كيفية تغيير المكره: 5 خطوات سهلة لتحسين الكفاءة
مرحباً بكم في مدونتي!
I’m thrilled to have you here! Before we dive into the content, I’d love for you to join me on my social media platforms. It’s where I share extra insights, connect with our amazing community, and keep you updated on the latest news. Here’s how you can stay connected:
📘 Facebook: Shanghai Leierwo Industry Trade Co., Ltd.
Now, let’s embark on this journey together! I hope you find the content here not only insightful but also inspiring and valuable. Let’s get started!
جدول المحتويات
مقدمة
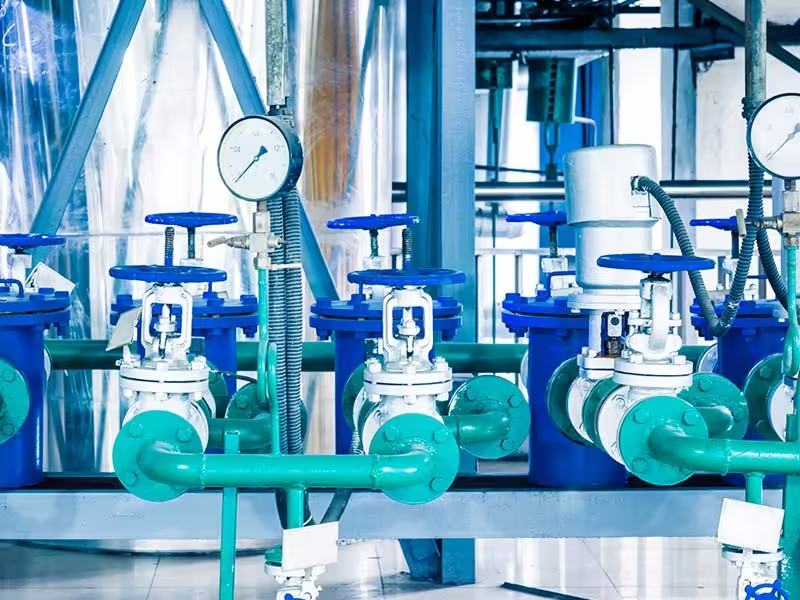
ال impeller is a crucial part of many mechanical systems, especially in pumps, motors, and turbines. It plays a significant role in transferring energy to the fluid it moves, which is why the efficiency of your system heavily depends on its condition. Over time, impellers can wear out, reducing the overall efficiency of your system. So, knowing how to change impeller parts properly can be key to maintaining smooth operation.
In this article, we will guide you through the steps for changing an impeller, explain why it’s necessary, and provide tips for ensuring a smooth replacement. By following these steps, you’ll improve the efficiency of your system and avoid performance issues down the road.
Why You Need to Change Impeller Regularly
Before diving into the steps for changing the impeller, it’s important to understand why this maintenance task is essential. The impeller’s function is to move fluid or gas by creating rotational energy, which is essential for the performance of many machines. Over time, the impeller can experience damage, wear, or corrosion, leading to reduced efficiency and possible damage to the entire system.
Here are some key reasons why you should change impeller components:
- Wear and Tear: Continuous use can erode the impeller, especially in environments with high pressure, temperature, or corrosive substances.
- Performance Decrease: A worn-out impeller will struggle to move fluid efficiently, leading to poor system performance.
- Prevent Further Damage: Delaying the change can cause other parts of the system to suffer from the reduced efficiency or even break down.
Step 1: Prepare for Impeller Replacement
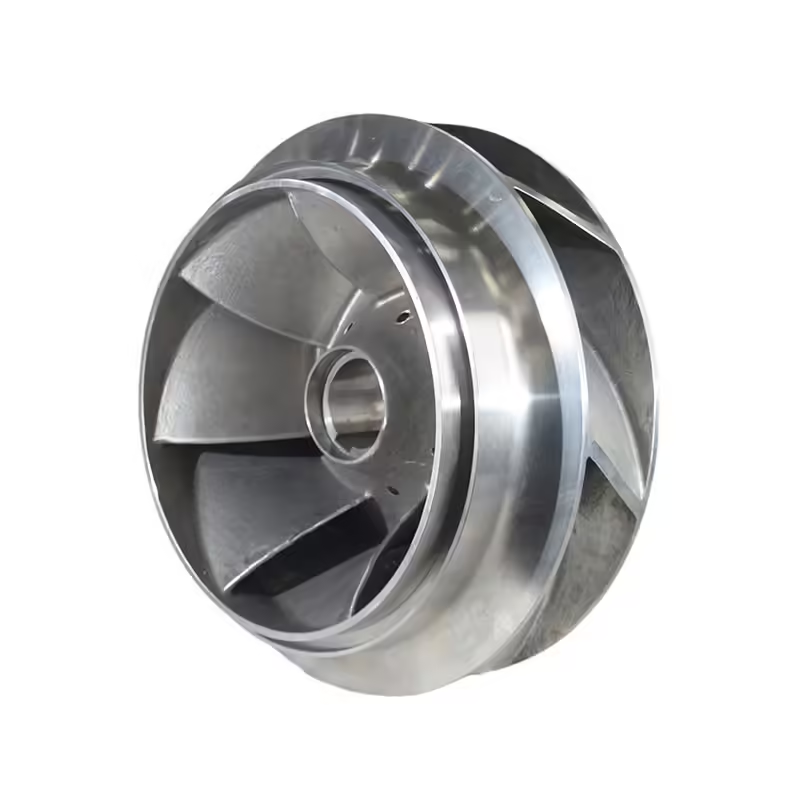
Before starting the process of how to change impeller parts, the first step is preparation. Proper preparation ensures a safe, efficient, and smooth process. Here’s what you need to do:
- Turn Off Power: Ensure the system is completely powered off and disconnected from any electrical sources.
