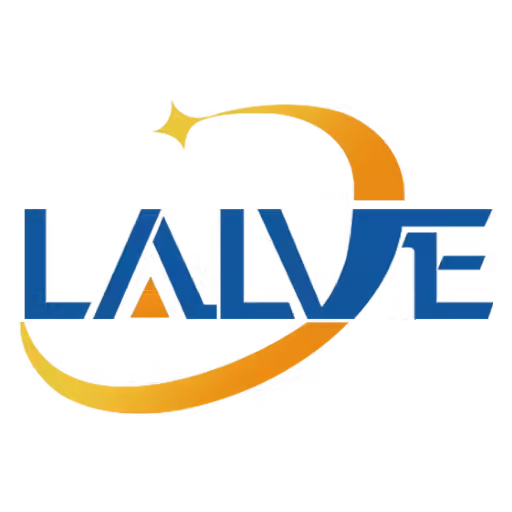