10 علامات حرجة تشير إلى وجود مصنع سيء لمضخات الصب
مرحباً بكم في مدونتي!
I’m thrilled to have you here! Before we dive into the content, I’d love for you to join me on my social media platforms. It’s where I share extra insights, connect with our amazing community, and keep you updated on the latest news. Here’s how you can stay connected:
📘 Facebook: Shanghai Leierwo Industry Trade Co., Ltd.
Now, let’s embark on this journey together! I hope you find the content here not only insightful but also inspiring and valuable. Let’s get started!
جدول المحتويات
مقدمة
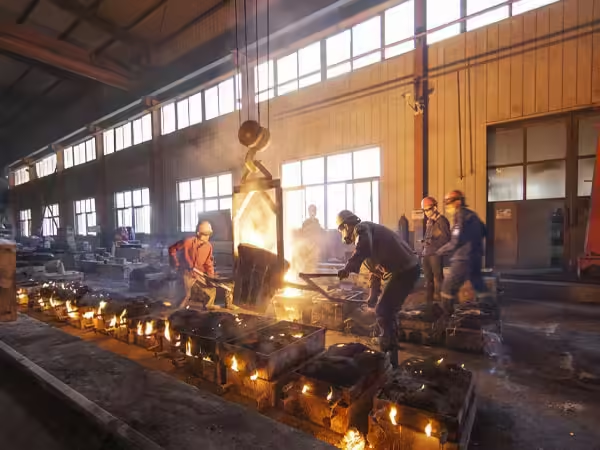
When it comes to industries relying heavily on fluid movement—such as water treatment, chemical processing, and power generation—cast impellers are among the most crucial components. These parts are integral in ensuring that pumps and turbines operate efficiently. The performance of cast impellers, however, is directly influenced by the manufacturing standards of the factory where they are made.
Selecting the right cast impeller factory is not just about choosing a supplier, but about ensuring that the impellers produced meet stringent quality standards and can perform reliably over the long term. The wrong factory can lead to disastrous consequences, ranging from frequent breakdowns to costly repairs. Therefore, it’s vital for businesses to identify and avoid factories that are prone to making critical errors in manufacturing.
NO 1. Absence of Industry Certifications
Industry certifications are a clear indicator that a cast impeller factory adheres to internationally recognized standards and regulatory requirements. The absence of such certifications often signals that the factory does not meet the basic expectations for product quality and safety. These certifications—such as ISO 9001 or specific industry-related standards—serve as proof that the cast impeller factory’s processes are thoroughly tested and validated by independent bodies.
If a cast impeller factory does not hold these certifications or is unwilling to disclose them, it raises a red flag. Such factories might bypass key safety checks, overlook quality control measures, or ignore guidelines for producing impellers that can withstand the operational stresses they will encounter. Without these certifications, the cast impeller factory’s impellers are far more likely to fail under real-world conditions, jeopardizing the smooth operation of critical systems.
For any company that values quality assurance, choosing a certified cast impeller factory is non-negotiable. Without these certifications, you may end up with substandard products that do not meet the required specifications or safety standards.
NO 2. Variability in Product Quality
One of the hallmarks of a reliable cast impeller factory is the ability to produce consistent, high-quality products over time. Impellers must meet precise specifications regarding dimensions, materials, and surface finish. Even minor variations in these parameters can cause major operational issues. If a cast impeller factory produces impellers with noticeable variations from batch to batch, it is a clear sign of subpar manufacturing practices.
Inconsistent product quality can manifest in several ways: incorrect sizes, uneven weight distribution, or even visible defects such as cracks or surface imperfections. These discrepancies can directly affect the efficiency of pumps, leading to unbalanced operation, increased wear and tear, and the potential for catastrophic system failure. Impellers that are not up to standard may also result in additional maintenance costs, as they may need to be replaced more frequently than properly manufactured counterparts.
To ensure operational reliability, it is essential to partner with a factory that has stringent quality control measures in place. This includes regular inspections, performance testing, and a system to track and correct any deviations in product quality. Only through consistent, high-quality production can businesses guarantee that their impellers will perform as expected throughout their lifecycle.