- Gather Tools: Depending on the impeller type and the system, you will need a set of tools like wrenches, screwdrivers, and a puller.
- Safety Gear: Wear gloves, goggles, and protective clothing to avoid any injuries while handling sharp parts or hazardous materials.
- Check the Manufacturer’s Manual: Always consult the manufacturer’s instructions for specific guidelines about your impeller replacement.
By following this preparatory step, you’ll avoid unnecessary issues during the impeller replacement process.
Step 2: Remove the Old Impeller
The next step in learning how to change impeller parts is removing the old impeller. This step is crucial, as improper removal can damage other components or hinder the installation of the new impeller. Here’s how you can proceed:
- Remove Fasteners and Bolts: Carefully remove any screws, bolts, or fasteners that are holding the impeller in place.
- Use a Puller: If the impeller is tightly fixed, use an impeller puller to safely remove it from the shaft.
- Inspect the Shaft: Once the impeller is removed, inspect the shaft for any signs of wear, corrosion, or damage.
It is essential to handle the impeller carefully during removal to avoid causing any damage that could affect the new impeller or surrounding components.
Step 3: Install the New Impeller
Once you’ve successfully removed the old impeller, it’s time to install the new one. The installation process is critical, as any misalignment or improper fitting can affect system performance. Follow these steps to ensure proper installation:
- Align the Impeller: Place the new impeller onto the shaft, ensuring it is aligned correctly with the system’s specifications.
- Secure the Impeller: Use the necessary bolts and fasteners to secure the impeller tightly in place. Make sure the impeller is seated correctly.
- Check for Proper Rotation: Before closing up the system, manually rotate the impeller to check if it moves freely and smoothly.
If done correctly, the new impeller should be securely installed and ready to perform efficiently.
Step 4: Reassemble the System
Once the new impeller is in place, you will need to reassemble the system. This step involves ensuring that everything is put back together without damaging any parts or causing leaks. Here’s how you can reassemble the system:
- Reattach All Components: Ensure all bolts, nuts, and screws are tightened properly.
- Check Seals: Inspect seals or gaskets to ensure they’re in good condition and properly positioned.
- Reinstall Protective Covers: If your system has protective covers or panels, reinstall them to secure the impeller and prevent any external interference.
After reassembling, verify that the impeller is securely in place before proceeding to the next step.
Step 5: Test the System
Finally, the last step in how to change impeller parts involves testing the system. This step is critical to ensure that the impeller is functioning properly and the system is operating at peak efficiency. Here’s what you should do:
- Power On the System: Turn the power back on and observe the system’s operation.
- Check for Leaks: Look for any potential leaks or unusual sounds that could indicate improper installation.
- Monitor Performance: Ensure that the system is operating efficiently and that the new impeller is moving the fluid effectively.
If everything checks out, you’ve successfully replaced your impeller!
Table: Impeller Replacement Checklist
Step | Action | Notes |
---|---|---|
1. Prepare | Gather tools, disconnect power, and wear safety gear | Follow the manufacturer’s instructions |
2. Remove Old Impeller | Use a puller, inspect shaft for damage | Handle carefully to avoid damage |
3. Install New Impeller | Align, secure, and check rotation | Ensure proper fitting and alignment |
4. Reassemble | Tighten components, check seals | Reinstall covers to secure impeller |
5. Test System | Power on and check for leaks or issues | Monitor system performance |
When to Change المكرهة: Signs That It’s Time for a Replacement
Knowing when to change impeller components is just as crucial as understanding how to change impeller parts. Impellers are critical to the efficient operation of many machines, so recognizing the signs of wear and tear early on can prevent more severe damage and costly repairs. Here are some key indicators that it’s time to change impeller components:
1. Decreased Performance
One of the most common signs that it’s time to change impeller components is a noticeable drop in the system’s performance. If your pump, motor, or turbine isn’t moving fluid as efficiently as it should, it might be time to change the impeller. A deteriorated impeller struggles to move fluid at the necessary rate, leading to a reduction in the system’s overall efficiency. When you change impeller parts, the system will regain its optimal performance.
