3 Essential Qualities of Sand Cast Impellers
Welcome to My Blog!
I’m thrilled to have you here! Before we dive into the content, I’d love for you to join me on my social media platforms. It’s where I share extra insights, connect with our amazing community, and keep you updated on the latest news. Here’s how you can stay connected:
📘 Facebook: Shanghai Leierwo Industry Trade Co., Ltd.
Now, let’s embark on this journey together! I hope you find the content here not only insightful but also inspiring and valuable. Let’s get started!
Table of Contents
Introduction
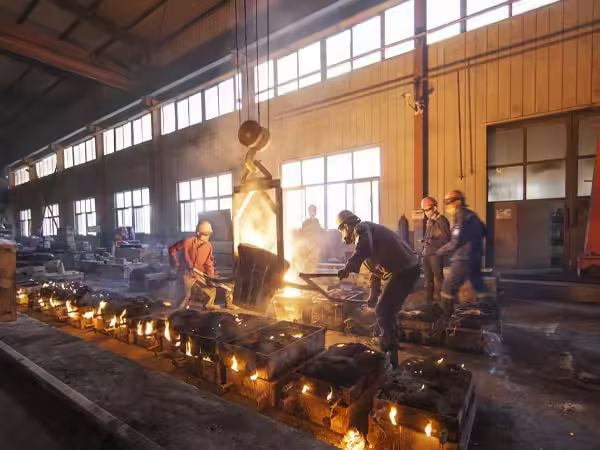
In the world of industrial manufacturing, impellers are crucial components used in pumps, compressors, and various fluid-handling equipment. Among the various manufacturing methods, sand casting remains a popular choice for producing impellers due to its cost-efficiency and design flexibility. This blog delves into the essential qualities of sand cast impellers and explores why they remain a reliable choice across multiple industries.
By examining sand cast impellers, we can better understand the characteristics that define their performance and longevity. This article will focus on three core qualities that every high-performance impeller must exhibit: dimensional accuracy, material integrity, and mechanical performance. Each of these elements plays a pivotal role in ensuring that the final product meets operational demands.
Dimensional Accuracy of Sand Cast Impellers
Dimensional accuracy plays a pivotal role in determining the operational success of components produced via sand casting, especially impellers. These parts are often deployed in high-performance systems where precise measurements ensure proper fitment within casings and seamless interaction with adjoining mechanisms.
Traditional sand molding techniques are inherently susceptible to variations. Factors such as thermal contraction, mold wear, and manual inconsistencies can influence the final geometry. However, recent advancements in pattern design, computer-aided mold modeling, and improved refractory materials have drastically enhanced precision levels. Nowadays, tolerances fall within acceptable industrial margins, making these components reliable for numerous critical tasks.
Moreover, dimensional accuracy is crucial when producing impellers for systems that operate under high pressure or velocity. Impellers with dimensional deviations can cause turbulence, vibration, or misalignment, all of which contribute to reduced efficiency and increased maintenance. Inaccuracies in blade profiles or hub geometries can disrupt fluid flow, reducing output and potentially damaging adjacent components. Therefore, modern casting operations often incorporate 3D modeling and simulation tools to predict dimensional shrinkage and adjust mold designs accordingly.
Additionally, dimensional repeatability across multiple production runs is important for industries that require interchangeable parts. Variations in geometry between batches can complicate assembly, leading to increased downtime and added costs. As such, quality control protocols including coordinate measuring machines (CMM) and laser scanning are often used to ensure conformity to design specifications.
Maintaining precise dimensions helps optimize flow characteristics, reduce premature wear, and enhance energy efficiency. This is particularly crucial in high-velocity rotating systems, where even minimal imbalance can result in excessive vibration, inefficient operation, and potentially catastrophic failures.
