ثلاثة مخاطر خفية في مراوح مضخات الحديد الزهر
مرحباً بكم في مدونتي!
I’m thrilled to have you here! Before we dive into the content, I’d love for you to join me on my social media platforms. It’s where I share extra insights, connect with our amazing community, and keep you updated on the latest news. Here’s how you can stay connected:
📘 Facebook: Shanghai Leierwo Industry Trade Co., Ltd.
Now, let’s embark on this journey together! I hope you find the content here not only insightful but also inspiring and valuable. Let’s get started!
جدول المحتويات
مقدمة
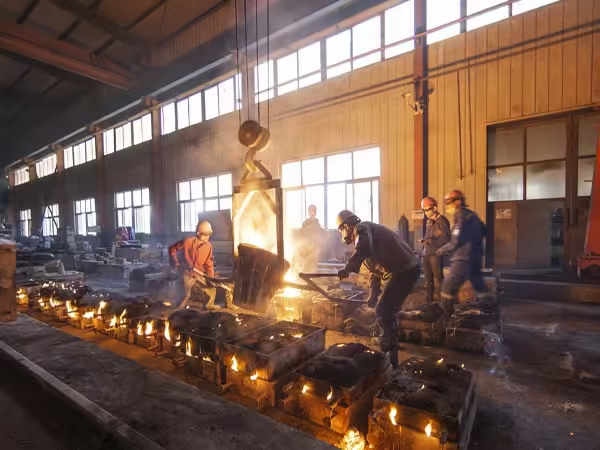
Cast iron pump impellers play a crucial role in many fluid-handling systems across industries such as agriculture, wastewater treatment, and chemical processing. Known for their durability and cost-effectiveness, these components are frequently chosen for pumps where rugged performance is required. Despite their many advantages, relying solely on cast iron pump impellers can expose operations to unexpected problems. This article uncovers three hidden dangers associated with cast iron pump impellers, exploring how they might impact performance, safety, and long-term operational costs.
Understanding these risks is essential for engineers, technicians, and maintenance teams aiming to maximize the efficiency and lifespan of pumping equipment. By recognizing the vulnerabilities of the cast iron pump impeller, stakeholders can implement proactive strategies to mitigate failures and maintain smooth operations.
The Corrosion Conundrum in Cast Iron Pump Impellers
One of the most significant yet often underestimated dangers is corrosion. While cast iron provides excellent mechanical strength, it is inherently prone to oxidation and rusting when exposed to moisture, chemicals, or acidic fluids. This corrosion process can rapidly degrade the surface and structural integrity of the impeller.
Pumps used in harsh environments or handling aggressive liquids may suffer accelerated wear, reducing their overall lifespan. Corrosion not only affects the appearance of the cast iron pump impeller but also diminishes its hydraulic performance, leading to reduced flow rates and energy efficiency. Moreover, if left unchecked, corrosion can cause catastrophic failure, necessitating costly replacements and unplanned downtime.
Types of Corrosion Commonly Found
- Uniform corrosion: Even surface rusting due to consistent fluid exposure.
- Pitting corrosion: Localized and intense corrosion forming cavities.
- Galvanic corrosion: Caused by contact with dissimilar metals in the pump housing.
Proper material coatings, improved fluid chemistry, and routine inspections can help mitigate these risks.
Mechanical Wear and Erosion Challenges
Mechanical wear and erosion represent another hidden danger in cast iron pump impellers, especially in applications that involve the transport of abrasive or particle-laden fluids. These forces can compromise not just the surface finish of the impeller but also its critical dimensions, leading to a progressive decline in pump efficiency and reliability.
When abrasive particles such as sand, gravel, or slurry pass through the pump at high velocity, they act like tiny projectiles that repeatedly strike the impeller’s surface. This results in the gradual removal of material, particularly at the vane tips and edges where flow velocity is the highest. Over time, this erosion can lead to significant dimensional changes in the impeller, affecting the hydraulic balance and impeding fluid flow.
Furthermore, the roughened surfaces caused by erosion increase turbulence, which can exacerbate cavitation—a phenomenon where vapor bubbles form and collapse inside the pump. Cavitation not only accelerates wear but can also lead to pitting damage, worsening the structural condition of the impeller.
Key Indicators of Mechanical Wear
- Thinning of vane edges: As material wears away, the vanes become thinner, reducing their strength and ability to impart energy to the fluid.
- Surface roughness: The formerly smooth surfaces develop pitting, scratches, and uneven wear patterns, increasing flow resistance.
- Reduced pump head and pressure: A clear sign that the impeller can no longer move the fluid with the same force due to loss of geometry.
- Irregular flow patterns: Variability in output pressure or pulsating flows may indicate imbalance or hydraulic inefficiency.