2. Unusual Noise or Vibration
If your system begins making unusual noises or vibrations, it could indicate an issue with the impeller. A damaged impeller may become unbalanced or loose, causing irregular movement. If left unchecked, this can lead to more severe issues, such as bearing failure or excessive wear on other parts of the system. In such cases, it’s essential to change the impeller to prevent further damage and restore balance.
3. Visible Damage or Wear
Inspecting the impeller for visible damage is one of the best ways to tell if it needs to be replaced. Over time, the impeller’s blades can wear down, crack, or become corroded, especially in systems operating under harsh conditions. If you notice any significant damage to the blades or housing, it’s time to change the impeller. Changing the impeller ensures that the system continues to function at full capacity.
4. Increased Energy Consumption
A malfunctioning or inefficient impeller can cause the system to work harder to achieve the same output. If you notice a sudden increase in energy consumption, the impeller could be the culprit. This is often due to excessive friction or improper rotation, both of which can decrease system efficiency. Changing the impeller will reduce energy consumption and improve overall system performance.
5. Imbalance or Cavitation Issues
Cavitation is a phenomenon where air bubbles form and collapse inside the system, often due to improper impeller function. This causes a loss in system efficiency and can damage internal parts. If your system is experiencing cavitation, it may be due to an impeller that is no longer functioning as it should, making it necessary to change the impeller. Changing the impeller can eliminate cavitation and improve system operation.
6. Frequent Maintenance and Repair Needs
If you find yourself frequently repairing or maintaining the impeller, it might be a sign that it’s approaching the end of its service life. A constantly failing impeller can lead to more frequent downtime and costly repairs. Replacing the impeller proactively can prevent further issues and keep your system running smoothly. When you change the impeller at the right time, you can significantly reduce maintenance costs and downtime.
خاتمة
Knowing how to change impeller parts is essential for maintaining the efficiency of many industrial systems. Understanding the steps to change impeller components can make a significant difference in the long-term functionality of your machinery. By following the five easy steps outlined in this article, you can ensure that your system runs smoothly, efficiently, and reliably. Regularly learning how to change impeller parts helps prevent system failure, reduces downtime, and keeps your operations running at optimal performance. Remember, knowing when to change impeller parts is just as important as the process itself.
Always remember to consult your system’s manual and follow proper safety protocols during the replacement process. When it comes to maintaining the performance of your equipment, knowing how to change impeller components correctly is vital for ensuring longevity and preventing unnecessary repairs.
الأسئلة الشائعة
What is the lifespan of an impeller?
The lifespan of an impeller can vary depending on the material, the system’s operating conditions, and how well it’s maintained. Typically, impellers last anywhere from 2 to 5 years before they need replacing.
Can I change the impeller myself?
Yes, changing an impeller can be done by following the proper steps, ensuring safety, and using the correct tools. However, if you’re unsure or working with complex systems, it’s recommended to consult a professional.
How do I know when to change the impeller?
Signs that your impeller needs changing include reduced system performance, unusual noises, vibrations, or visible wear on the impeller blades.
فئات المنتجات
- أجزاء الصمامات
- أجزاء مضخة المياه
- أجزاء صندوق المحمل
- أجزاء الصب بالقالب
- منتجات مضخات الفولاذ المقاوم للصدأ
- منتجات مضخات الحديد الزهر
- قطع غيار الصمامات لاستخدام السيارات
- قطع غيار السيارات
- أجزاء الصمامات للاستخدام المدني
- قطع غيار مضخة التفريغ KF
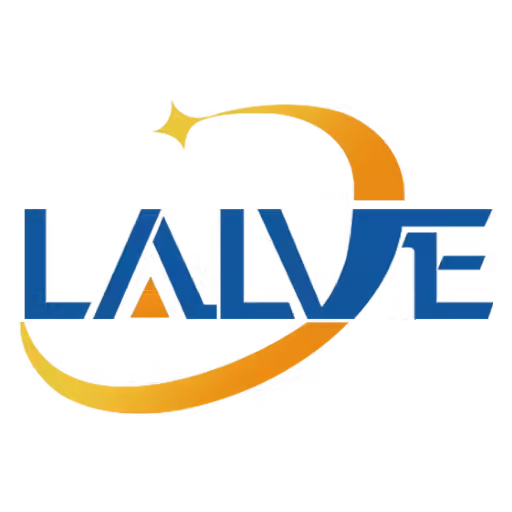