Material Integrity in Sand Cast Impellers
Material integrity addresses the internal consistency and soundness of the alloy used in crafting impellers through sand-based casting processes. Given that casting can introduce flaws such as gas porosity, slag inclusions, or fine cracks, ensuring a homogenous and defect-free structure becomes essential for long-term reliability.
Material selection is equally critical. Alloys like stainless steel, bronze, and nickel-based variants are commonly employed, each with their specific performance traits. These range from corrosion resistance and thermal endurance to tensile strength.
The following table compares the attributes of frequently used materials:
Material Type | Corrosion Resistance | Tensile Strength (MPa) | Common Applications |
---|---|---|---|
Stainless Steel | High | 480-620 | Marine, Chemical Processing |
Bronze | Moderate | 310-370 | Water Pumps, HVAC |
Nickel-Based Alloy | Very High | 620-900 | Aerospace, High-Temp Systems |
To ensure structural soundness, manufacturers commonly implement non-destructive evaluation methods such as ultrasonic scanning or X-ray inspection. These processes help in detecting internal flaws before the components are deployed, ensuring safety and consistency in critical environments.
Furthermore, metal quality control begins at the foundry level, where raw materials are analyzed for chemical composition. Advanced spectrometry tools ensure that alloying elements like chromium, nickel, or molybdenum are present in correct proportions, guaranteeing mechanical performance and corrosion resistance. Degassing treatments and filtration systems are also employed during the casting process to remove trapped gases and impurities.
Post-casting, heat treatments such as annealing, quenching, and tempering further enhance the material’s internal grain structure, improving ductility, toughness, and fatigue life. These processes ensure the impeller will function reliably under a range of thermal and mechanical stresses.
Mechanical Performance of Sand Cast Impellers
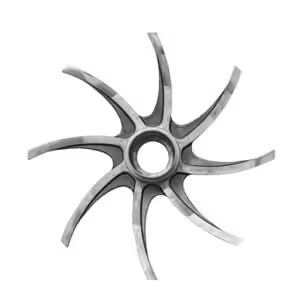
The mechanical behavior of an impeller determines its ability to withstand dynamic stresses encountered during service. Key parameters include resistance to fatigue, durability under impact, and surface hardness. These qualities are particularly important when the component operates in environments exposed to rapid rotation, pressure surges, and fluid-borne abrasives.
Consistent exposure to mechanical loads can lead to stress-induced degradation. Therefore, strong fatigue resistance is essential, especially for systems that operate continuously. High impact strength is also vital, as impellers may experience occasional solid particle collisions or cavitation effects.
The sand casting technique permits variable thicknesses, which allow engineers to design reinforced zones in stress-prone regions. In addition, proper heat treatments post-production can improve grain alignment and metallurgical consistency, leading to better performance metrics across fatigue life, resilience, and reliability.
Surface finishing also plays a key role in mechanical performance. As-cast surfaces are often rough and may include micro-defects that can serve as initiation points for fatigue cracks. Techniques such as shot blasting, grinding, or machining are applied to improve surface finish and remove imperfections. In some applications, coatings such as ceramic layers or hard chrome plating may be applied to enhance wear resistance and reduce friction.
Finally, testing methods like dynamic balancing, tensile strength analysis, and endurance testing ensure that impellers meet or exceed the operational demands of their intended applications. This comprehensive approach to mechanical quality ensures impellers deliver consistent performance across a wide variety of conditions.
Applications Benefiting from Sand Cast Impellers
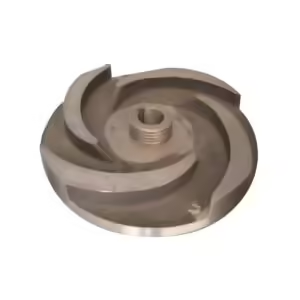
Due to their robust nature and adaptability, these impellers find use in a wide array of mechanical systems. Their longevity and effectiveness are underpinned by the structural and material characteristics discussed earlier.