NO 3. Lack of Transparency and Poor Communication
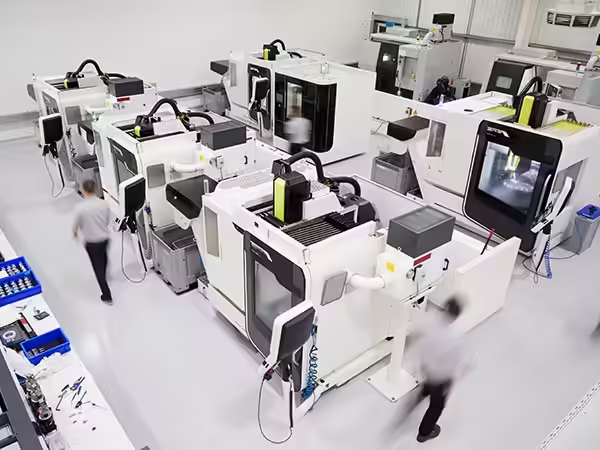
Communication between manufacturers and clients is key to establishing a successful partnership. A reliable cast impeller factory should be transparent about its production processes, delivery timelines, and any potential issues. If the factory is difficult to reach, avoids questions, or provides unclear answers, it can be a warning sign of deeper operational issues.
Inadequate communication often reflects poor management or a lack of organization within the factory. If the factory fails to clearly outline their production capabilities, timelines, and possible challenges, it indicates that they may be hiding critical information about their operations. This lack of transparency can lead to delays in production, difficulties with post-purchase support, and even unexpected issues with product quality.
A good cast impeller factory should be open and honest with its clients. If they are unwilling to provide detailed information about their production timelines, capabilities, or quality control procedures, it is wise to reconsider doing business with them. Clear, effective communication is vital for ensuring that you receive the products you need, when you need them, and that any concerns are addressed promptly.
NO 4. Limited Customization Capabilities
Customization is essential in industries that require impellers to meet specific, often complex operational demands. Every system has its unique needs, and impellers must be tailored to suit those requirements—whether it’s adjusting material types to withstand certain chemicals, optimizing design to improve performance in particular conditions, or customizing dimensions for different pump models.
If a factory cannot provide customized solutions or lacks the technical expertise to modify designs based on your specifications, it could be an indication that they lack the necessary resources or experience to meet higher industry standards. This limitation can result in purchasing off-the-shelf products that don’t fit your system’s needs, potentially leading to inefficiencies, equipment failure, or excessive maintenance costs.
A reliable cast impeller factory should have the capability to offer tailored solutions, whether through design modifications, specialized material selection, or bespoke manufacturing processes. This flexibility ensures that your impellers will perform optimally in your specific application.
NO 5. Inadequate Testing and Inspection Procedures
Testing and inspection are crucial components of the manufacturing process for cast impellers. Before any product leaves the factory, it should undergo comprehensive testing to verify its integrity, performance, and compliance with required specifications. If a cast impeller factory lacks these procedures or does not conduct thorough testing on their impellers, it opens the door to potential defects and product failures.
Tests such as material strength assessments, dimensional accuracy checks, and surface integrity evaluations are vital to ensuring that the impellers can withstand the harsh conditions they will face during operation. Without these tests, you might end up with impellers that have hidden flaws, such as cracks, insufficient strength, or subpar performance, which can compromise the entire system they are part of.
A reputable cast impeller factory should employ rigorous inspection and testing protocols, and they should be transparent about the methods they use. If a cast impeller factory does not regularly test their products or refuses to provide test reports, it’s best to seek a more trustworthy supplier.
Table: Key Indicators of a Substandard Cast Impeller Factory
Indicator | Implications |
---|---|
No industry certifications | Lack of adherence to global manufacturing standards |
Inconsistent product quality | Potential performance issues, unbalanced operation |
Poor communication | Increased risk of delays and misunderstandings |
Limited customization options | Risk of purchasing unsuitable impellers |
Insufficient testing procedures | Higher likelihood of undetected defects and failures |
NO 6. Frequent Delivery Delays
Timely delivery is crucial for keeping operations running smoothly and avoiding disruptions. If a factory consistently fails to meet delivery deadlines, it indicates poor management, inadequate capacity, or supply chain issues. These delays can set back critical projects and increase costs, especially if they result in equipment downtimes or missed deadlines in larger projects.