- Increased operating noise: High-pitched whines or rattling sounds can suggest uneven wear or distorted impeller alignment.
To combat these issues, maintenance teams should conduct regular particle size and concentration analysis to assess the abrasiveness of the fluid. When high levels of particulates are detected, the use of wear-resistant coatings—such as tungsten carbide or ceramic linings—can be beneficial. In more extreme conditions, switching to impellers made from harder materials like stainless steel or duplex alloys may be necessary.
Best Practices to Minimize Mechanical Wear
- Install filters or strainers upstream to remove large abrasive particles.
- Optimize pump speed and flow rates to reduce fluid velocity and minimize impact forces.
- Use erosion-resistant coatings or hardfacing materials on impeller surfaces.
- Design impellers with thicker vane profiles for high-abrasion scenarios.
- Monitor vibration and alignment regularly to prevent additional mechanical stress.
By proactively managing erosion and mechanical wear, operators can maintain the efficiency and extend the service life of cast iron pump impellers, especially in demanding industrial settings.
Brittle Fracture Under Extreme Conditions
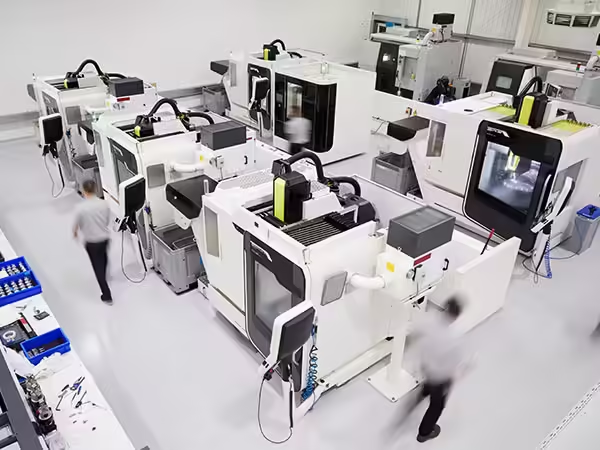
Though cast iron is known for its compressive strength, it exhibits brittleness under tensile stress or impact. This means the cast iron pump impeller is vulnerable to cracking or sudden fracture if subjected to sudden pressure changes, mechanical shock, or improper installation.
In cold climates, thermal contraction can exacerbate the problem, increasing the likelihood of fractures during startup or shutdown cycles. A brittle fracture can halt operations entirely and may even pose safety risks to personnel, particularly in high-pressure systems. Proper material selection and design review are critical for mitigating this risk.
Common Scenarios Leading to Fracture:
- Freezing fluid within the pump housing
- Rapid start-stop cycles
- Sudden valve closures causing water hammer
- Improperly aligned motor couplings
Table: Comparative Analysis of Pump Impeller Materials
Property | الحديد الزهر | Bronze | الفولاذ المقاوم للصدأ | Engineering Plastic |
---|---|---|---|---|
مقاومة التآكل | Poor to Moderate | جيد | ممتاز | ممتاز |
Abrasion Resistance | معتدل | معتدل | جيد | Low to Moderate |
Strength | High (compressive) | معتدل | عالي | معتدل |
Brittleness | عالي | قليل | قليل | Very Low |
Cost | قليل | معتدل | عالي | Low to Moderate |
التطبيقات الشائعة | Wastewater, agriculture | Marine, oil | Chemicals, food processing | Light-duty, corrosive fluids |
The above table offers a comparative view of different materials commonly used in pump impellers, highlighting both the advantages and limitations of the cast iron pump impeller relative to alternatives.
Detecting Early Signs of Failure in Cast Iron Pump Impellers
Preventive maintenance plays a crucial role in extending the service life of cast iron pump impellers. Catching signs of deterioration early can help prevent catastrophic failure and reduce repair costs. Here are several key early indicators that should not be overlooked:
- Unusual noises: A rattling, grinding, or whining sound coming from the pump often indicates an imbalance, misalignment, or wear in the impeller. These noises may worsen over time and should be investigated immediately.
- Reduced flow rate: A noticeable drop in pump performance, such as slower fluid movement or decreased pressure, can signal erosion, corrosion, or deformation of the impeller blades.
- Visible cracks or rust spots: Surface imperfections, particularly around blade roots or mounting points, may be precursors to deeper fractures. Rust can spread quickly in moist environments, weakening the structure.
- Increased vibration: Abnormal vibrations are frequently caused by asymmetrical wear, buildup of solids, or internal cracks. Persistent vibration not only damages the pump but can also affect connected equipment.
- Frequent maintenance cycles: If a pump requires increasingly frequent repairs or inspections, the impeller may be degrading more rapidly than expected due to cumulative damage.