Common implementations include:
- Industrial and agricultural centrifugal pump assemblies
- Heating, ventilation, and air conditioning (HVAC) systems
- Equipment for handling corrosive fluids in oil and gas sectors
- Propulsion and circulation systems in marine settings
- Food-grade processing units requiring hygienic and corrosion-resistant materials
- Fire suppression and municipal water treatment systems
- Chemical reactors and fertilizer mixing applications
Each of these environments presents unique challenges, including variable flow conditions, temperature fluctuations, exposure to abrasive or corrosive substances, and continuous duty cycles. Sand cast impellers, when properly engineered, can deliver the durability and performance necessary to meet such demands reliably.
In agriculture, for instance, impellers are used in irrigation pumps that must endure prolonged operation in outdoor conditions. In the oil and gas industry, impellers are exposed to aggressive chemicals and high pressures, demanding excellent corrosion resistance and mechanical resilience. Meanwhile, in food processing, compliance with hygiene standards is critical, and stainless steel cast impellers meet these requirements while also delivering reliable performance.
These scenarios highlight the significance of quality assurance in casting and underscore why maintaining dimensional fidelity, structural soundness, and mechanical strength is non-negotiable.asizing the importance of material and design customization.th is non-negotiable.
Conclusion
The enduring popularity of sand cast impellers stems from their proven ability to meet diverse performance demands in industrial settings. Their dimensional accuracy ensures compatibility and operational smoothness; material integrity guards against failure from internal flaws; and their mechanical performance allows them to withstand harsh environments.
With continuous advancements in casting technology, sand cast impellers remain an economical and efficient choice for manufacturers needing reliable components. Understanding the three essential qualities outlined in this article helps stakeholders make informed decisions when designing or selecting impellers for their systems.
FAQ
What is the advantage of sand casting for impellers?
Sand casting is cost-effective and allows for complex geometries and large-sized impellers that would be expensive or difficult to produce using other methods.
Are sand cast impellers suitable for high-speed applications?
Yes, as long as the impeller has high dimensional accuracy and material integrity, it can be used in high-speed environments with minimal vibration and wear.
How can defects in sand cast impellers be detected?
Non-destructive testing methods such as X-ray, dye penetrant, and ultrasonic inspection are used to detect internal and surface flaws.
What materials are best for corrosion resistance?
Nickel-based alloys and certain grades of stainless steel offer excellent corrosion resistance, making them ideal for marine or chemical environments.
Can sand cast impellers be customized?
The chosen alloy influences corrosion resistance, temperature tolerance, and mechanical strength. For example, nickel-based alloys offer superior high-temperature performance, while bronze provides moderate corrosion resistance in less aggressive environments. Alloy selection should be tailored to the application’s demands.
Product Categories
- Valve Parts
- Water Pump Parts
- Bearing Box Parts
- Die Casting Parts
- Stainless Steel Pump Products
- Cast Iron Pump Products
- Valve Parts For Automobile Use
- Auto Parts
- Valve Parts For Civil Use
- Vacuum Pump Parts KF
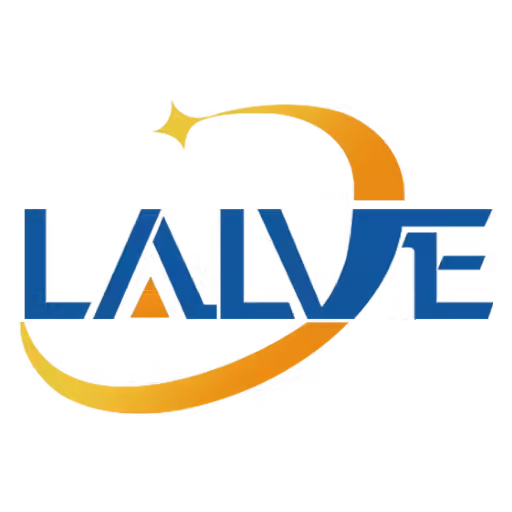