The causes of delivery delays can be traced back to various factors: inefficient manufacturing processes, problems with raw material procurement, or poorly managed production schedules. Regardless of the reason, frequent delays are a significant sign that the factory is not equipped to handle your needs reliably.
A good cast impeller factory should provide realistic delivery estimates and stick to them. They should have contingency plans in place to handle unforeseen delays and keep their clients informed of any potential setbacks in a timely manner.
NO 7. Outdated Manufacturing Facilities
Manufacturing technology plays a vital role in the quality of the end product. A factory that relies on outdated or obsolete equipment may struggle to maintain consistent quality, resulting in impellers with dimensional inaccuracies, poor surface finishes, or inferior mechanical properties.
Modern manufacturing processes, such as advanced casting technologies, CNC machining, and precision testing equipment, ensure that the impellers are made to the highest standards. Factories that fail to invest in upgrading their facilities may not be able to keep up with evolving industry standards or meet the performance requirements of their clients.
When selecting a cast impeller factory, assess the condition of their equipment and their willingness to adopt new technologies. This will give you an indication of their commitment to quality and their ability to produce impellers that meet modern demands.
NO 8. Negative Customer Feedback
Customer feedback provides valuable insight into the performance and reliability of a cast impeller factory. A pattern of negative reviews or complaints about product quality, poor service, or missed deadlines should not be ignored. Consistently poor customer experiences indicate systemic problems that are unlikely to improve without significant changes to the factory’s operations.
While some isolated complaints may be expected in any business, a factory with a history of negative feedback should be scrutinized carefully. If the majority of reviews point to issues such as product failures, poor communication, or unmet expectations, it may be a sign that the factory is not capable of delivering the quality and service you need.
Before committing to a supplier, take the time to research customer reviews and ratings. Look for patterns in feedback and consider whether the factory has made efforts to address past problems. If customer satisfaction is low, it’s a red flag.
NO 9. Absence of After-Sales Support
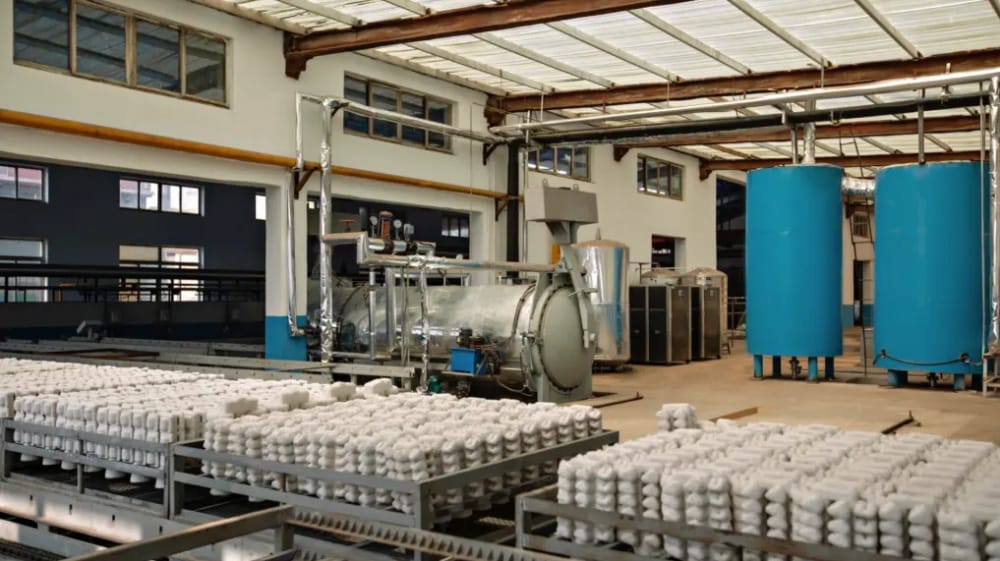
After-sales support is essential for ensuring that the impellers function properly over time and that any issues encountered after delivery are promptly addressed. A cast impeller factory that does not provide reliable after-sales services, such as technical support, installation advice, or warranty coverage, may leave clients stranded when issues arise.