To enhance early detection, maintenance teams should adopt the following diagnostic practices:
- Regular visual inspections using endoscopes or disassembly
- Vibration analysis to track amplitude and frequency shifts
- Ultrasonic testing to detect internal flaws
- Fluid sampling to evaluate chemical aggressiveness or particulate content
Implementing a proactive condition-monitoring program allows plant operators to plan timely repairs or replacements, thereby minimizing downtime and maximizing equipment longevity.
Alternative Materials and Their Impact on Performance
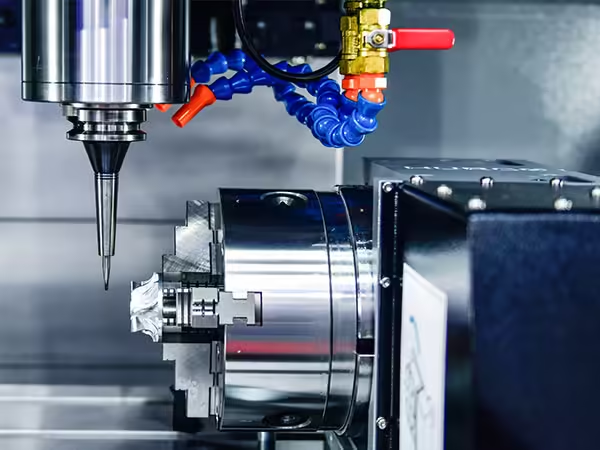
For operations experiencing frequent failures or maintenance challenges, switching to an alternative impeller material could offer improved reliability. Stainless steel impellers provide superior corrosion and wear resistance, while bronze offers better ductility and lower brittleness. In less demanding environments, high-performance plastics may deliver corrosion resistance at a lower weight and cost.
However, material changes should be made with a clear understanding of the application, fluid characteristics, and operating conditions. Each material has trade-offs that must be considered alongside performance expectations and budget constraints.
Questions to Ask Before Switching Materials
- What is the total cost of ownership over the pump’s lifecycle?
- What is the chemical composition of the fluid being pumped?
- Are there solid particles present in the fluid?
- Is the operating temperature or pressure extreme?
- How often is maintenance currently required?
خاتمة
While cast iron pump impellers remain a popular choice for many applications due to their affordability and strength, they are not without their hidden dangers. Corrosion, mechanical wear, and brittleness can compromise pump performance and increase operational costs if not properly managed.
By identifying these risks and adopting proactive strategies such as material evaluation, scheduled maintenance, and regular inspections, operators can mitigate failures and ensure long-term system reliability. For those dealing with frequent breakdowns, exploring alternative impeller materials may lead to significant performance improvements.
Ultimately, understanding the limits of the cast iron pump impeller is key to making informed decisions in pump system design and maintenance.
الأسئلة الشائعة
How often should a مروحة مضخة من الحديد الزهر be inspected?
Inspection frequency depends on the application, but a quarterly inspection is recommended in demanding environments.
Can a مروحة مضخة من الحديد الزهر be repaired if damaged?
Minor surface damage can sometimes be repaired, but extensive corrosion or cracks usually require replacement.
What fluids are most damaging to cast iron pump impellers?
Acidic, alkaline, or abrasive fluids can severely shorten the life of a cast iron pump impeller.
Are coatings effective in protecting cast iron impellers?
Yes, certain protective coatings can improve corrosion resistance but may not prevent mechanical wear.
When should I consider switching to a different impeller material?
If your system frequently experiences impeller failures or increased maintenance costs, alternative materials like stainless steel may offer better longevity.
فئات المنتجات
- أجزاء الصمامات
- أجزاء مضخة المياه
- أجزاء صندوق المحمل
- أجزاء الصب بالقالب
- منتجات مضخات الفولاذ المقاوم للصدأ
- منتجات مضخات الحديد الزهر
- قطع غيار الصمامات لاستخدام السيارات
- قطع غيار السيارات
- أجزاء الصمامات للاستخدام المدني
- قطع غيار مضخة التفريغ KF
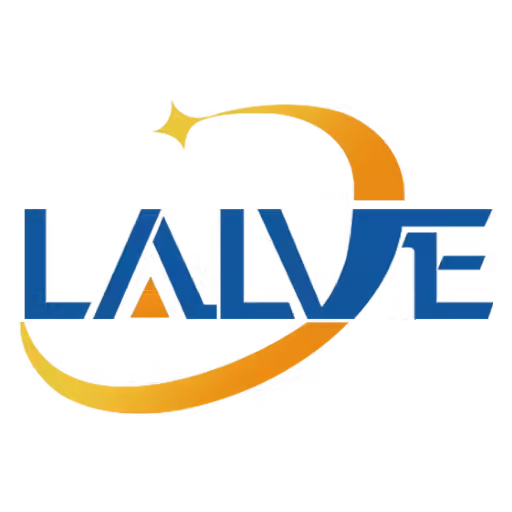