Lack of after-sales support increases the risk of prolonged downtimes if problems are encountered, leading to higher costs and operational inefficiencies. A factory that offers comprehensive support services can help mitigate these risks and provide guidance on product usage, maintenance, and troubleshooting.
When selecting a factory, ensure that they offer clear and accessible after-sales support. This will help ensure that you have the resources you need to maintain operational efficiency over the life of the impellers.
NO 10. Refusal to Provide Sample Products
A trustworthy cast impeller factory should be willing to provide sample products for testing and evaluation before committing to a large order. Samples allow businesses to assess the quality, performance, and fit of the impellers in their systems. If a factory refuses to provide samples or imposes unreasonable conditions for their provision, it could be a sign that they are hiding potential defects or weaknesses in their products.
Samples are an essential part of the decision-making process, as they allow for hands-on evaluation of the product’s suitability for your needs. If a factory is unwilling to provide samples or has strict limitations on sample availability, it’s a major warning sign that they may not be a reliable supplier.
خاتمة
Selecting the right cast impeller factory is a critical decision that can have long-term implications for the success of your operations. By identifying the critical signs of a bad factory—such as lack of certifications, inconsistent product quality, poor communication, and inadequate testing procedures—you can avoid costly mistakes and ensure that you are working with a reliable and capable supplier.
Prioritize factories that demonstrate transparency, offer robust customer support, and consistently meet high-quality standards. By taking the time to thoroughly assess potential suppliers, you can ensure that your cast impellers perform as expected, keeping your systems running smoothly and minimizing the risk of costly failures.
الأسئلة الشائعة
Why are industry certifications important when selecting a cast impeller factory?
Certifications ensure that the factory adheres to internationally recognized standards for quality, safety, and environmental impact. They provide assurance that the factory’s processes are validated and meet specific performance criteria.
How can I assess the quality of impellers before placing a large order?
Requesting samples allows you to test the product for fit, performance, and material quality. This step is essential for ensuring the impellers meet your exact specifications.
What role does after-sales support play in the selection of a factory?
After-sales support ensures that any issues with the impellers can be addressed promptly, reducing downtime and maintenance costs. It is essential for long-term operational efficiency.
How do outdated manufacturing facilities impact impeller quality?
Outdated facilities often lack the precision required to produce high-quality impellers. This can lead to defects, dimensional inaccuracies, and subpar performance.
What are the risks of engaging with a factory that has negative customer feedback?
Negative feedback often points to recurring issues with quality, service, or reliability. Engaging with such a factory increases the risk of receiving faulty products or experiencing poor customer service.
فئات المنتجات
- أجزاء الصمامات
- أجزاء مضخة المياه
- أجزاء صندوق المحمل
- أجزاء الصب بالقالب
- منتجات مضخات الفولاذ المقاوم للصدأ
- منتجات مضخات الحديد الزهر
- قطع غيار الصمامات لاستخدام السيارات
- قطع غيار السيارات
- أجزاء الصمامات للاستخدام المدني
- قطع غيار مضخة التفريغ KF
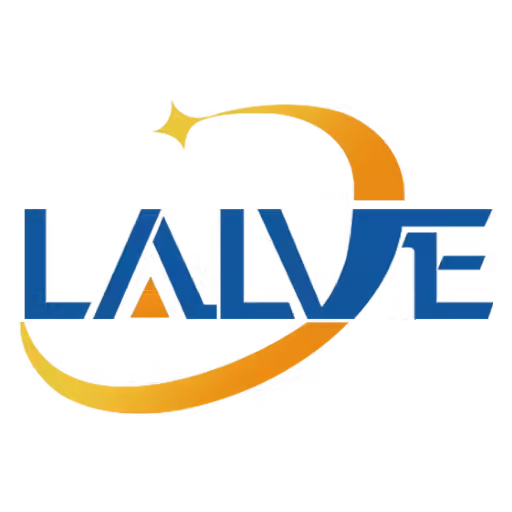